Physical Vapor Deposition (PVD) is a vacuum-based process used to deposit thin films of material onto a substrate. It involves the transformation of a solid material into a vapor phase, which then condenses onto the substrate to form a thin film. The process is widely used in industries such as electronics, optics, and tool manufacturing due to its ability to produce high-quality, durable coatings. PVD is distinct from Chemical Vapor Deposition (CVD) in that it relies on physical processes rather than chemical reactions to deposit materials. The PVD process typically involves four key steps: vaporization of the target material, transportation of the vapor, reaction with a gaseous species (if applicable), and condensation onto the substrate.
Key Points Explained:
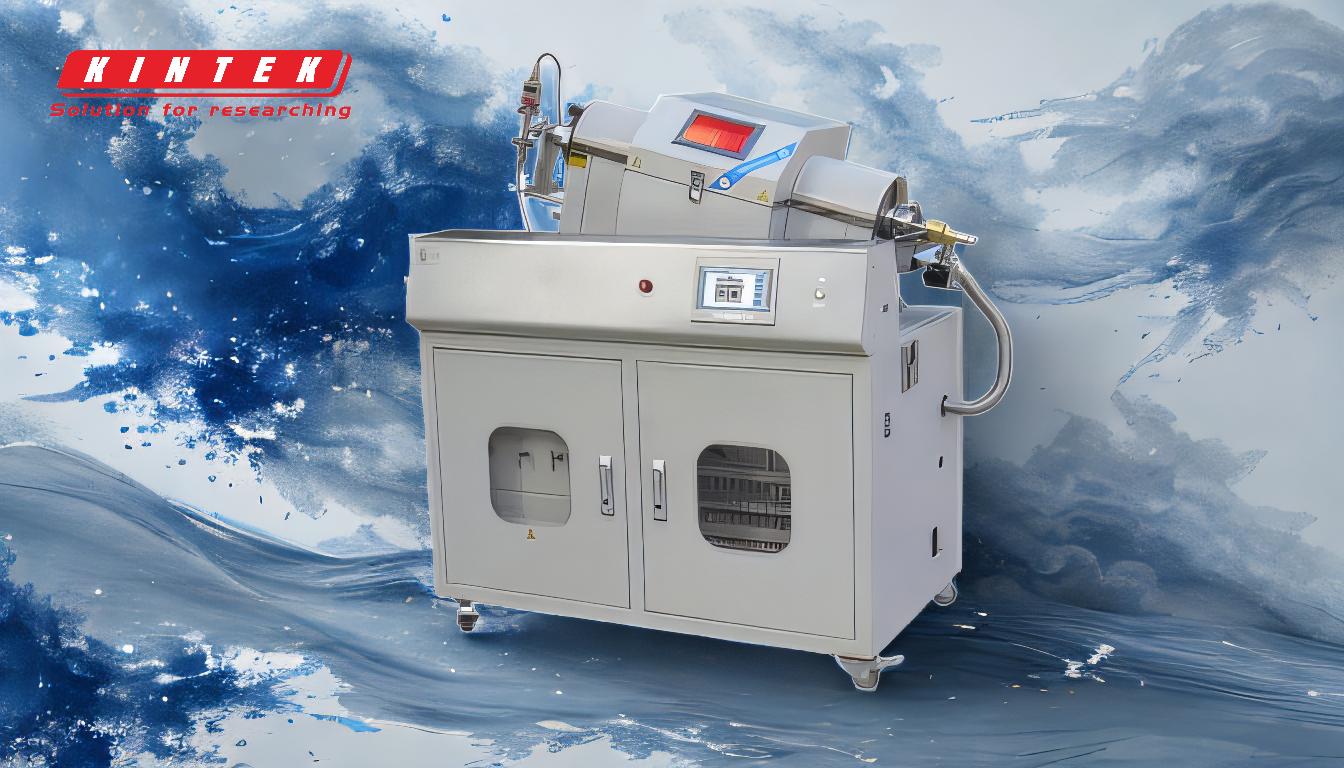
-
Vaporization of the Target Material:
- The first step in the PVD process is the vaporization of the target material. This is typically achieved through physical means such as sputtering, evaporation, or laser ablation. In sputtering, high-energy ions bombard the target material, knocking atoms off its surface and into the vapor phase. In evaporation, the target material is heated until it evaporates. Laser ablation uses a high-energy laser to vaporize the material. The choice of vaporization method depends on the material properties and the desired film characteristics.
-
Transportation of the Vapor:
- Once the target material is vaporized, the vapor must be transported to the substrate. This occurs in a vacuum environment to ensure that the vapor can travel without interference from air molecules. The vacuum also helps to maintain the purity of the deposited film by minimizing contamination. The vaporized atoms or molecules travel in a straight line from the target to the substrate, where they will eventually condense.
-
Reaction with a Gaseous Species (Optional):
- In some PVD processes, a reactive gas is introduced into the vacuum chamber. This gas can react with the vaporized material to form a compound. For example, if the target material is titanium and the reactive gas is nitrogen, the resulting compound would be titanium nitride (TiN), which is known for its hardness and wear resistance. This step is optional and depends on the desired properties of the final coating.
-
Condensation onto the Substrate:
- The final step in the PVD process is the condensation of the vaporized material (or the reaction product) onto the substrate. The substrate is typically positioned in such a way that it intercepts the vapor stream. As the vaporized atoms or molecules strike the substrate, they lose energy and condense, forming a thin film. The film grows layer by layer, and the process can be controlled to achieve specific thicknesses and properties. The resulting film is typically dense, uniform, and well-adhered to the substrate.
-
Advantages of PVD:
- PVD offers several advantages over other deposition techniques. It produces films with high purity and excellent adhesion. The process can be used to deposit a wide range of materials, including metals, ceramics, and composites. PVD coatings are also known for their durability, resistance to wear and corrosion, and ability to enhance the performance of tools and components. Additionally, PVD is an environmentally friendly process, as it does not involve the use of hazardous chemicals.
-
Applications of PVD:
- PVD is used in a variety of applications across different industries. In the electronics industry, it is used to deposit thin films for semiconductors, solar cells, and optical coatings. In the tool manufacturing industry, PVD coatings are applied to cutting tools, molds, and dies to improve their wear resistance and lifespan. PVD is also used in the production of decorative coatings for jewelry, watches, and automotive components.
-
Comparison with Chemical Vapor Deposition (CVD):
- While both PVD and CVD are used to deposit thin films, they differ in their mechanisms. PVD relies on physical processes to vaporize and deposit materials, whereas CVD involves chemical reactions to form the film. PVD is typically performed at lower temperatures than CVD, making it suitable for temperature-sensitive substrates. However, CVD can produce films with better step coverage and conformality, making it more suitable for complex geometries.
In summary, Physical Vapor Deposition is a versatile and widely used technique for depositing thin films with excellent properties. Its ability to produce high-quality, durable coatings makes it a valuable process in various industries. By understanding the key steps and advantages of PVD, manufacturers can make informed decisions about its use in their applications.
Summary Table:
Key Aspect | Description |
---|---|
Process | Vacuum-based deposition of thin films onto a substrate. |
Steps | 1. Vaporization of target material 2. Transportation of vapor 3. Optional reaction with gas 4. Condensation onto substrate |
Advantages | High purity, excellent adhesion, durability, and eco-friendliness. |
Applications | Electronics, optics, tool manufacturing, and decorative coatings. |
Comparison with CVD | PVD uses physical processes; CVD involves chemical reactions. |
Discover how PVD can enhance your products—contact us today for expert advice!