Hot isostatic pressing (HIP) is a manufacturing process used to improve the properties of materials, particularly metals and ceramics, by applying high temperature and uniform pressure. This process is essential for enhancing material density, mechanical performance, and resistance to wear and corrosion. It is widely used in industries such as aerospace, automotive, and medical devices, where high-performance materials are critical. HIP is also increasingly integrated with advanced manufacturing techniques like 3D printing to address issues such as porosity and poor layer adhesion, while reducing production time and costs. The process involves several steps, including powder preparation, cladding design, and controlled heating and pressurization, followed by cooling and post-processing.
Key Points Explained:
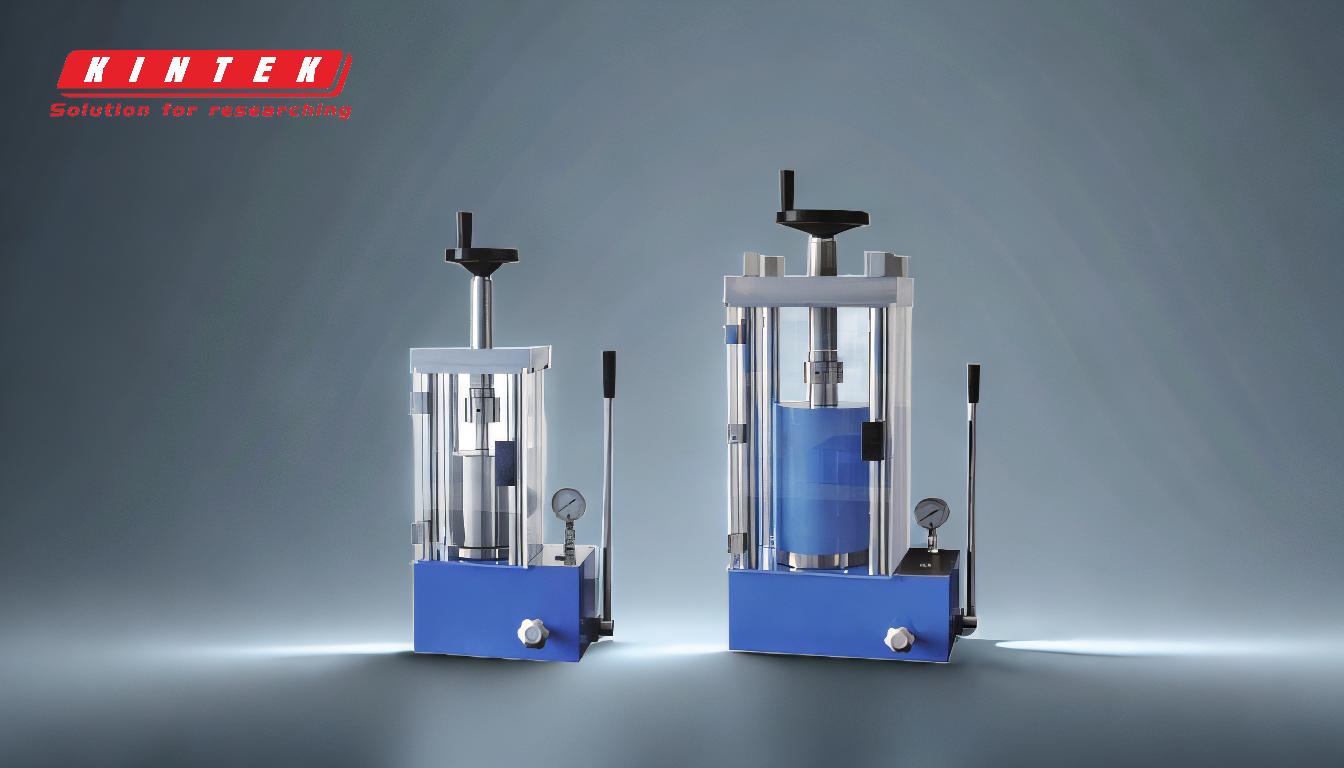
-
Definition and Purpose of Hot Isostatic Pressing (HIP):
- HIP is a process that uses high temperature and uniform hydrostatic pressure to improve the properties of materials. It is particularly effective in bonding materials, reducing porosity, and enhancing mechanical performance. This makes it invaluable for industries requiring high-strength, durable components.
-
Process Steps:
- The HIP process involves several key stages:
- Powder Preparation: Raw materials are prepared in powder form.
- Cladding Design and Manufacturing: A flexible mold or cladding is designed to hold the powder.
- Powder Filling and Degassing Sealing: The powder is loaded into the cladding, and air is removed to prevent contamination.
- Hot Isostatic Pressing: The sealed cladding is placed in a pressure vessel, where it is subjected to high temperature and pressure.
- Removal of Cladding: After processing, the cladding is removed.
- Subsequent Processing: Final machining or heat treatment may be applied to achieve the desired properties.
- The HIP process involves several key stages:
-
Benefits of HIP:
- Improved Material Properties: HIP significantly enhances wear resistance, corrosion resistance, and mechanical performance. It can increase fatigue life by 10 to 100 times.
- Increased Density: The process achieves material densities close to the theoretical maximum, reducing defects like porosity.
- Stress Relief: HIP relieves thermal stresses in cast, sintered, and additively manufactured parts, improving their structural integrity.
- Combined Manufacturing Steps: HIP integrates heat treatment, quenching, and aging processes, reducing overall production time and costs.
-
Applications in Advanced Manufacturing:
- HIP is increasingly used alongside 3D printing to address challenges such as porosity and poor layer adhesion in additive manufacturing. This combination reduces production time and costs while improving part quality.
- It is also used in the production of complex geometries and high-performance components for industries like aerospace and medical devices.
-
Techniques in Isostatic Pressing:
- HIP can be performed using two main techniques:
- Wet-Bag Technique: The flexible mold containing the powder is submerged in a pressure vessel filled with a pressurizing fluid.
- Dry-Bag Technique: The flexible mold is fixed in the pressure vessel, and powder is loaded without removing the mold.
- HIP can be performed using two main techniques:
-
Process Control:
- During HIP, inert argon gas is used to apply pressure, and the temperature, pressure, and process time are closely monitored. The process concludes with a controlled depressurization and cooling phase to ensure the safety and integrity of the parts.
-
Impact on Manufacturing Efficiency:
- By combining HIP with other manufacturing techniques, such as 3D printing, the overall production time and cost are dramatically reduced. This makes HIP a valuable process for producing high-quality components efficiently.
In summary, hot isostatic pressing is a versatile and powerful process that enhances material properties, reduces defects, and streamlines manufacturing. Its integration with advanced techniques like 3D printing further expands its applications, making it a critical tool in modern manufacturing.
Summary Table:
Key Aspect | Details |
---|---|
Purpose | Improves material properties like density, wear resistance, and strength. |
Process Steps | Powder preparation, cladding design, HIP treatment, and post-processing. |
Benefits | Reduces porosity, enhances fatigue life, and integrates manufacturing steps. |
Applications | Aerospace, automotive, medical devices, and 3D printing. |
Techniques | Wet-bag and dry-bag methods for isostatic pressing. |
Learn how hot isostatic pressing can transform your manufacturing process—contact us today for expert guidance!