Physical Vapor Deposition (PVD) by evaporation and sputtering is a widely used thin-film deposition technique in materials science and engineering. It involves the transformation of a solid material into a vapor phase, which is then transported and deposited onto a substrate to form a thin, uniform, and adherent film. PVD is divided into two primary methods: evaporation and sputtering. In evaporation, the material is heated until it vaporizes, while in sputtering, high-energy ions bombard the target material to dislodge atoms, creating a vapor. Both methods are used to produce high-purity, durable coatings for applications in electronics, optics, and protective coatings.
Key Points Explained:
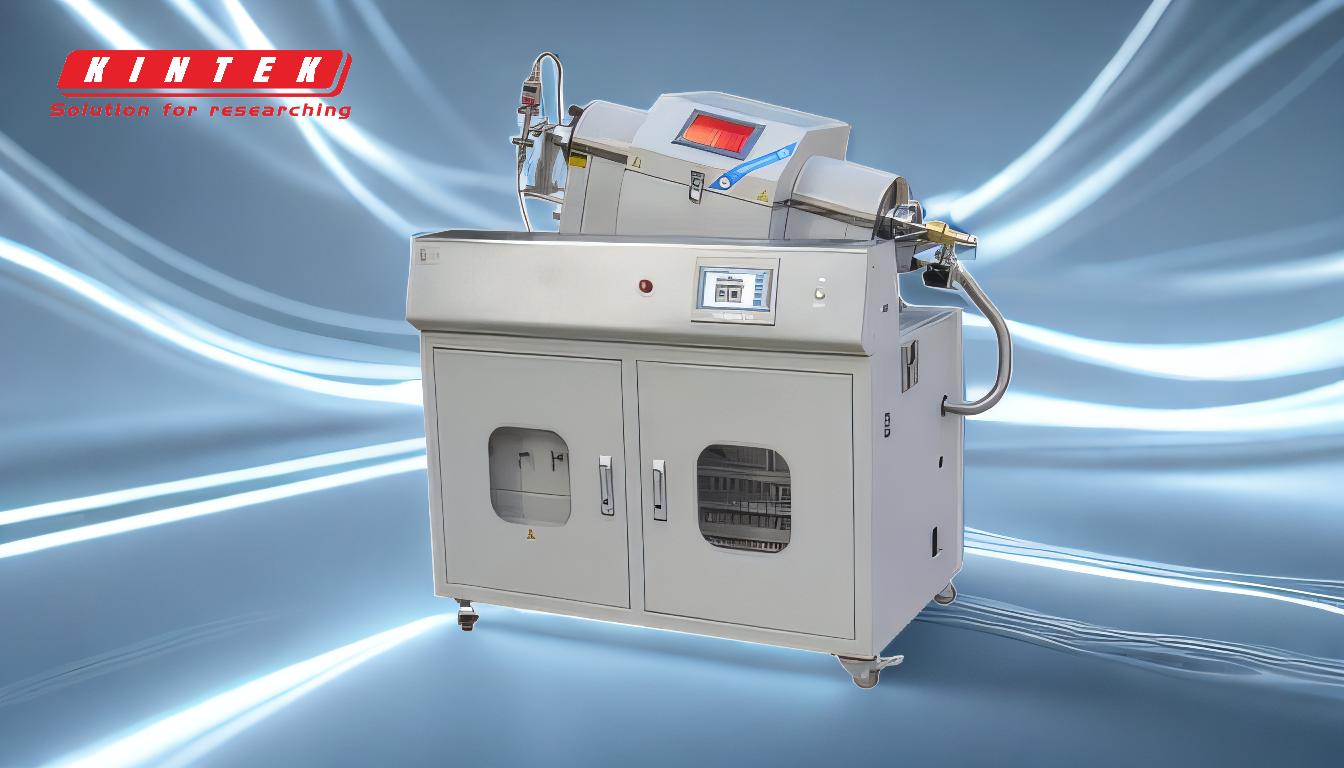
-
Physical Vapor Deposition (PVD) Overview:
- PVD is a vacuum-based process used to deposit thin films of materials onto substrates.
