Hydraulic forging is a manufacturing process that uses hydraulic pressure to shape metal into desired forms. This method is particularly effective for creating complex and high-strength components, often used in industries such as aerospace, automotive, and heavy machinery. The process involves placing a metal workpiece between two dies and applying immense hydraulic pressure to deform the metal into the shape of the dies. Hydraulic forging is known for its precision, ability to handle large workpieces, and the production of parts with superior mechanical properties. It is a versatile technique that can be used for both open-die and closed-die forging, making it suitable for a wide range of applications.
Key Points Explained:
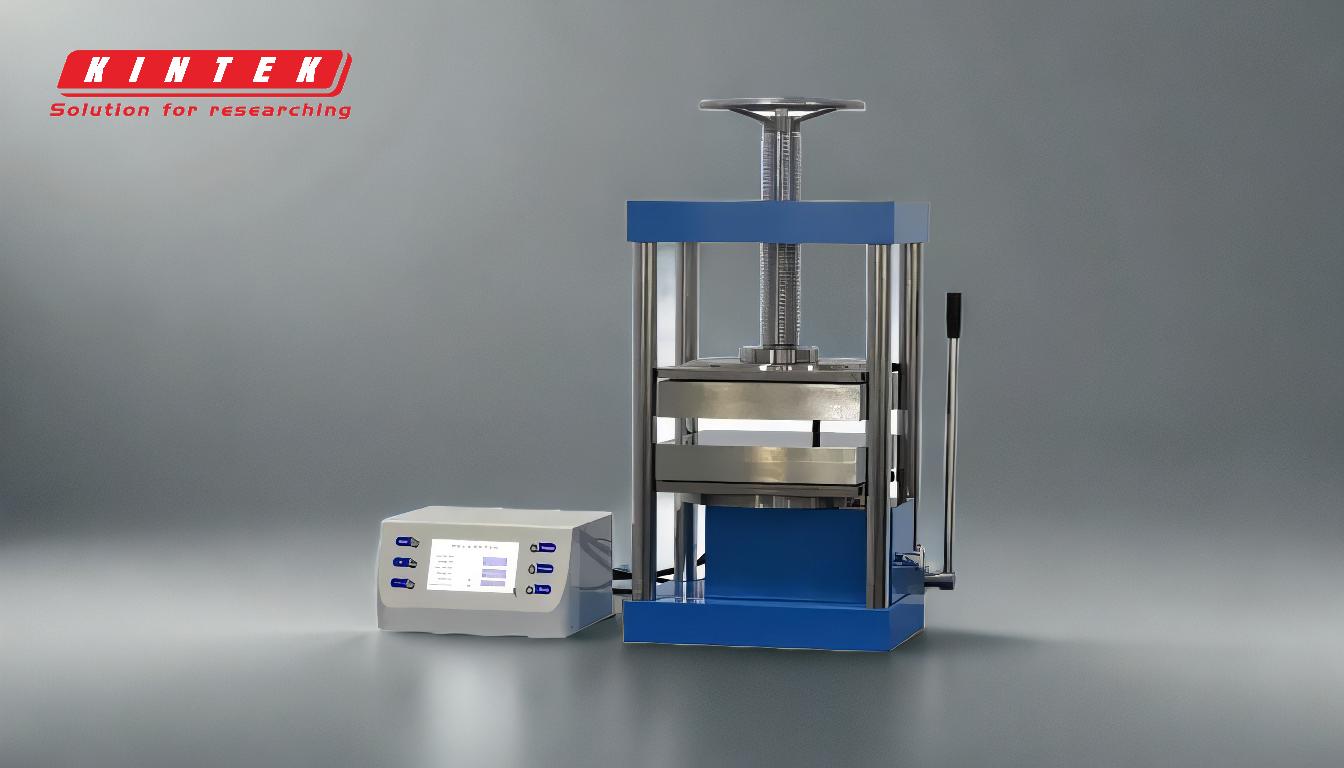
-
Definition and Process of Hydraulic Forging:
- Hydraulic forging is a metalworking process where hydraulic pressure is used to shape metal into specific forms. The process typically involves placing a metal workpiece between two dies and applying high-pressure hydraulic force to deform the metal into the desired shape. This method is particularly useful for creating complex geometries and high-strength components.
-
Types of Hydraulic Forging:
- Open-Die Forging: In this type, the metal is placed between flat or simple-shaped dies, and the hydraulic press applies pressure to shape the metal. Open-die forging is often used for large or custom-shaped components.
- Closed-Die Forging: Also known as impression-die forging, this method uses dies that have a specific shape or impression. The metal is forced into the die cavities under high pressure, resulting in precise and detailed parts.
-
Advantages of Hydraulic Forging:
- Precision and Accuracy: Hydraulic forging allows for precise control over the shaping process, resulting in components with tight tolerances and high accuracy.
- High Strength and Durability: The process enhances the mechanical properties of the metal, such as strength, toughness, and fatigue resistance, making it ideal for critical applications.
- Versatility: Hydraulic forging can be used with a wide range of metals, including steel, aluminum, titanium, and alloys, making it suitable for various industries.
- Efficiency: The process is highly efficient, especially for large-scale production, as it can produce complex parts in a single operation.
-
Applications of Hydraulic Forging:
- Aerospace: Hydraulic forging is used to produce high-strength components such as turbine blades, landing gear, and structural parts.
- Automotive: The process is employed to manufacture critical parts like crankshafts, connecting rods, and transmission components.
- Heavy Machinery: Hydraulic forging is used to create large, durable parts for construction equipment, mining machinery, and industrial tools.
-
Comparison with Other Forging Methods:
- Hydraulic vs. Mechanical Forging: Hydraulic forging offers better control over the deformation process, allowing for more complex shapes and finer details. Mechanical forging, on the other hand, is faster but less precise.
- Hydraulic vs. Hammer Forging: Hydraulic forging provides a more consistent and controlled force application, resulting in uniform material properties. Hammer forging, while effective for certain applications, can lead to variations in material density and strength.
-
Challenges and Considerations:
- Cost: Hydraulic forging equipment and tooling can be expensive, making it less suitable for small-scale production.
- Material Limitations: While hydraulic forging is versatile, certain materials may not be suitable for this process due to their brittleness or other properties.
- Maintenance: The hydraulic systems require regular maintenance to ensure consistent performance and prevent downtime.
In summary, hydraulic forging is a highly effective and versatile metalworking process that offers numerous advantages in terms of precision, strength, and efficiency. It is widely used in industries that require high-performance components and is particularly valued for its ability to produce complex and durable parts. However, it is important to consider the cost and material limitations when choosing this method for specific applications.
Summary Table:
Aspect | Details |
---|---|
Definition | Uses hydraulic pressure to shape metal into desired forms. |
Types | Open-die forging (flat/simple dies) and closed-die forging (specific dies). |
Advantages | Precision, high strength, versatility, and efficiency. |
Applications | Aerospace, automotive, and heavy machinery. |
Challenges | High cost, material limitations, and maintenance requirements. |
Learn how hydraulic forging can enhance your manufacturing process—contact us today!