Microwave plasma is a versatile and powerful technology used across various industries for applications ranging from material processing to environmental cleanup. It leverages the unique properties of plasma—a highly energized state of matter—generated using microwave energy. This technology is particularly valued for its ability to achieve high temperatures and reactive environments without direct contact, making it suitable for precision tasks like surface modification, thin film deposition, and waste treatment. Its efficiency, scalability, and environmental benefits have made it a key tool in advanced manufacturing, electronics, and sustainability efforts.
Key Points Explained:
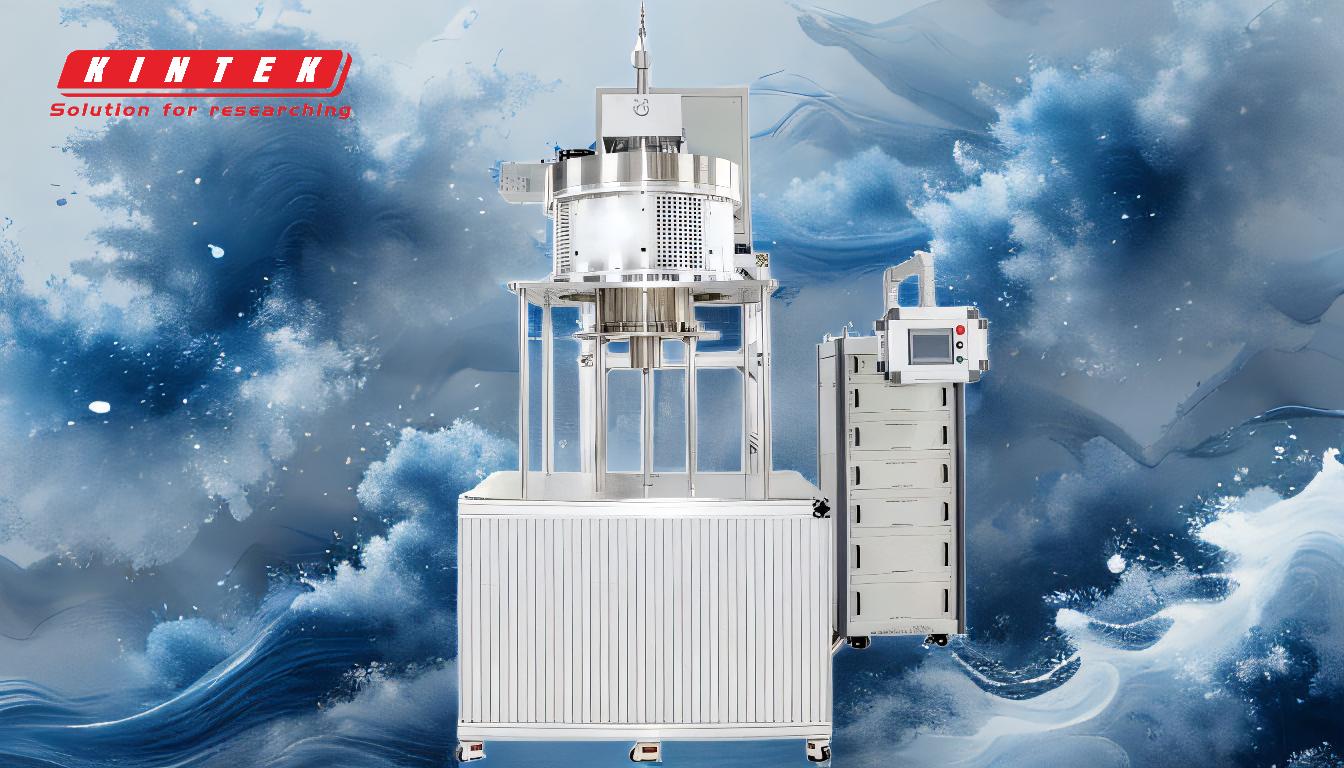
-
Definition and Generation of Microwave Plasma
- Microwave plasma is created by using microwave energy to ionize gases, producing a plasma state. This plasma consists of charged particles, free electrons, and neutral atoms, which are highly reactive and energetic.
- The process involves generating electromagnetic waves at microwave frequencies (typically 2.45 GHz) to excite gas molecules, leading to ionization. This method is efficient and can be precisely controlled, making it suitable for various industrial applications.
-
Applications in Material Processing
- Surface Modification: Microwave plasma is used to alter the surface properties of materials, such as improving adhesion, hardness, or corrosion resistance. For example, it can be applied to polymers, metals, and ceramics to enhance their performance in specific applications.
- Thin Film Deposition: This technology is widely used in the semiconductor industry to deposit thin films of materials like silicon dioxide or titanium nitride. The precision and uniformity of microwave plasma make it ideal for creating high-quality coatings.
- Nanomaterial Synthesis: Microwave plasma enables the synthesis of nanoparticles and nanostructures with controlled size and morphology, which are essential for advanced materials in electronics, catalysis, and energy storage.
-
Environmental and Waste Treatment Applications
- Pollution Control: Microwave plasma can break down harmful pollutants, such as volatile organic compounds (VOCs) and greenhouse gases, into less harmful substances. This is achieved through the high-energy reactions in the plasma, which decompose complex molecules.
- Waste-to-Energy Conversion: The technology is used to convert organic waste into syngas (a mixture of hydrogen and carbon monoxide), which can be used as a fuel or chemical feedstock. This process is highly efficient and environmentally friendly.
- Water Purification: Microwave plasma can disinfect water by destroying pathogens and breaking down organic contaminants, making it a promising solution for clean water production.
-
Advantages of Microwave Plasma Technology
- High Efficiency: Microwave plasma systems are energy-efficient and can achieve high temperatures quickly, reducing processing times and costs.
- Scalability: The technology can be scaled for both small-scale laboratory applications and large-scale industrial processes.
- Environmental Benefits: By enabling cleaner production processes and reducing waste, microwave plasma contributes to sustainability goals.
-
Challenges and Future Directions
- Cost and Complexity: While microwave plasma offers many benefits, the initial setup and operational costs can be high, especially for advanced applications.
- Research and Development: Ongoing research aims to optimize the technology for new applications, such as biomedical devices and renewable energy systems.
- Integration with Other Technologies: Combining microwave plasma with other advanced manufacturing techniques could unlock new possibilities in fields like additive manufacturing and smart materials.
In summary, microwave plasma is a transformative technology with wide-ranging applications in material processing, environmental cleanup, and beyond. Its ability to deliver precise, high-energy reactions makes it a valuable tool for industries seeking innovative and sustainable solutions. As research continues to advance, the potential for microwave plasma to address global challenges in energy, manufacturing, and environmental protection will only grow.
Summary Table:
Application | Key Uses |
---|---|
Material Processing | Surface modification, thin film deposition, nanomaterial synthesis |
Environmental Cleanup | Pollution control, waste-to-energy conversion, water purification |
Advantages | High efficiency, scalability, environmental benefits |
Challenges | High cost, complexity, ongoing R&D for new applications |
Learn how microwave plasma can revolutionize your processes—contact our experts today!