Vapor deposition is a process used to create thin films or coatings on a substrate by depositing material from a vaporized state. This technique is widely used in industries such as electronics, optics, and manufacturing to enhance surface properties like hardness, oxidation resistance, and friction reduction. There are two main types of vapor deposition: Physical Vapor Deposition (PVD) and Chemical Vapor Deposition (CVD). PVD involves physically vaporizing a solid material in a vacuum and depositing it onto a substrate, while CVD involves chemical reactions in the vapor phase to form a solid coating. Both methods are essential for creating precise and high-quality coatings.
Key Points Explained:
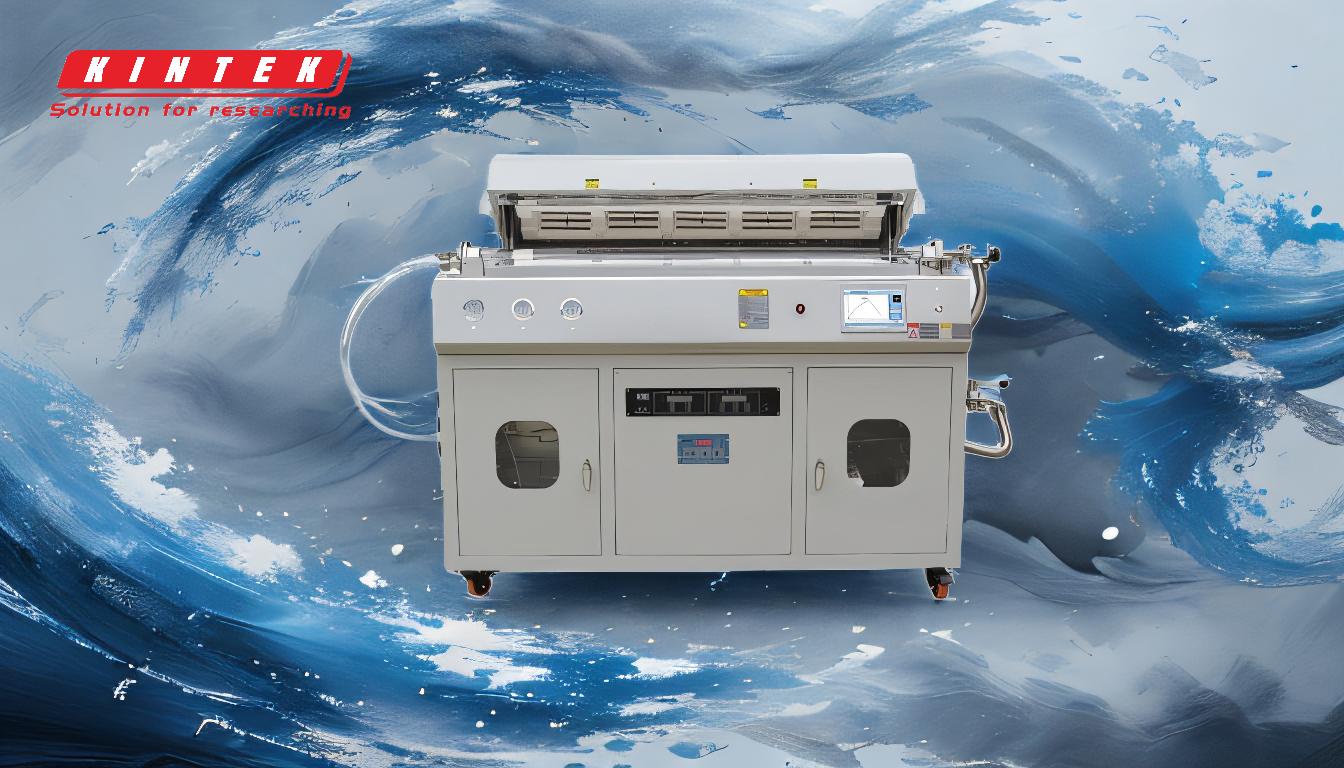
-
Definition of Vapor Deposition:
- Vapor deposition is a process where materials are deposited onto a substrate from a vaporized state. This technique is used to create thin films, coatings, and solid products. The process typically involves a heat source and a vacuum to ensure the material is vaporized and then deposited uniformly onto the substrate.
-
Types of Vapor Deposition:
-
Physical Vapor Deposition (PVD):
- PVD is a process conducted under vacuum conditions where a solid precursor material is bombarded with a beam of electrons to release atoms. These atoms then enter a reacting chamber where they may react with other gases or deposit directly onto the substrate, forming a thin coat. PVD is particularly useful for applications requiring reduced friction, improved oxidation resistance, and enhanced hardness.
-
Chemical Vapor Deposition (CVD):
- CVD involves chemical reactions in the vapor phase to form a solid coating on a substrate. This method is used for creating high-purity and high-performance solid materials. CVD is often used in the semiconductor industry to produce thin films of materials like silicon dioxide and silicon nitride.
-
Physical Vapor Deposition (PVD):
-
Applications of Vapor Deposition:
-
Electronics:
- Vapor deposition is crucial in the electronics industry for creating thin films used in semiconductors, integrated circuits, and other electronic components.
-
Optics:
- The technique is used to deposit anti-reflective coatings on lenses and other optical components.
-
Manufacturing:
- In manufacturing, vapor deposition is used to enhance the surface properties of tools and components, making them more durable and resistant to wear and corrosion.
-
Electronics:
-
Advantages of Vapor Deposition:
-
Precision:
- Vapor deposition allows for precise control over the thickness and composition of the deposited material, making it ideal for applications requiring high accuracy.
-
Uniformity:
- The process ensures a uniform coating, which is essential for consistent performance in various applications.
-
Versatility:
- Vapor deposition can be used with a wide range of materials, including metals, ceramics, and polymers, making it a versatile technique for different industries.
-
Precision:
-
Process Details:
-
Vacuum Environment:
- Both PVD and CVD processes are typically conducted in a vacuum to prevent contamination and ensure the purity of the deposited material.
-
Heat Source:
- A heat source is used to vaporize the material in PVD, while in CVD, heat is often used to drive the chemical reactions necessary for deposition.
-
Substrate Preparation:
- The substrate must be carefully prepared and cleaned to ensure proper adhesion of the deposited material.
-
Vacuum Environment:
In summary, vapor deposition is a versatile and precise technique used to create thin films and coatings on various substrates. It is essential in industries requiring high-performance materials with enhanced surface properties. The two main types, PVD and CVD, offer different advantages and are used based on the specific requirements of the application.
Summary Table:
Aspect | Details |
---|---|
Definition | Process of depositing materials from a vaporized state onto a substrate. |
Types | Physical Vapor Deposition (PVD) and Chemical Vapor Deposition (CVD). |
Applications | Electronics, optics, and manufacturing. |
Advantages | Precision, uniformity, and versatility. |
Process Details | Conducted in a vacuum, involves heat source, and requires substrate prep. |
Discover how vapor deposition can enhance your products—contact our experts today!