A microwave furnace is a specialized type of furnace that uses microwave energy to generate heat for various industrial and laboratory applications. Unlike traditional furnaces that rely on combustion or electric resistance heating, microwave furnaces utilize electromagnetic waves to directly heat materials. This method offers advantages such as rapid heating, energy efficiency, and precise temperature control. Microwave furnaces are commonly used in materials processing, ceramics, and chemical synthesis, where uniform and controlled heating is critical. They are particularly effective for applications requiring fast heating rates or processing of materials that are difficult to heat using conventional methods.
Key Points Explained:
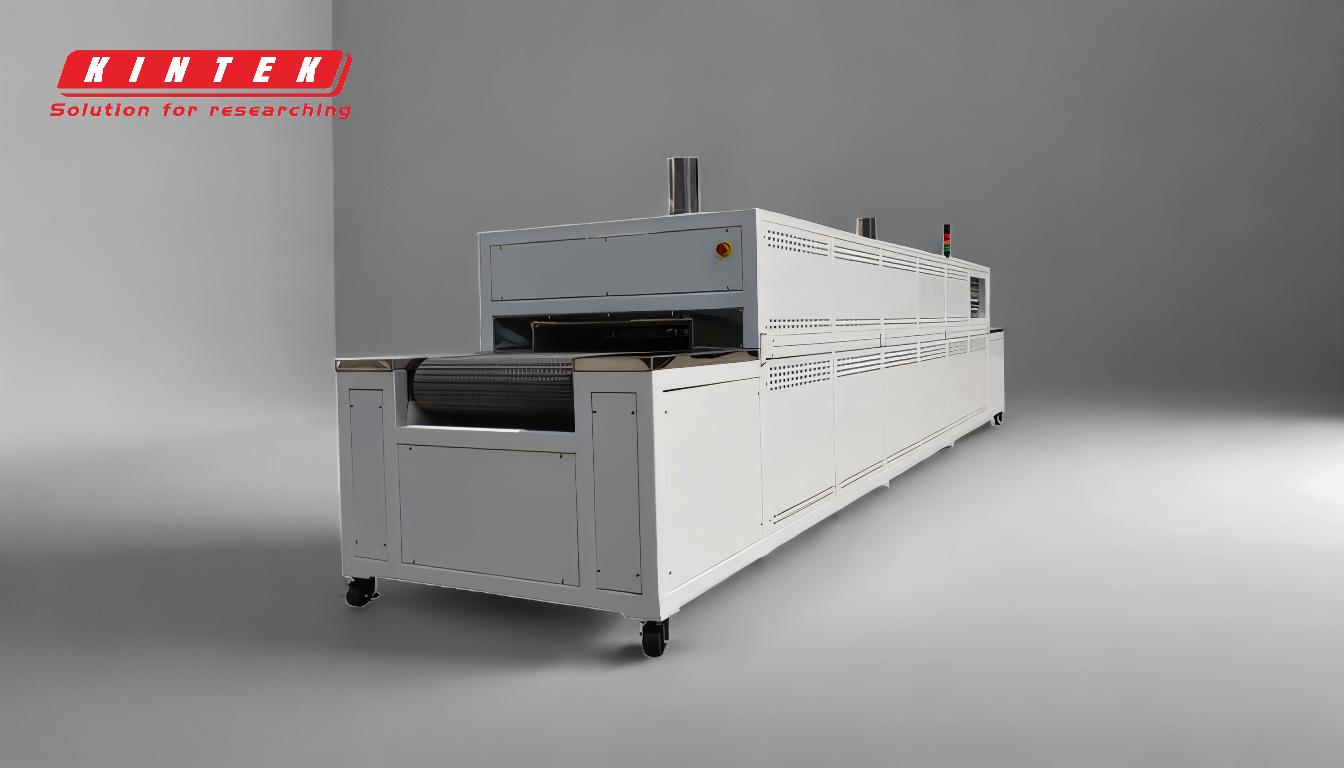
-
Definition and Function:
- A microwave furnace is a device that uses microwave energy to generate heat for processing materials. It operates by converting electromagnetic energy into thermal energy, which is absorbed by the material being processed.