- It is a physical process, meaning it does not involve chemical reactions to form the vapor phase.
- PVD is widely used in industries such as semiconductors, optics, and tool coatings due to its ability to produce high-quality, durable films.
-
PVD by Evaporation:
- Process: In evaporation, the material to be deposited is heated in a vacuum chamber until it reaches its vaporization temperature. This can be achieved using resistive heating, electron beams, or lasers.
- Transportation: The vaporized atoms travel through the vacuum and condense on the cooler substrate surface.
- Applications: Evaporation is commonly used for depositing metals, alloys, and some compounds in applications like optical coatings and thin-film electronics.
-
PVD by Sputtering:
- Process: Sputtering involves bombarding a target material (the source of the coating) with high-energy ions (usually argon) in a vacuum. The impact dislodges atoms from the target, which then form a vapor.
- Transportation: The sputtered atoms travel through the vacuum and deposit onto the substrate.
- Reaction: In reactive sputtering, a reactive gas (e.g., oxygen or nitrogen) is introduced, allowing the sputtered atoms to form compounds like oxides, nitrides, or carbides on the substrate.
- Applications: Sputtering is widely used for depositing complex materials, including dielectrics, semiconductors, and magnetic films.
-
Key Steps in PVD:
- Evaporation or Sputtering: The material is converted into a vapor phase either by heating (evaporation) or ion bombardment (sputtering).
- Transportation: The vaporized atoms or molecules travel through the vacuum chamber to the substrate.
- Reaction (Optional): In reactive PVD, the vapor reacts with a gas to form a compound coating.
- Deposition: The vapor condenses on the substrate, forming a thin film.
-
Advantages of PVD:
- High Purity: PVD produces extremely pure films due to the vacuum environment, which minimizes contamination.
- Uniformity: The process allows for precise control over film thickness and uniformity.
- Adhesion: PVD coatings exhibit excellent adhesion to the substrate, making them durable and long-lasting.
- Versatility: PVD can deposit a wide range of materials, including metals, ceramics, and composites.
-
Comparison with Chemical Vapor Deposition (CVD):
- Process Difference: Unlike PVD, CVD involves chemical reactions to form the vapor phase, which then deposits onto the substrate.
- Temperature: CVD typically requires higher temperatures than PVD, limiting its use with temperature-sensitive substrates.
- Applications: CVD is often used for depositing complex compounds and conformal coatings, while PVD is preferred for high-purity, thin films.
-
Industrial Applications:
- Electronics: PVD is used to deposit conductive and insulating layers in semiconductor devices.
- Optics: It is employed to create reflective and anti-reflective coatings for lenses and mirrors.
- Tool Coatings: PVD coatings enhance the hardness and wear resistance of cutting tools and molds.
By understanding the principles and steps involved in PVD by evaporation and sputtering, manufacturers and researchers can select the appropriate method for their specific application, ensuring high-quality, durable coatings.
Summary Table:
Aspect | Evaporation | Sputtering |
---|---|---|
Process | Material is heated to vaporize in a vacuum. | High-energy ions bombard the target to dislodge atoms, creating a vapor. |
Transportation | Vaporized atoms travel through vacuum to condense on the substrate. | Sputtered atoms travel through vacuum to deposit on the substrate. |
Reaction | Typically no chemical reaction involved. | Reactive sputtering uses gases to form compounds like oxides or nitrides. |
Applications | Metals, alloys, and optical coatings. | Dielectrics, semiconductors, and magnetic films. |
Advantages | High purity, uniform thickness, excellent adhesion, and versatility. | High purity, uniform thickness, excellent adhesion, and versatility. |
Discover how PVD can enhance your applications—contact our experts today for tailored solutions!