Hot press molding is a manufacturing process that involves the application of heat and pressure to shape materials into a desired form. This technique is widely used in industries such as automotive, aerospace, and electronics to produce high-strength, lightweight components. The process typically involves placing a material, such as a composite or polymer, into a mold and then applying heat and pressure using a hot press machine. The material is then cured or solidified under these conditions, resulting in a finished product with precise dimensions and properties. Hot press molding is valued for its ability to produce complex shapes with high accuracy and repeatability, making it a preferred method for high-performance applications.
Key Points Explained:
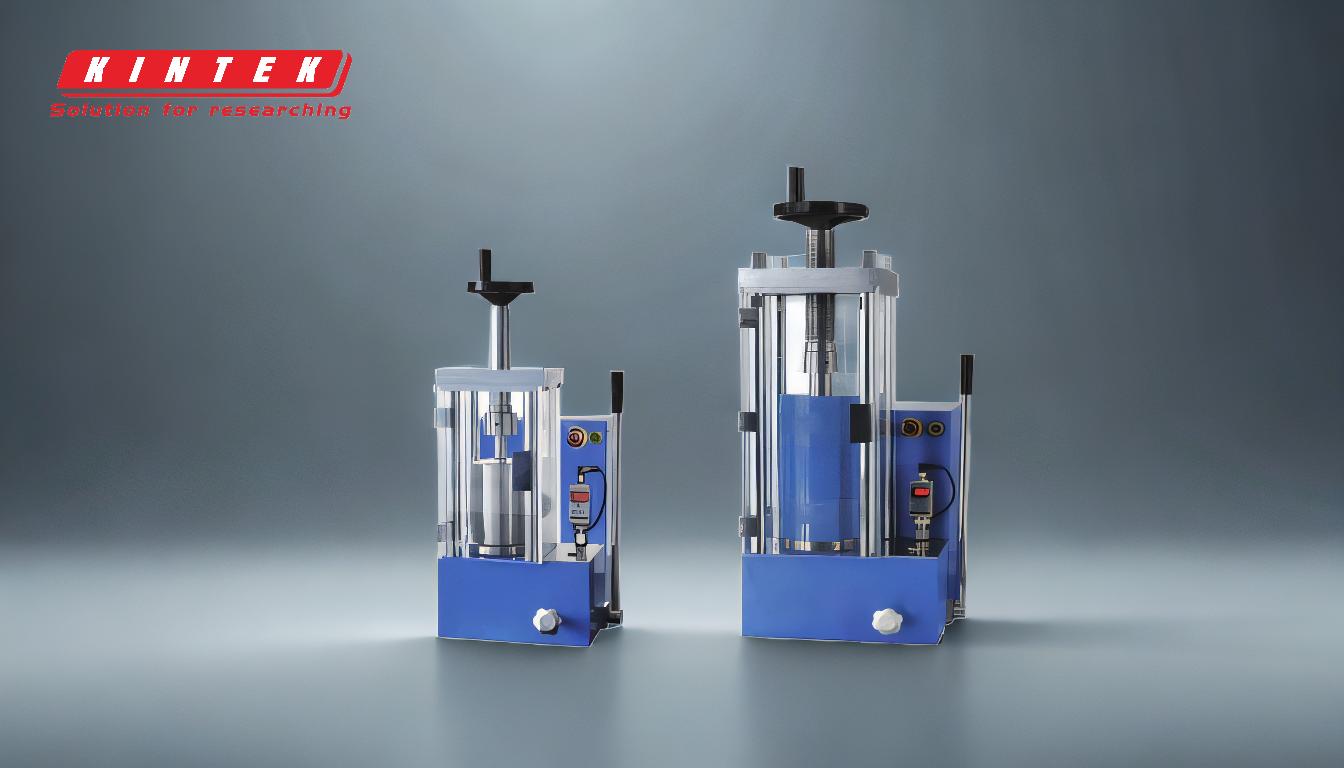
-
Definition of Hot Press Molding:
- Hot press molding is a manufacturing process that uses heat and pressure to shape materials. It is commonly used for creating components from composites, polymers, and other materials that require precise shaping and curing.
-
Role of the Hot Press Machine:
- The hot press machine is the core equipment used in this process. It applies both heat and pressure to the material within the mold, ensuring that the material is evenly distributed and properly cured. The machine typically consists of heated platens that press the material into the desired shape.
-
Materials Used in Hot Press Molding:
- Common materials include thermoset resins, thermoplastic polymers, and composite materials. These materials are chosen for their ability to withstand the high temperatures and pressures involved in the process, as well as for their final mechanical properties.
-
Process Steps:
- Preparation: The material is prepared and placed into the mold.
- Heating and Pressing: The mold is placed in the hot press machine, where heat and pressure are applied.
- Curing: The material is allowed to cure or solidify under the applied conditions.
- Cooling and Ejection: The mold is cooled, and the finished product is ejected.
-
Advantages of Hot Press Molding:
- High Precision: The process allows for the production of components with tight tolerances and complex geometries.
- Material Efficiency: Minimal waste is generated, as the material is precisely shaped.
- Strength and Durability: The resulting products have high mechanical strength and durability, making them suitable for demanding applications.
-
Applications:
- Hot press molding is used in various industries, including automotive (for parts like dashboards and interior panels), aerospace (for lightweight structural components), and electronics (for enclosures and insulators).
-
Considerations for Purchasers:
- When selecting a hot press machine, consider factors such as the maximum temperature and pressure capabilities, the size of the platens, and the control system for precise regulation of the process parameters.
By understanding these key points, purchasers can make informed decisions about the equipment and materials needed for hot press molding, ensuring that they achieve the desired results in their manufacturing processes.
Summary Table:
Aspect | Details |
---|---|
Definition | A manufacturing process using heat and pressure to shape materials. |
Key Equipment | Hot press machine for applying heat and pressure. |
Common Materials | Thermoset resins, thermoplastic polymers, and composite materials. |
Process Steps | Preparation, heating/pressing, curing, cooling/ejection. |
Advantages | High precision, material efficiency, strength, and durability. |
Applications | Automotive, aerospace, and electronics industries. |
Purchasing Tips | Consider temperature, pressure, platen size, and control system. |
Discover how hot press molding can enhance your manufacturing process—contact us today for expert advice!