- Unlike traditional furnaces, such as muffle furnaces or electric furnaces, microwave furnaces do not rely on external heating elements or combustion. Instead, they use microwaves to directly heat the material, resulting in faster and more efficient heating.
-
Heating Mechanism:
- Microwave furnaces work by emitting microwave radiation, typically at frequencies of 2.45 GHz, which is absorbed by certain materials, causing them to heat up. This process is known as dielectric heating.
- Materials that absorb microwave energy, such as water, ceramics, and certain polymers, heat up quickly and uniformly. This makes microwave furnaces ideal for applications requiring precise temperature control and rapid heating.
-
Applications:
- Microwave furnaces are widely used in materials science, ceramics, and chemical synthesis. They are particularly effective for sintering, annealing, and curing processes.
- In the ceramics industry, microwave furnaces are used to fire ceramic materials, ensuring uniform heating and reducing processing times. They are also used in the synthesis of advanced materials, such as nanoparticles and composites.
- In chemical laboratories, microwave furnaces are employed for organic and inorganic synthesis, where rapid and controlled heating is essential.
-
Advantages:
- Energy Efficiency: Microwave furnaces are highly energy-efficient because they directly heat the material, minimizing heat loss to the surroundings.
- Rapid Heating: The ability to heat materials quickly reduces processing times, making microwave furnaces ideal for high-throughput applications.
- Precise Temperature Control: Microwave furnaces offer excellent temperature control, which is crucial for processes requiring specific thermal profiles.
- Uniform Heating: The electromagnetic waves in a microwave furnace ensure uniform heating, reducing the risk of thermal gradients and material defects.
-
Comparison with Other Furnaces:
- Muffle Furnaces: Unlike muffle furnaces, which use external heating elements to heat a chamber, microwave furnaces directly heat the material, resulting in faster and more efficient processing.
- Electric Furnaces: While electric furnaces rely on resistive heating elements, microwave furnaces use electromagnetic waves, offering superior energy efficiency and heating rates.
- IGBT Furnaces: IGBT furnaces use advanced power electronics for precise control of heating processes, but microwave furnaces provide even greater control and efficiency for certain applications.
-
Limitations:
- Material Compatibility: Not all materials are suitable for microwave heating. Materials that do not absorb microwave energy, such as metals, may not be effectively processed in a microwave furnace.
- Cost: Microwave furnaces can be more expensive than traditional furnaces due to the specialized technology required.
- Size Limitations: The size of the microwave cavity limits the volume of material that can be processed at once, making them less suitable for large-scale industrial applications.
-
Future Trends:
- The development of hybrid furnaces, combining microwave heating with traditional methods, is an emerging trend. These systems aim to leverage the benefits of both technologies for improved processing efficiency and material quality.
- Advances in microwave technology, such as variable frequency microwaves, are expanding the range of materials that can be processed using microwave furnaces.
In summary, microwave furnaces are a versatile and efficient heating solution for a wide range of industrial and laboratory applications. Their ability to provide rapid, uniform, and precise heating makes them a valuable tool in materials processing, ceramics, and chemical synthesis. While they have some limitations, ongoing advancements in technology are likely to further enhance their capabilities and expand their applications.
Summary Table:
Aspect | Details |
---|---|
Definition | Uses microwave energy to generate heat for material processing. |
Heating Mechanism | Emits 2.45 GHz microwaves for dielectric heating of materials. |
Applications | Materials science, ceramics, chemical synthesis, sintering, and annealing. |
Advantages | Energy efficiency, rapid heating, precise temperature control, uniform heat. |
Limitations | Material compatibility, higher cost, size constraints. |
Future Trends | Hybrid furnaces, variable frequency microwaves for expanded applications. |
Ready to upgrade your lab or industrial heating process? Contact us today to learn more about microwave furnaces!