Roll forming is a highly efficient and versatile manufacturing process used to shape metal sheets and coils into continuous profiles with a consistent cross-section. This process is widely employed across various industries due to its ability to produce complex shapes with high precision, speed, and cost-effectiveness. Roll forming is particularly advantageous for creating long lengths of metal components, such as roofing panels, structural supports, automotive parts, and more. The process involves passing a metal strip through a series of rollers that gradually bend the material into the desired shape. This method is preferred for its ability to handle high-volume production while maintaining tight tolerances and reducing material waste.
Key Points Explained:
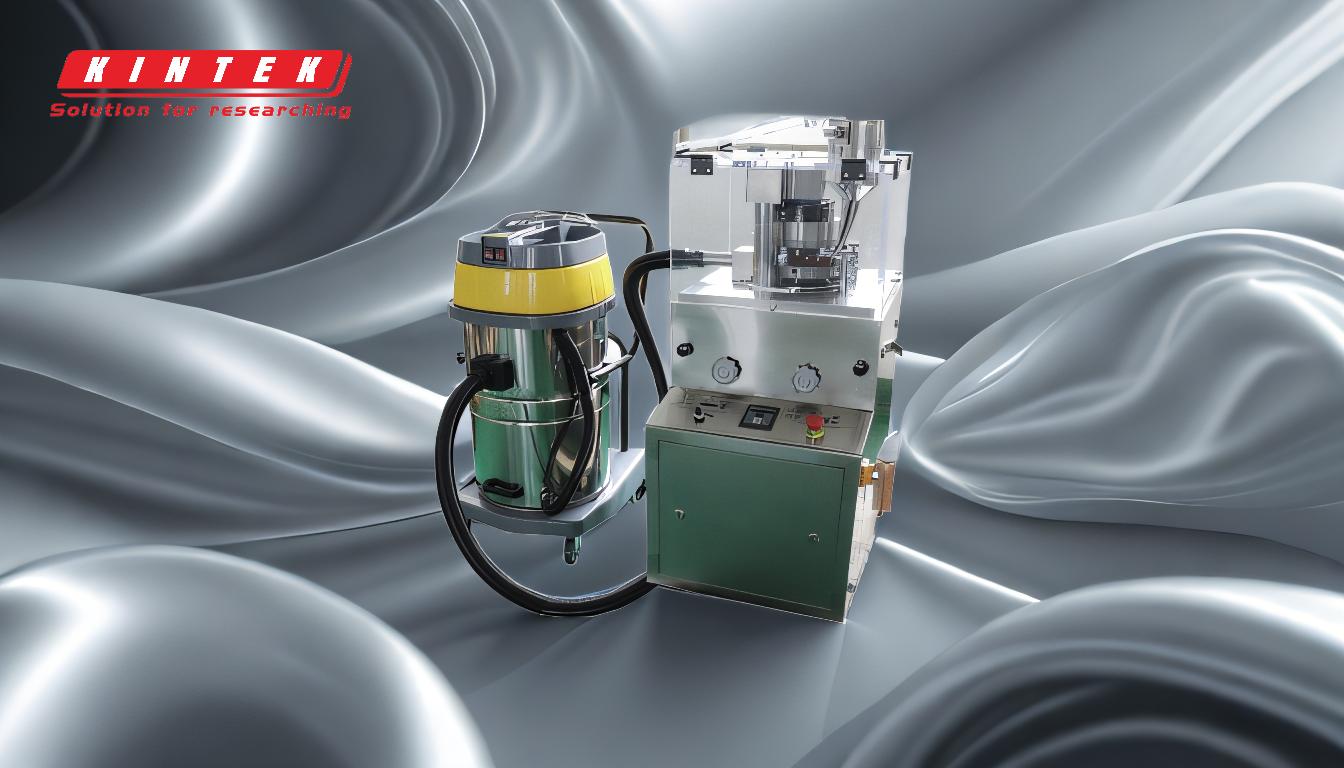
-
Definition and Process of Roll Forming:
- Roll forming is a continuous bending operation where a metal strip is progressively shaped by passing it through a series of rollers, each performing a small incremental bend until the final profile is achieved.
- The process begins with a flat metal coil, which is fed into the roll forming machine. The rollers are arranged in pairs and are designed to progressively shape the metal into the desired cross-section.
-
Applications of Roll Forming:
- Construction Industry: Roll forming is extensively used to produce metal roofing panels, wall cladding, and structural components like steel studs and tracks. These products are essential for modern construction due to their durability, lightweight, and ease of installation.
- Automotive Industry: In the automotive sector, roll forming is used to manufacture parts such as door beams, seat frames, and chassis components. The process allows for the production of lightweight yet strong parts, which are crucial for improving fuel efficiency and safety.
- HVAC Systems: Roll forming is employed to create ductwork and other components used in heating, ventilation, and air conditioning systems. The ability to produce long, continuous sections of metal with precise dimensions makes roll forming ideal for these applications.
- Furniture and Appliances: The process is also used to produce metal frames for furniture, shelving, and household appliances. The consistent quality and aesthetic appeal of roll-formed parts make them suitable for consumer products.
-
Advantages of Roll Forming:
- High Production Speed: Roll forming is a continuous process that can produce long lengths of metal profiles at high speeds, making it ideal for large-scale production.
- Precision and Consistency: The process allows for tight tolerances and consistent quality across large production runs, ensuring that each part meets the required specifications.
- Material Efficiency: Roll forming minimizes material waste by using the exact amount of metal needed to create the desired profile, reducing costs and environmental impact.
- Versatility: The process can be used to create a wide range of complex shapes and profiles, making it suitable for various industries and applications.
-
Challenges and Considerations:
- Tooling Costs: The initial cost of designing and manufacturing the rollers can be high, especially for custom profiles. However, these costs are often offset by the efficiency and volume of production.
- Material Limitations: While roll forming is suitable for a wide range of metals, including steel, aluminum, and copper, it may not be ideal for materials that are too brittle or difficult to bend.
- Design Constraints: The process requires careful consideration of the material properties and the desired profile to ensure that the final product meets the required specifications without defects.
-
Future Trends in Roll Forming:
- Automation and Robotics: The integration of automation and robotics in roll forming is expected to increase efficiency, reduce labor costs, and improve precision.
- Advanced Materials: The development of new materials, such as high-strength alloys and composites, is likely to expand the range of applications for roll forming.
- Sustainability: As industries focus on reducing their environmental impact, roll forming will continue to play a key role due to its material efficiency and ability to produce lightweight, durable products.
In conclusion, roll forming is a critical manufacturing process that offers numerous advantages, including high production speed, precision, and versatility. Its applications span across various industries, from construction and automotive to HVAC and consumer products. While there are challenges associated with tooling costs and material limitations, ongoing advancements in technology and materials are expected to further enhance the capabilities and applications of roll forming in the future.
Summary Table:
Aspect | Details |
---|---|
Applications | Construction, Automotive, HVAC, Furniture & Appliances |
Advantages | High production speed, precision, material efficiency, versatility |
Challenges | High tooling costs, material limitations, design constraints |
Future Trends | Automation, advanced materials, sustainability |
Interested in how roll forming can benefit your industry? Contact us today for expert guidance!