Nitriding is a heat treatment process that introduces nitrogen into the surface of specific ferrous alloys to enhance their hardness, wear resistance, and corrosion resistance. Unlike other heat treatment methods, nitriding does not require quenching, making it a unique and efficient process. The treatment is performed at relatively low temperatures (975–1,050°F or 500–580°C) over an extended period (24–72 hours), during which nitrogen is absorbed into the metal surface and diffuses inward to form a hard, wear-resistant nitride layer. This process is commonly used in industries requiring durable and long-lasting components, such as automotive, aerospace, and tool manufacturing.
Key Points Explained:
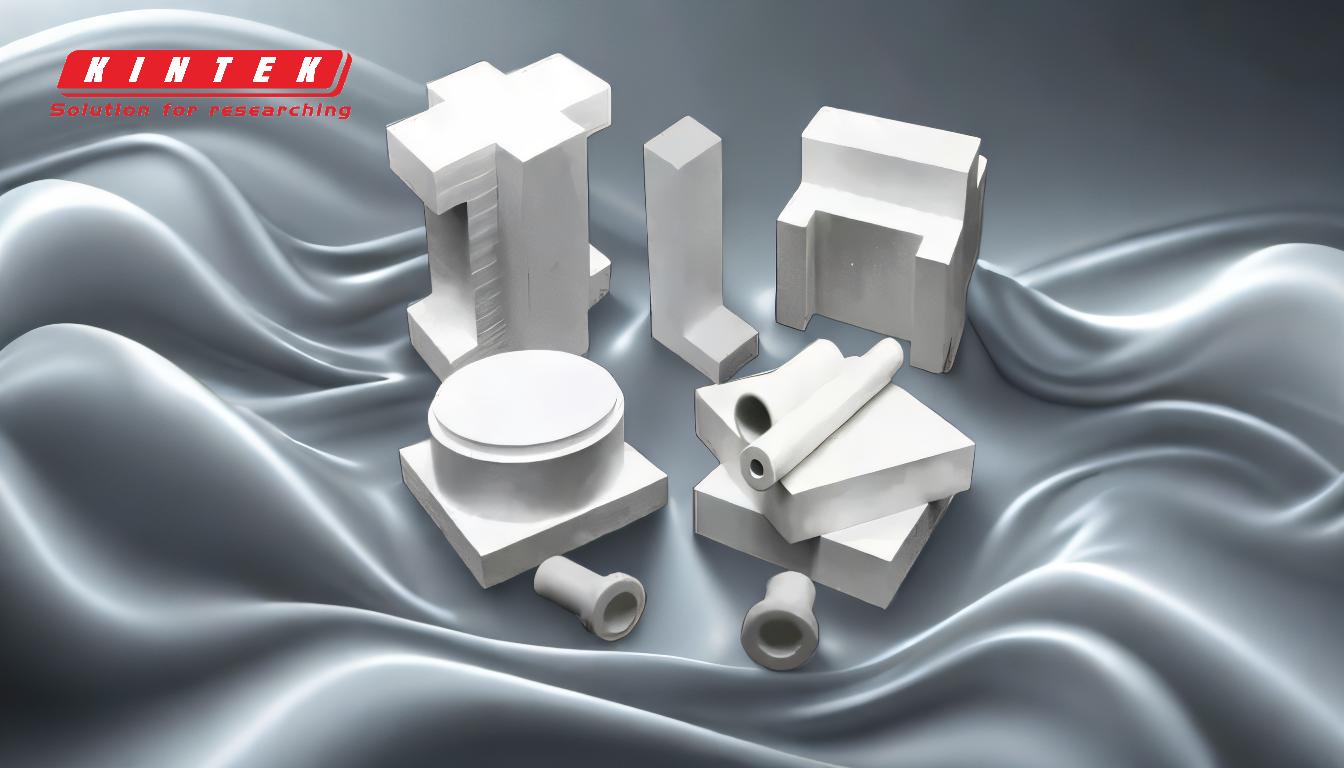
-
Definition of Nitriding:
- Nitriding is a surface hardening process that introduces nitrogen into the surface of ferrous alloys.
- It is performed at relatively low temperatures (975–1,050°F or 500–580°C) over a prolonged period (24–72 hours).
- The process does not require quenching, which distinguishes it from other heat treatment methods.
-
Mechanism of Nitriding:
- The process involves heating the metal in the presence of a nitrogen source, typically ammonia gas.
- At temperatures above 400°C, ammonia decomposes into hydrogen and reactive nitrogen atoms.
- These nitrogen atoms are absorbed by the steel surface and diffuse inward, forming a hard nitride layer.
-
Benefits of Nitriding:
- Increased Hardness: The nitride layer significantly enhances the surface hardness of the metal, making it more resistant to wear and abrasion.
- Improved Wear Resistance: The hard surface layer reduces wear and extends the lifespan of the component.
- Enhanced Corrosion Resistance: The nitride layer also improves the metal's resistance to corrosion, making it suitable for harsh environments.
- No Quenching Required: Unlike other heat treatment processes, nitriding does not require rapid cooling (quenching), reducing the risk of distortion or cracking.
-
Applications of Nitriding:
- Automotive Industry: Used for components like crankshafts, camshafts, and gears to improve durability and performance.
- Aerospace Industry: Applied to parts that require high strength and resistance to wear and corrosion.
- Tool Manufacturing: Enhances the lifespan and performance of cutting tools, dies, and molds.
- General Engineering: Used in various industrial applications where surface hardness and wear resistance are critical.
-
Types of Nitriding:
- Gas Nitriding: The most common method, where the workpiece is heated in a sealed chamber with ammonia gas. The gas decomposes at high temperatures, releasing nitrogen atoms that diffuse into the metal surface.
- Plasma Nitriding: A more advanced method that uses plasma to ionize nitrogen gas, allowing for more precise control over the nitriding process and resulting in a more uniform nitride layer.
- Salt Bath Nitriding: Involves immersing the metal in a molten salt bath containing nitrogen compounds. This method is less common but can be effective for certain applications.
-
Considerations for Nitriding:
- Material Selection: Not all ferrous alloys are suitable for nitriding. Alloys containing elements like aluminum, chromium, and molybdenum are particularly well-suited for the process.
- Temperature Control: Precise temperature control is crucial to ensure the formation of a high-quality nitride layer without compromising the metal's core properties.
- Time Duration: The process requires a significant amount of time (24–72 hours) to achieve the desired depth of the nitride layer.
- Post-Treatment: In some cases, post-nitriding treatments such as polishing or coating may be required to achieve the desired surface finish or additional properties.
In summary, nitriding is a versatile and effective heat treatment process that enhances the surface properties of ferrous alloys. Its ability to improve hardness, wear resistance, and corrosion resistance without the need for quenching makes it a valuable technique in various industrial applications.
Summary Table:
Aspect | Details |
---|---|
Process | Introduces nitrogen into ferrous alloys at 975–1,050°F (500–580°C). |
Key Benefits | Increased hardness, wear resistance, corrosion resistance, no quenching. |
Applications | Automotive, aerospace, tool manufacturing, general engineering. |
Types of Nitriding | Gas nitriding, plasma nitriding, salt bath nitriding. |
Considerations | Material selection, temperature control, time duration, post-treatment. |
Discover how nitriding can improve your components' performance—contact us today for expert advice!