Nitrogen atmosphere heat treatment is a modern and environmentally friendly method used in various industrial processes to improve the properties of metals and alloys. This technique involves heating materials in a nitrogen-rich environment, which can be pure nitrogen or a blend with other gases like hydrogen. The nitrogen atmosphere serves multiple purposes, including protecting the material from oxidation, acting as a carrier gas for carbon-controlled atmospheres, and enhancing the overall efficiency and safety of the heat treatment process. This method is versatile and can be applied to a wide range of heat treatment processes, such as quenching, annealing, carburizing, and more, offering results comparable to traditional methods while being more energy-efficient and less polluting.
Key Points Explained:
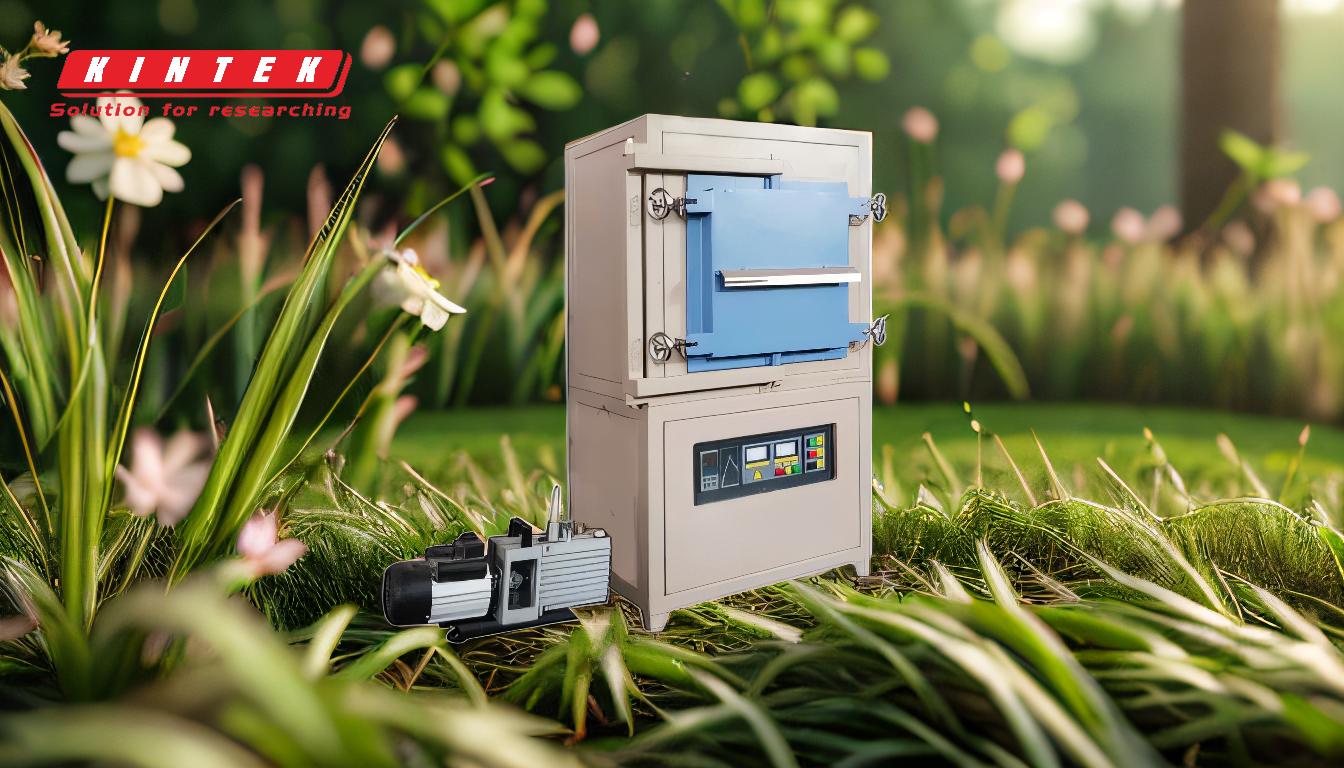
-
Purpose of Nitrogen Atmosphere in Heat Treatment:
- The primary role of a nitrogen atmosphere in heat treatment is to provide a protective environment that prevents oxidation and other undesirable chemical reactions. This is crucial for maintaining the integrity and desired properties of the material being treated.
- Nitrogen can also act as a carrier gas in carbon-controlled atmospheres, facilitating processes like carburizing and carbonitriding, where carbon is introduced into the surface of the metal to enhance hardness and wear resistance.
-
Composition and Delivery of Nitrogen Atmosphere:
- Nitrogen used in heat treatment is typically not pure but is often mixed with small amounts of hydrogen. A common blend is 90% nitrogen and 10% hydrogen, which helps in reducing the risk of oxidation and improves the overall effectiveness of the heat treatment process.
- The dew point of the nitrogen atmosphere is critical and is usually maintained between -75°F and -110°F to ensure the dryness and purity of the gas, which is essential for achieving consistent and high-quality results.
-
Advantages of Nitrogen Atmosphere Heat Treatment:
- Energy Efficiency: Using nitrogen can lead to significant energy savings compared to traditional heat treatment methods. The process is more controlled and requires less energy to maintain the desired atmosphere.
- Environmental Benefits: Nitrogen atmosphere heat treatment reduces the release of harmful gases and pollutants, making it a more environmentally friendly option.
- Safety: The use of nitrogen, especially when blended with hydrogen in controlled amounts, enhances the safety of the heat treatment process by reducing the risk of explosions and other hazards associated with more reactive gases.
-
Applications of Nitrogen Atmosphere Heat Treatment:
- This method is highly versatile and can be applied to a wide range of heat treatment processes, including:
- Quenching: Rapid cooling of metals to achieve desired hardness and strength.
- Annealing: Heating and then slowly cooling metals to relieve internal stresses and improve ductility.
- Carburizing: Introducing carbon into the surface of low-carbon steels to increase hardness.
- Carbonitriding: Similar to carburizing but also introduces nitrogen to enhance surface properties.
- Soft Nitriding: A process that introduces nitrogen into the surface of metals to improve wear resistance and fatigue strength.
- Carbon Re-carbonation: Restoring carbon content in the surface of metals that have been decarburized.
- This method is highly versatile and can be applied to a wide range of heat treatment processes, including:
-
Comparison with Traditional Methods:
- Nitrogen atmosphere heat treatment offers results that are comparable to traditional endothermic atmosphere treatments but with added benefits such as energy savings, enhanced safety, and reduced environmental impact.
- The process is more controlled and can be tailored to specific material requirements, leading to more consistent and high-quality outcomes.
In summary, nitrogen atmosphere heat treatment is a sophisticated and efficient method that leverages the protective and reactive properties of nitrogen to enhance the heat treatment process. Its applications are vast, and it offers significant advantages over traditional methods, making it a preferred choice in modern industrial applications.
Summary Table:
Aspect | Details |
---|---|
Purpose | Prevents oxidation, acts as a carrier gas, enhances safety and efficiency. |
Composition | Typically 90% nitrogen + 10% hydrogen; dew point maintained at -75°F to -110°F. |
Advantages | Energy-efficient, environmentally friendly, and safer than traditional methods. |
Applications | Quenching, annealing, carburizing, carbonitriding, soft nitriding, and more. |
Comparison | Comparable to traditional methods but with added energy savings and safety. |
Interested in optimizing your heat treatment process? Contact us today to learn more about nitrogen atmosphere solutions!