PVD electroplating, or Physical Vapour Deposition electroplating, is a modern and environmentally friendly process used to deposit thin layers of material onto a surface. Unlike traditional electroplating, which uses an electrochemical process to coat metals, PVD involves vaporizing a solid material in a vacuum chamber and then condensing it onto the target surface. This results in a highly durable, pure, and thin coating that offers excellent mechanical, chemical, and optical properties. PVD electroplating is widely used in industries such as aerospace, medical, and high-tech due to its ability to provide superior hardness, wear resistance, corrosion resistance, and aesthetic appeal.
Key Points Explained:
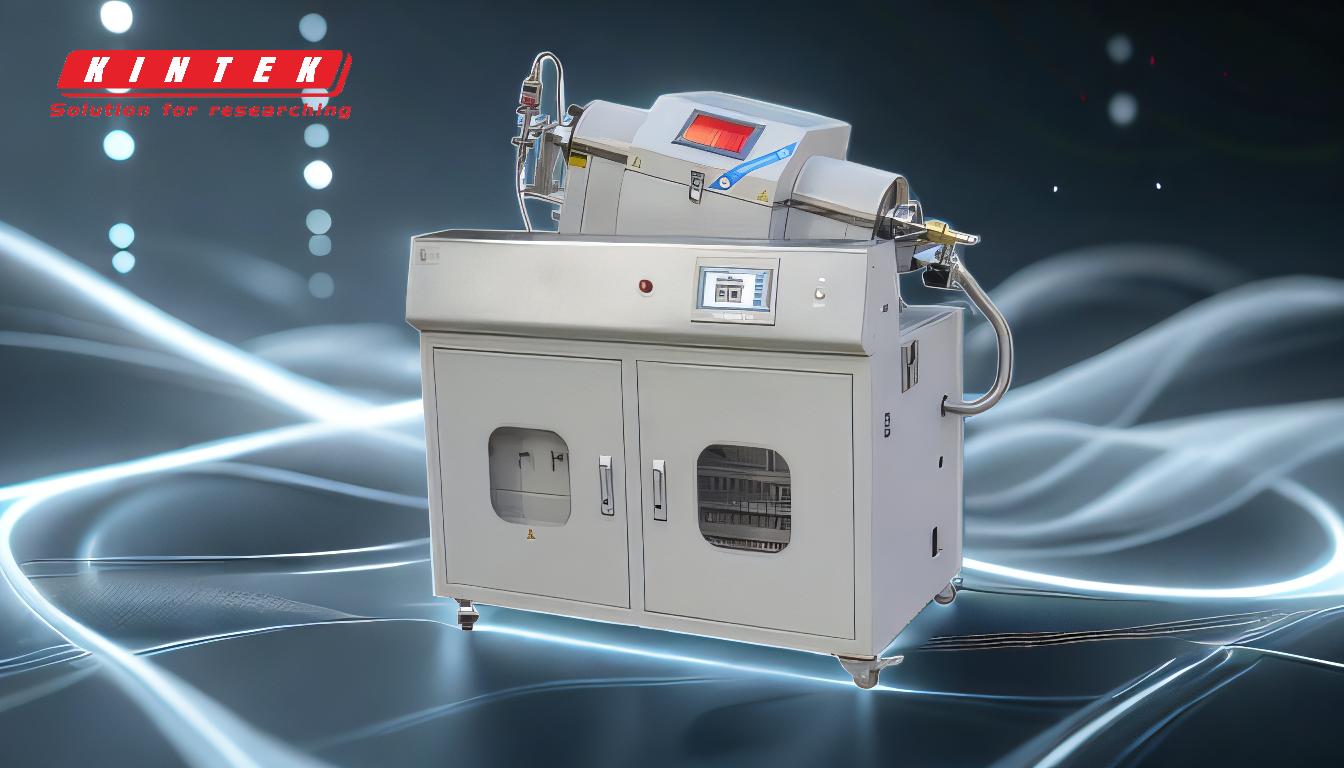
-
Definition and Process of PVD Electroplating:
- PVD electroplating is a technique that deposits thin layers of material onto a surface using vaporization and condensation.
- The process involves placing the item in a vacuum chamber and bombarding it with ions or atoms of the coating material, which then bond to the surface to form a robust and resilient layer.
- Unlike traditional electroplating, which uses an electrochemical process, PVD relies on physical vaporization and condensation, resulting in a more precise and controlled deposition.
-
Steps Involved in PVD Electroplating:
- Ablation: The solid coating material is vaporized through methods such as sputtering or arc discharge.
- Transport: The vaporized material is transported through the vacuum chamber to the target substrate.
- Reaction: The ions of the vaporized material react with a reactive gas, usually nitrogen, to form a thin coating.
- Deposition: The coating material condenses onto the target substrate, forming a thin, pure, and durable layer.
-
Materials Used in PVD Electroplating:
- Common materials used in PVD electroplating include titanium, zirconium, and chromium.
- These materials are chosen for their ability to form coatings with excellent mechanical, chemical, and optical properties.
- The choice of material can also affect the color, finish, and functionality of the final coating.
-
Benefits of PVD Electroplating:
- Durability: PVD coatings are extremely tough and durable, offering high hardness, wear resistance, and corrosion resistance.
- Aesthetic Appeal: PVD electroplating allows for a wide range of colors and finishes, making it suitable for both functional and decorative applications.
- Environmental Friendliness: The PVD process is more environmentally friendly than many other coating technologies, as it occurs under vacuum conditions and does not involve harmful chemicals.
- Versatility: PVD electroplating can be used to deposit various materials, providing a wide range of functionalities and applications.
-
Applications of PVD Electroplating:
- Aerospace: PVD coatings are used to protect aircraft components from corrosion and wear, extending their lifespan and reducing maintenance costs.
- Medical: PVD coatings are used on medical devices and implants to improve their biocompatibility and resistance to wear and corrosion.
- High-Tech: PVD coatings are used in the electronics industry to enhance the performance and durability of components.
- Marine: PVD coatings are suitable for marine environments due to their resistance to saltwater and prolonged exposure to ultraviolet light.
-
Comparison with Traditional Electroplating:
- Process: Traditional electroplating uses an electrochemical process to coat metals, while PVD electroplating uses physical vaporization and condensation.
- Coating Quality: PVD coatings are generally thinner, purer, and more durable than traditional electroplated coatings.
- Environmental Impact: PVD electroplating is more environmentally friendly, as it does not involve harmful chemicals and occurs under vacuum conditions.
- Aesthetic Options: PVD electroplating offers a wider range of colors and finishes compared to traditional electroplating.
In summary, PVD electroplating is a sophisticated and versatile coating technique that offers numerous advantages over traditional electroplating methods. Its ability to produce durable, aesthetically pleasing, and environmentally friendly coatings makes it a preferred choice in various high-performance industries.
Summary Table:
Aspect | Details |
---|---|
Process | Vaporization and condensation in a vacuum chamber |
Materials | Titanium, zirconium, chromium |
Benefits | Durability, aesthetic appeal, environmental friendliness, versatility |
Applications | Aerospace, medical, high-tech, marine |
Comparison | Thinner, purer, and more durable than traditional electroplating |
Upgrade your coating process with PVD electroplating—contact us today to learn more!