Physical Vapor Deposition (PVD) is a sophisticated thin-film coating process that involves vaporizing a solid material in a vacuum environment and depositing it onto a substrate to form a thin, durable, and high-performance layer. This process is widely used in industries such as electronics, optics, automotive, and aerospace due to its ability to produce coatings with excellent adhesion, corrosion resistance, and thermal stability. PVD techniques include sputtering and thermal evaporation, which are carried out in vacuum chambers to ensure minimal contamination and precise control over film properties. The process is ideal for creating coatings on materials with high melting points and can produce films with nanoscale precision.
Key Points Explained:
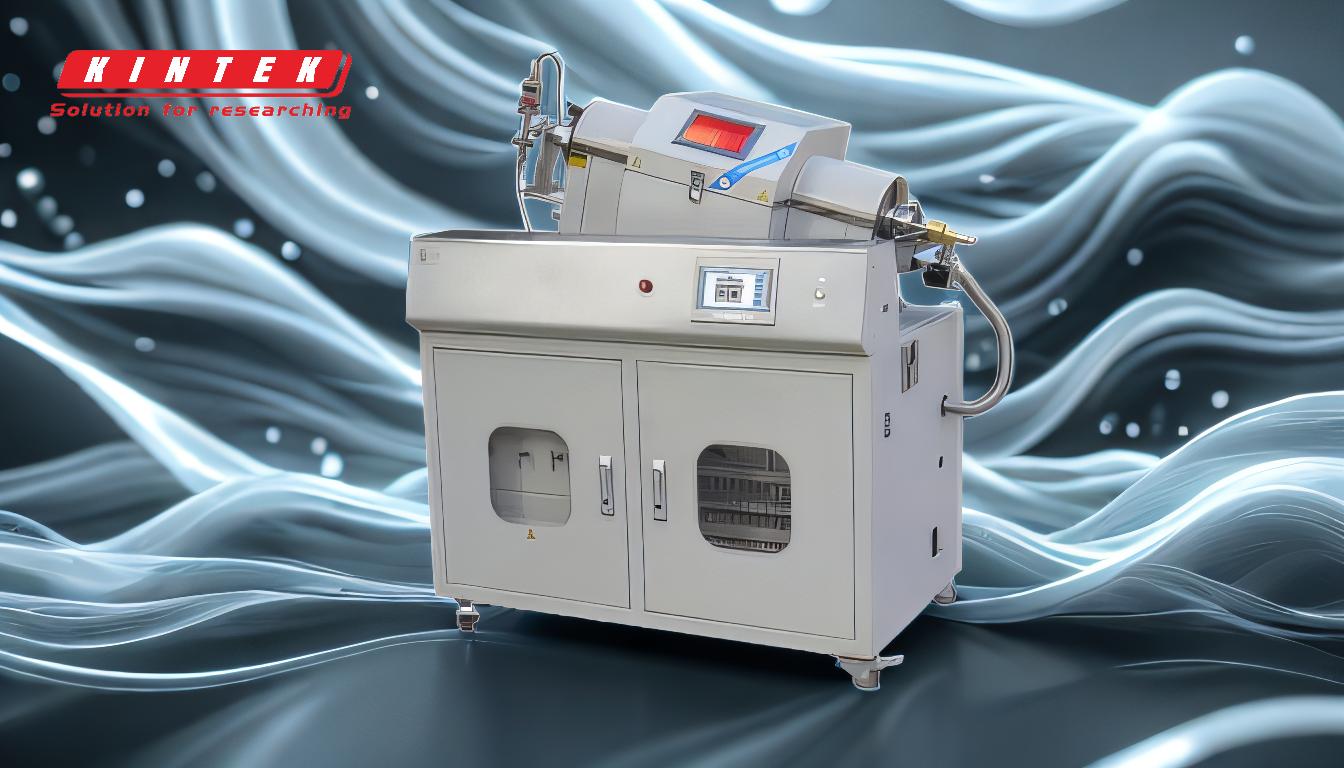
-
Definition and Purpose of PVD:
- PVD is a physical process used to deposit thin films of material onto a substrate. It is primarily employed to create coatings that enhance the durability, corrosion resistance, and thermal stability of surfaces.
- The process is widely used in industries such as electronics, optics, automotive, and aerospace due to its ability to produce high-quality, uniform coatings.
-
Core Mechanism of PVD:
- The process begins with a solid precursor material, which is vaporized using high-energy methods such as electrical discharge, laser ablation, or thermal evaporation.
- The vaporized material is then transported through a vacuum or low-pressure chamber to the substrate, where it condenses and forms a thin film.
-
Types of PVD Techniques:
- Sputtering: A method where the target material is bombarded with high-energy ions, causing atoms to be ejected and deposited onto the substrate. This technique is highly versatile and can be used with a wide range of materials.
- Thermal Evaporation: Involves heating the target material until it evaporates, and the vapor condenses onto the substrate. This method is suitable for materials with lower melting points.
- Other sub-methods include arc vapor deposition and pulsed laser deposition, each with specific applications and advantages.
-
Vacuum Environment:
- PVD processes are conducted in vacuum chambers to minimize contamination from background gases and ensure precise control over the deposition process.
- The vacuum environment also allows for better control of film thickness and uniformity.
-
Advantages of PVD:
- High-Quality Coatings: PVD produces thin films with excellent adhesion, uniformity, and durability.
- Material Versatility: It can handle materials with high melting points, such as metals, ceramics, and alloys.
- Environmental Friendliness: PVD is a clean process that produces minimal waste and does not involve harmful chemicals.
-
Applications of PVD:
- Electronics: Used to deposit conductive and insulating layers in semiconductor devices.
- Optics: Applied to create anti-reflective and protective coatings on lenses and mirrors.
- Automotive and Aerospace: Enhances the wear resistance and corrosion protection of engine components and tools.
- Medical Devices: Provides biocompatible coatings for implants and surgical instruments.
-
Control and Monitoring:
- Advanced PVD systems use quartz crystal rate monitors to precisely control the deposition rate and film thickness.
- The vacuum chamber is pumped down to ultra-low pressures to reduce the presence of background gases that could interfere with the deposition process.
-
Challenges and Considerations:
- Complexity: PVD systems require sophisticated equipment and precise control, making the process more expensive than some alternative coating methods.
- Material Limitations: While PVD can handle a wide range of materials, some may require specialized techniques or pre-treatment.
By understanding these key points, a purchaser of equipment or consumables for PVD processes can make informed decisions about the technology's suitability for their specific applications and requirements.
Summary Table:
Aspect | Details |
---|---|
Definition | A process to deposit thin films onto substrates in a vacuum environment. |
Key Techniques | Sputtering, thermal evaporation, arc vapor deposition, pulsed laser deposition. |
Advantages | High-quality coatings, material versatility, environmental friendliness. |
Applications | Electronics, optics, automotive, aerospace, medical devices. |
Challenges | Requires sophisticated equipment; some materials need specialized techniques. |
Ready to enhance your projects with PVD technology? Contact us today to learn more!