Low Pressure Chemical Vapor Deposition (LPCVD) is a specialized chemical vapor deposition (CVD) technique used to deposit thin films of material onto a substrate. It operates at reduced pressures (typically below 133 Pa or 0.1–10 Torr) and moderate temperatures (200–800°C), which enhances the efficiency of the deposition process. LPCVD relies on heat to initiate chemical reactions between precursor gases and the substrate surface, resulting in the formation of a solid-phase material. This method is widely used in industries such as electronics, where it deposits thin films on semiconductors, and in manufacturing processes like creating thin-film solar cells or protective coatings for cutting tools. The reduced pressure environment increases the mean free path of gas molecules, accelerates mass transfer, and improves the uniformity and quality of the deposited films.
Key Points Explained:
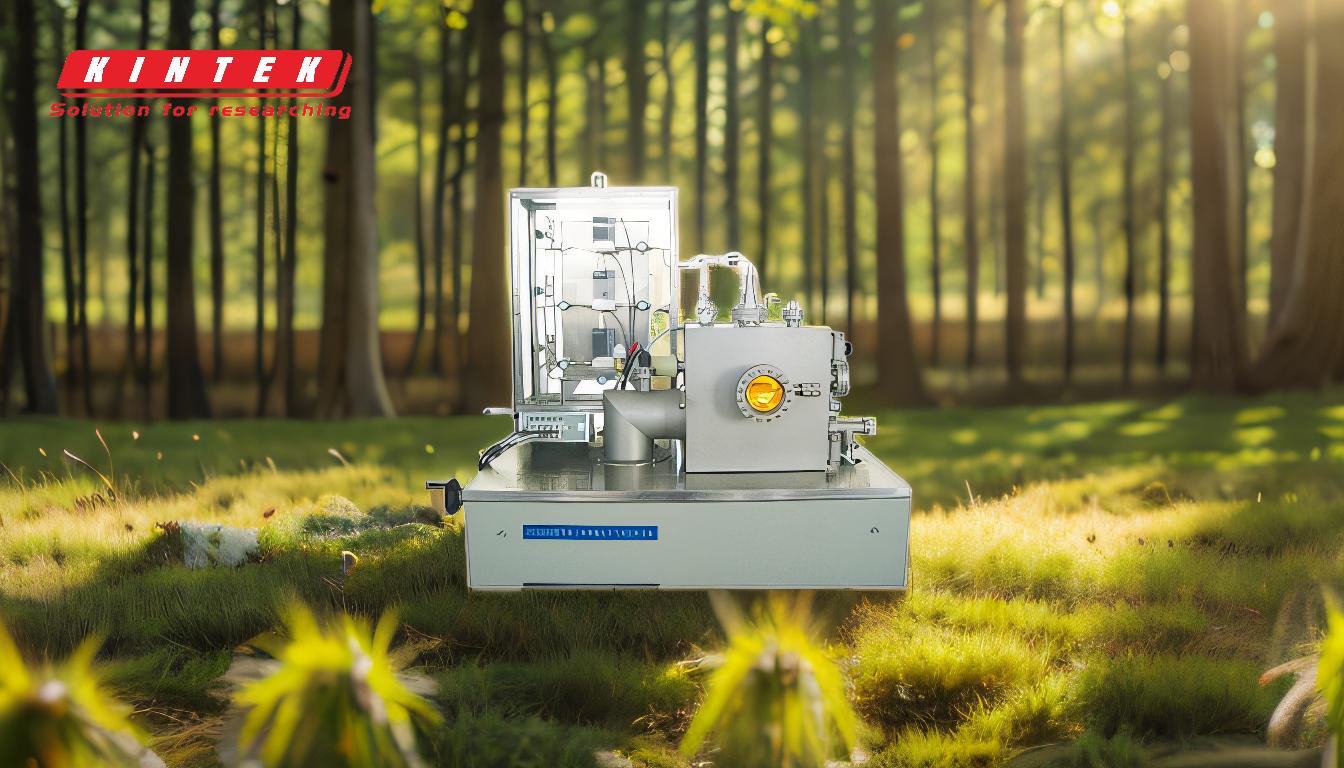
-
Definition and Purpose of LPCVD:
- LPCVD is a type of chemical vapor deposition that operates at low pressures (below 133 Pa or 0.1–10 Torr) and moderate temperatures (200–800°C).
- Its primary purpose is to deposit thin, uniform films of material onto a substrate through controlled chemical reactions between precursor gases and the substrate surface.
-
How LPCVD Works:
- Precursor Gases: Reactant gases are introduced into a vacuum chamber containing the substrate.
- Heat Activation: The substrate is heated to promote surface reactions, causing the precursor gases to decompose or react chemically.
- Film Formation: The reaction products form a solid film on the substrate surface.
- By-product Removal: Vacuum pumps remove gaseous by-products from the chamber, ensuring a clean deposition environment.
-
Advantages of Low Pressure:
- Reduced pressure increases the mean free path of gas molecules, allowing them to travel farther without collisions.
- This enhances the gas diffusion coefficient, accelerating the mass transfer of reactants and by-products.
- The result is improved film uniformity, better control over deposition rates, and higher-quality thin films.
-
Applications of LPCVD:
- Electronics: LPCVD is widely used to deposit thin films on semiconductors, such as silicon dioxide (SiO₂) and silicon nitride (Si₃N₄), which are essential for integrated circuits.
- Cutting Tools: It provides wear-resistant and corrosion-resistant coatings, extending the lifespan of tools.
- Solar Cells: LPCVD is used to deposit photovoltaic materials onto substrates for thin-film solar cells.
- Optics and MEMS: It is also employed in manufacturing optical coatings and microelectromechanical systems (MEMS).
-
Comparison to Other CVD Techniques:
- LPCVD operates at lower pressures than atmospheric pressure CVD (APCVD), which reduces contamination and improves film quality.
- Unlike plasma-enhanced CVD (PECVD), LPCVD relies solely on thermal energy rather than plasma to drive reactions, making it suitable for high-temperature substrates.
-
Process Parameters:
- Pressure: Typically 0.1–10 Torr (133–1333 Pa).
- Temperature: Ranges from 200–800°C, depending on the material being deposited.
- Precursor Delivery: Specialized systems ensure precise control over gas flow and composition.
- Vacuum System: High-performance pumps maintain low pressure and remove by-products.
-
Challenges and Considerations:
- Uniformity: Achieving uniform film thickness across large substrates can be challenging.
- Temperature Sensitivity: Some materials may degrade at high temperatures, limiting their use in LPCVD.
- Cost: The equipment and operational costs for LPCVD systems are relatively high compared to simpler deposition methods.
-
Future Trends:
- Advances in precursor chemistry and reactor design are improving the efficiency and scalability of LPCVD.
- The growing demand for advanced materials in electronics, renewable energy, and nanotechnology is driving further innovation in LPCVD technology.
In summary, LPCVD is a critical technology for depositing high-quality thin films in various industries. Its ability to operate at low pressures and moderate temperatures, combined with precise control over chemical reactions, makes it a versatile and reliable method for creating advanced materials and coatings.
Summary Table:
Aspect | Details |
---|---|
Definition | A CVD technique for depositing thin films at low pressures (0.1–10 Torr). |
Key Advantages | Improved film uniformity, better deposition control, and high-quality films. |
Applications | Semiconductors, solar cells, cutting tools, optics, and MEMS. |
Process Parameters | Pressure: 0.1–10 Torr; Temperature: 200–800°C. |
Challenges | Uniformity, temperature sensitivity, and high costs. |
Discover how LPCVD can enhance your manufacturing process—contact our experts today!