Isostatic pressing, particularly the cold isostatic pressing method, is a versatile and efficient technique used in the manufacturing of ceramics and other materials. This method involves applying uniform pressure from all directions to a material, typically in powder form, using a high-pressure fluid medium. It is especially useful for creating intricate shapes and achieving high green density without the need for lubricants. The process is suitable for large parts that do not require high precision post-sintering and is widely used in industries such as ceramics, metals, and composites. The advantages include uniform pressure distribution, high material utilization, and the ability to handle difficult-to-compact materials.
Key Points Explained:
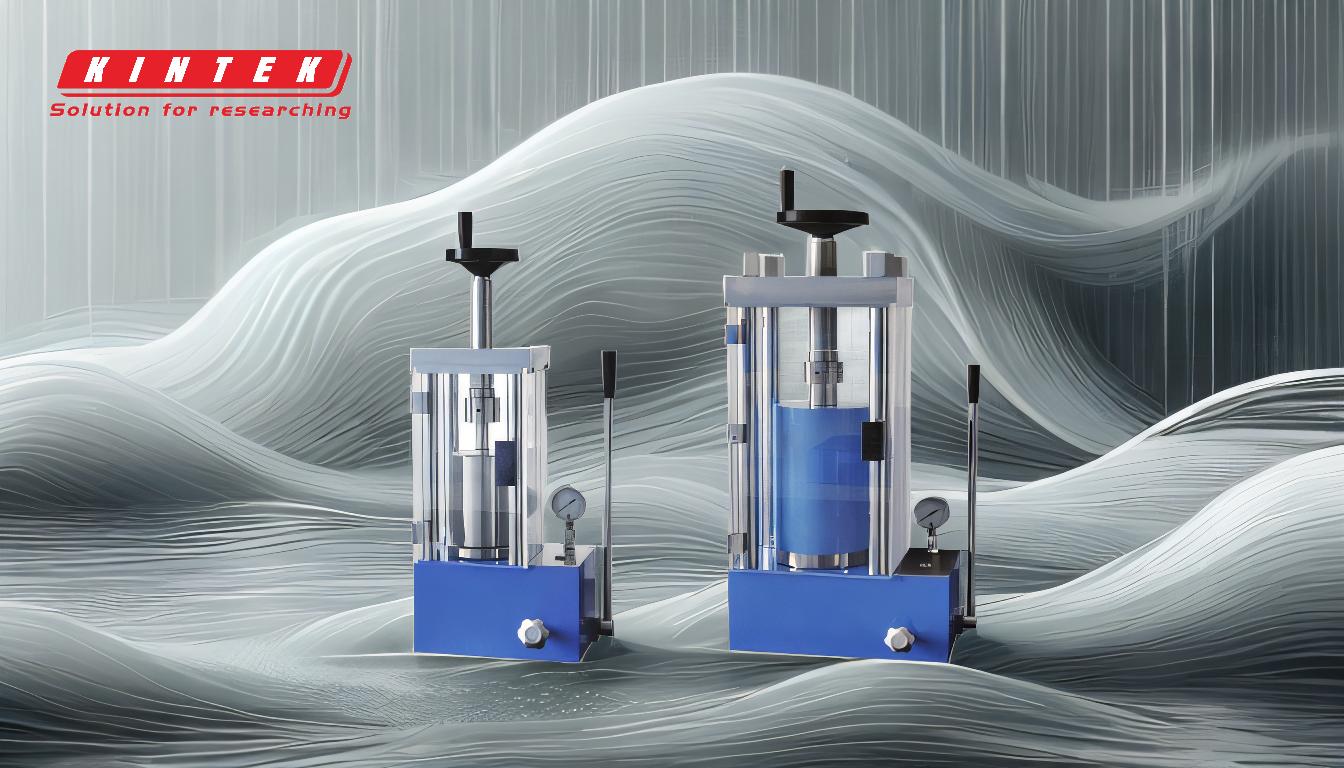
-
Definition and Process of Cold Isostatic Pressing:
- Cold Isostatic Pressing (CIP) involves placing a powdered material in a flexible mold and then subjecting it to uniform pressure from all sides. This is achieved by immersing the mold in a high-pressure fluid medium, typically water or oil, and applying hydraulic pressure. The uniform pressure ensures that the powder is compacted evenly, resulting in a high green density and intricate shapes.
- This method is particularly effective for materials that are difficult to compact using traditional uniaxial pressing methods. It is also beneficial for large parts that do not require high precision after sintering.
-
Applications of Cold Isostatic Pressing:
- CIP is widely used in the consolidation of powders and the defect healing of castings. It is applied to a range of materials including ceramics, metals, composites, plastics, and carbon. For example, it is used in the production of graphite blocks where powdered carbon is placed in large molds and subjected to high pressure (over 150 MPa) to ensure uniform physical parameters.
- In the ceramic industry, CIP is used to create parts that are too large for uniaxial presses and do not require high precision in the sintered state. It is also used for wear and metal forming tools.
-
Advantages of Cold Isostatic Pressing:
- Uniform Pressure Distribution: The pressure is applied uniformly from all directions, which ensures even compaction of the powder and eliminates the need for lubricants.
- High and Uniform Density: CIP achieves high green density, which is crucial for the subsequent sintering process.
- Versatility in Part Geometry: There are no constraints on the geometry of the parts, allowing for the creation of intricate shapes.
- Efficient Material Utilization: This method is particularly efficient for difficult-to-compact and expensive materials like superalloys, titanium, and stainless steel.
-
Comparison with Hot Isostatic Pressing:
- While Cold Isostatic Pressing is performed at room temperature, Hot Isostatic Pressing (HIP) involves applying external pressure along with high temperature to achieve densification. HIP is typically used for 3D shapes and is a variant of sintering. Both methods offer the advantage of uniform pressure distribution but are used in different contexts based on the material and the desired outcome.
-
Industrial Applications:
- Beyond ceramics, CIP is used in various industries such as furniture production, wooden glued pressing parts (like speakers), and in sectors like decoration, plastics, plane plywood, plywood, particleboard, and veneer. It is suitable for flattening, bonding, veneering, and pressing plates at normal temperature, offering high production efficiency and excellent quality.
-
Equipment and Consumables:
- The key equipment used in CIP is the cold isostatic pressing machine, which is designed to apply uniform hydraulic pressure to the material. The consumables include the flexible molds and the high-pressure fluid medium, which are essential for the process.
In conclusion, Cold Isostatic Pressing is a highly effective method for shaping and consolidating powdered materials, particularly in the ceramics industry. Its ability to apply uniform pressure from all directions, achieve high green density, and handle complex geometries makes it a valuable technique in various manufacturing processes.
Summary Table:
Aspect | Details |
---|---|
Process | Uniform pressure applied from all directions using a high-pressure fluid. |
Applications | Ceramics, metals, composites, plastics, and carbon. |
Advantages | - Uniform pressure distribution - High green density - Versatile geometries |
Equipment | Cold isostatic pressing machine, flexible molds, and high-pressure fluid. |
Industries | Ceramics, furniture, decoration, plastics, and more. |
Ready to enhance your manufacturing process? Contact us today to learn more about cold isostatic pressing solutions!