PVD-coated stainless steel is a material that combines the inherent strength and durability of stainless steel with the enhanced properties provided by a Physical Vapor Deposition (PVD) coating. This coating process involves vaporizing a solid material in a vacuum chamber and depositing it onto the stainless steel surface, resulting in a thin, durable layer that improves hardness, wear resistance, and corrosion resistance. Additionally, PVD coatings offer aesthetic benefits, providing a wide range of colors and finishes while maintaining environmental friendliness and low maintenance requirements. This makes PVD-coated stainless steel ideal for applications in harsh environments or decorative purposes where both durability and appearance are critical.
Key Points Explained:
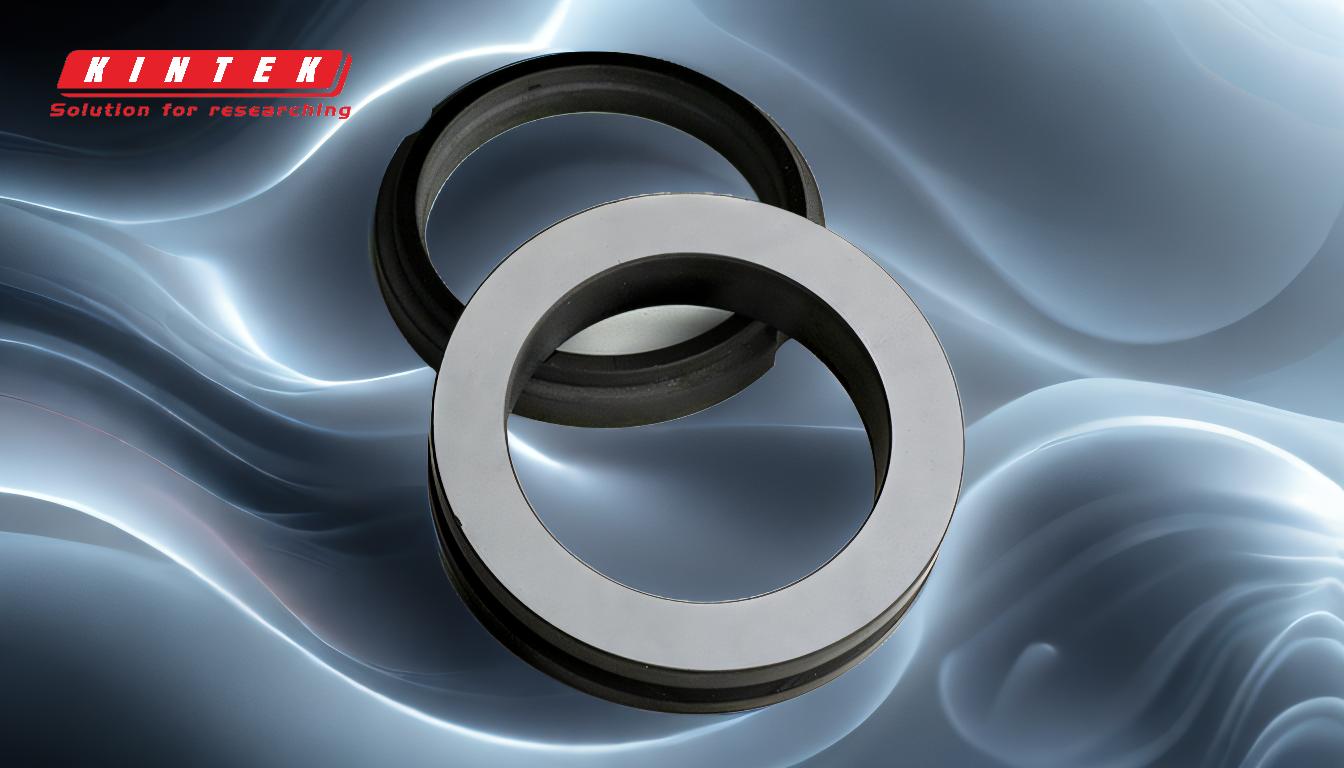
-
What is PVD-Coated Stainless Steel?
- PVD-coated stainless steel is stainless steel enhanced with a thin film coating applied through the Physical Vapor Deposition process. This coating improves the material's performance and aesthetic appeal.
-
The PVD Coating Process:
- PVD is a vacuum-based process where a solid material is vaporized and deposited onto the stainless steel surface. The process occurs at temperatures between 50 and 600 degrees Celsius.
- It is a "line of sight" technique, meaning the vaporized atoms travel through the vacuum and embed themselves into the target material. Proper positioning or rotation of the object ensures uniform coating.
-
Properties and Benefits of PVD Coatings:
- Enhanced Durability: PVD coatings are four times harder than chrome, making them highly resistant to scratches, abrasions, and corrosion.
- Wear Resistance: The coatings can withstand years of use in decorative applications with mild to moderate wear. For harsher conditions, thicker coatings (>1μm) are recommended.
- Aesthetic Value: PVD coatings offer a wide range of colors and finishes, enhancing the visual appeal of stainless steel.
- Environmental Friendliness: The process is eco-friendly, producing minimal waste and harmful byproducts.
- Compatibility: PVD coatings are compatible with various materials, including stainless steel, and provide a uniform, low-maintenance finish.
-
Applications of PVD-Coated Stainless Steel:
- Decorative Uses: Commonly used in architecture, interior design, and consumer products where aesthetics and durability are important.
- Industrial Applications: Ideal for components exposed to harsh environments, such as marine or coastal areas, due to its superior corrosion and wear resistance.
- High-Temperature Environments: PVD coatings can tolerate high temperatures, making them suitable for industrial machinery and tools.
-
Comparison to Other Coating Methods:
- PVD coatings outperform traditional methods like electroplating or powder coating in terms of durability, wear resistance, and corrosion resistance. They also provide a more consistent and uniform finish.
-
Maintenance and Longevity:
- PVD-coated stainless steel requires minimal maintenance due to its scratch and corrosion resistance. Its longevity makes it a cost-effective choice for long-term projects.
By combining the strength of stainless steel with the advanced properties of PVD coatings, this material offers a versatile solution for both functional and decorative applications, ensuring durability, aesthetic appeal, and environmental sustainability.
Summary Table:
Aspect | Details |
---|---|
Coating Process | Physical Vapor Deposition (PVD) in a vacuum chamber at 50–600°C. |
Key Benefits | Enhanced durability, wear resistance, corrosion resistance, and aesthetics. |
Applications | Decorative uses, industrial components, high-temperature environments. |
Environmental Impact | Eco-friendly process with minimal waste and harmful byproducts. |
Maintenance | Low maintenance, scratch-resistant, and long-lasting. |
Learn how PVD-coated stainless steel can elevate your project—contact us today for expert advice!