Isostatic pressing is a manufacturing process that applies uniform hydrostatic pressure to materials, typically powders, enclosed in a flexible mold. This technique, based on Pascal’s law, ensures consistent pressure from all directions, eliminating frictional forces and improving density uniformity. It is widely used in various industries, including battery production, ceramics, and metallurgy. Cold isostatic pressing (CIP) and hot isostatic pressing (HIP) are the two main types, with CIP performed at ambient temperatures and HIP at elevated temperatures. CIP is particularly useful for creating thin, dense solid electrolyte layers and integrating multi-layer systems for solid-state batteries (SSBs). The process involves placing powder in a mold, submerging it in a liquid medium, and applying high pressure to achieve a uniform product.
Key Points Explained:
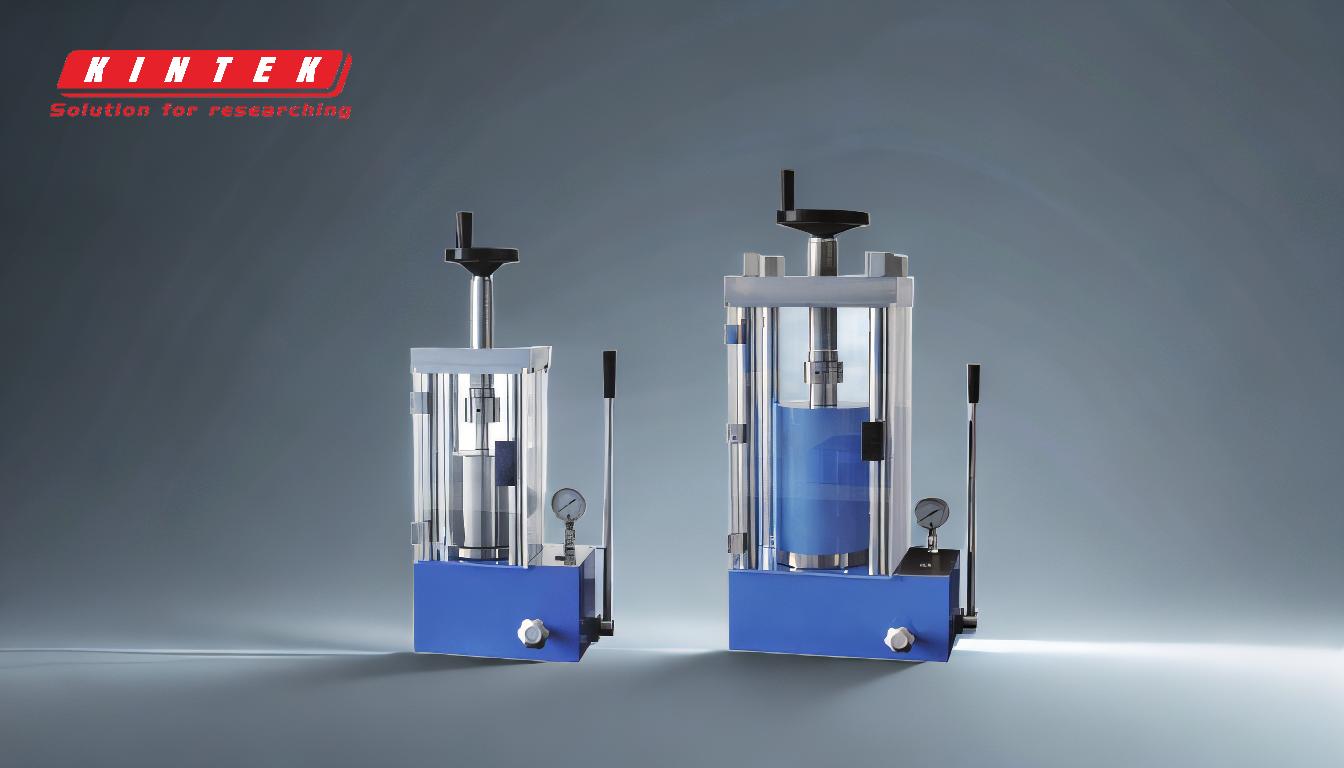
-
Definition and Principle of Isostatic Pressing:
- Isostatic pressing is a technique that applies uniform pressure in all directions to compact materials, typically powders, using a flexible mold. This process is based on Pascal’s law, which states that pressure applied to a confined fluid is transmitted equally in all directions. This uniformity eliminates frictional forces that hinder conventional pressing methods, resulting in improved density and material consistency.
-
Types of Isostatic Pressing:
-
Cold Isostatic Pressing (CIP): Performed at ambient temperatures, CIP is used to compact green parts (unfired ceramic or metal powders) into dense shapes. It is divided into two methods:
- Wet Bag Method: The mold is submerged in a liquid medium, and pressure is applied uniformly.
- Dry Bag Method: The mold is fixed within the pressure vessel, and the liquid medium is pumped directly into the mold.
- Hot Isostatic Pressing (HIP): Conducted at elevated temperatures, HIP uses solid-state diffusion to fully consolidate parts, often used for densifying metals and ceramics.
-
Cold Isostatic Pressing (CIP): Performed at ambient temperatures, CIP is used to compact green parts (unfired ceramic or metal powders) into dense shapes. It is divided into two methods:
-
Applications of Cold Isostatic Pressing:
- CIP is widely used in industries such as:
- Refractory Materials: Production of nozzles, blocks, and crucibles.
- Ceramics: Manufacturing of insulators, tubes, and ferrites.
- Metals: Creation of preforms, filters, and cemented carbides.
- Battery Production: Generating thin, dense solid electrolyte layers and integrating multi-layer systems for solid-state batteries (SSBs).
- CIP is widely used in industries such as:
-
Process of Cold Isostatic Pressing:
- In CIP, the powder material is placed in a flexible mold and inserted into a high-pressure chamber. A liquid medium, often an oil-water mixture, is pumped into the chamber and pressurized uniformly on all sides. The pressure can reach up to 100,000 psi, ensuring a highly uniform and dense product.
-
Advantages of Isostatic Pressing:
- Uniform Density: Eliminates frictional forces, resulting in consistent material density.
- Versatility: Suitable for a wide range of materials and shapes.
- Improved Performance: Enhances the mechanical and electrical properties of the final product, especially in battery applications.
- Efficiency: Simplifies and accelerates production processes, such as battery manufacturing.
-
Role in Battery Production:
- Isostatic pressing, particularly CIP, plays a crucial role in the production of solid-state batteries (SSBs). It enables the creation of thin, dense solid electrolyte layers and the integration of cathode, solid electrolyte, and anode layers into a dense, tri-layer system. This improves energy flow and overall battery performance.
-
Equipment Used:
- The cold isostatic pressing machine is a key piece of equipment in this process. It consists of a high-pressure chamber, a hydraulic system, and a liquid medium delivery system. The machine ensures uniform pressure application, making it essential for producing high-quality, dense materials.
By leveraging the principles of isostatic pressing, manufacturers can achieve superior material properties and streamline production processes, particularly in advanced applications like solid-state batteries.
Summary Table:
Aspect | Details |
---|---|
Definition | A process applying uniform hydrostatic pressure to materials using a mold. |
Types | Cold Isostatic Pressing (CIP) and Hot Isostatic Pressing (HIP). |
Applications | Battery production, ceramics, metallurgy, and refractory materials. |
Advantages | Uniform density, versatility, improved performance, and efficiency. |
Key Equipment | Cold isostatic pressing machine for high-pressure, uniform compaction. |
Learn how isostatic pressing can optimize your manufacturing process—contact our experts today!