Melt loss refers to the reduction in the amount of metal during the melting process due to various factors such as oxidation, evaporation, and slag formation. It is a critical consideration in metal casting and recycling industries, as it directly impacts material efficiency and cost. Understanding melt loss helps manufacturers optimize their processes, reduce waste, and improve the quality of the final product. Factors influencing melt loss include the type of metal, melting temperature, furnace conditions, and the presence of impurities.
Key Points Explained:
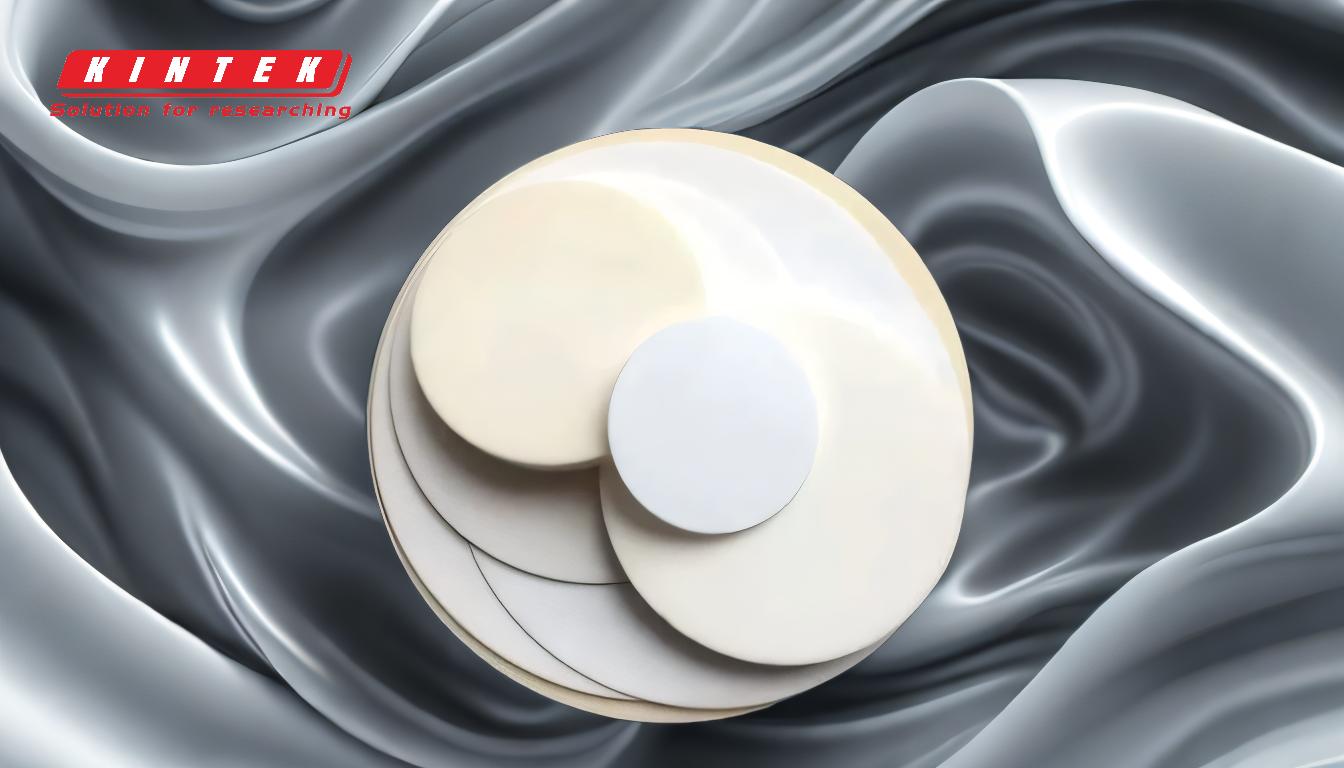
-
Definition of Melt Loss:
- Melt loss is the reduction in the mass of metal during the melting process. This occurs because some of the metal is lost through oxidation, evaporation, or incorporation into slag. For example, aluminum is particularly prone to oxidation, leading to significant melt loss if not properly managed.
-
Causes of Melt Loss:
- Oxidation: When metals are exposed to oxygen at high temperatures, they form oxides, which can either remain on the surface or become part of the slag. This is a primary cause of melt loss, especially for reactive metals like aluminum and magnesium.
- Evaporation: At very high temperatures, certain metals or alloying elements can evaporate. For instance, zinc and magnesium have relatively low boiling points and are prone to evaporation during melting.
- Slag Formation: Impurities in the metal, such as dirt, oxides, or other non-metallic inclusions, can form slag. This slag is often removed during the melting process, resulting in a loss of material.
-
Factors Influencing Melt Loss:
- Type of Metal: Different metals have varying susceptibilities to melt loss. For example, aluminum and magnesium are more prone to oxidation and evaporation compared to metals like iron or copper.
- Melting Temperature: Higher melting temperatures increase the likelihood of oxidation and evaporation, leading to greater melt loss.
- Furnace Conditions: The atmosphere inside the furnace (e.g., presence of oxygen, inert gases) and the design of the furnace can significantly impact melt loss. For instance, using a protective atmosphere or vacuum can reduce oxidation and evaporation.
- Impurities: The presence of impurities in the metal feedstock can increase slag formation, contributing to higher melt loss.
-
Impact on Industry:
- Material Efficiency: Melt loss directly affects the amount of usable metal obtained from the melting process. High melt loss means less material is available for casting or recycling, leading to increased costs.
- Cost Implications: Reducing melt loss can lead to significant cost savings, especially in industries that process large volumes of metal, such as automotive or aerospace manufacturing.
- Environmental Considerations: Minimizing melt loss also reduces waste and environmental impact, aligning with sustainability goals.
-
Strategies to Minimize Melt Loss:
- Use of Protective Atmospheres: Inert gases like argon or nitrogen can be used to create a protective atmosphere in the furnace, reducing oxidation.
- Optimized Melting Practices: Controlling the melting temperature and time can help minimize evaporation and oxidation.
- Pre-treatment of Metal: Cleaning and pre-treating the metal feedstock to remove impurities can reduce slag formation and melt loss.
- Advanced Furnace Designs: Modern furnaces with better temperature control and atmosphere management can significantly reduce melt loss.
By understanding and addressing the factors that contribute to melt loss, manufacturers can improve their processes, reduce costs, and enhance the sustainability of their operations.
Summary Table:
Aspect | Details |
---|---|
Definition | Reduction in metal mass during melting due to oxidation, evaporation, or slag. |
Causes | Oxidation, evaporation, and slag formation. |
Influencing Factors | Metal type, melting temperature, furnace conditions, and impurities. |
Industry Impact | Affects material efficiency, costs, and environmental sustainability. |
Minimization Strategies | Protective atmospheres, optimized melting practices, pre-treatment, and advanced furnace designs. |
Discover how to reduce melt loss and improve your metal processes—contact our experts today!