A screw press forging is a type of forging equipment that operates using a motor-driven screw mechanism to apply constant pressure and a long stroke to shape metal workpieces. Unlike other forging methods, screw presses work slowly but can generate significant force, up to 31,000 tons, making them suitable for precision forging tasks. This method is particularly effective for applications requiring consistent pressure over a prolonged period, ensuring high-quality results.
Key Points Explained:
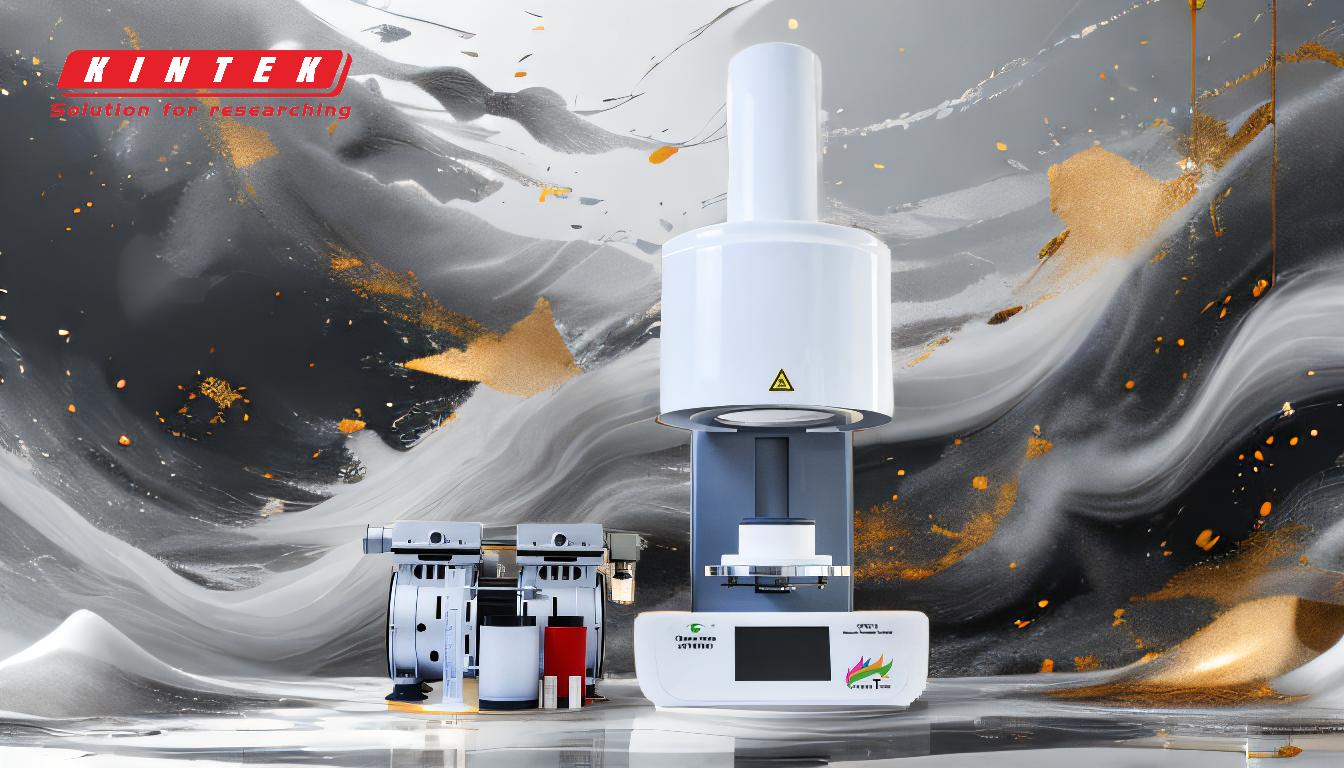
-
Mechanism of Operation:
- A screw press forging machine operates by using a motor to turn a screw, which in turn drives the ram downward onto the workpiece. This mechanism allows for a controlled and steady application of force, which is crucial for achieving precise shapes and dimensions in the forged parts.
-
Force Generation:
- One of the standout features of screw press forging is its ability to generate substantial force, up to 31,000 tons. This high force capability makes it suitable for a wide range of forging applications, including those requiring deep penetration or significant material deformation.
-
Speed and Stroke:
- Screw presses are characterized by their slow operation and long stroke. The slow speed ensures that the force is applied evenly and consistently, which is essential for maintaining the integrity and quality of the forged part. The long stroke allows for greater flexibility in the size and shape of the workpieces that can be processed.
-
Comparison with Hydraulic Forging Presses:
- While hydraulic forging presses use hydraulic cylinders to generate force, screw presses rely on a mechanical screw mechanism. This difference in operation means that screw presses can offer more consistent pressure over time, which is beneficial for certain types of forging tasks. Hydraulic presses, on the other hand, might be preferred for applications requiring rapid force application.
-
Applications:
- Screw press forging is commonly used in industries where precision and consistency are paramount. This includes the automotive, aerospace, and heavy machinery sectors, where high-strength and high-precision components are required.
-
Advantages:
- The primary advantages of screw press forging include the ability to apply consistent pressure, the high force generation capability, and the precision achievable with the slow, controlled operation. These features make it an excellent choice for producing high-quality forged parts with complex geometries.
-
Components:
- While the reference mentions components of a hydraulic forging press, it's important to note that screw presses have their own set of key components, including the motor, screw mechanism, ram, and control systems. These components work together to ensure the machine operates efficiently and effectively.
In summary, screw press forging is a highly effective method for producing precision-forged parts, offering consistent pressure, high force generation, and the ability to handle complex geometries. Its slow, controlled operation makes it particularly suitable for applications where quality and precision are critical.
Summary Table:
Feature | Description |
---|---|
Mechanism | Motor-driven screw mechanism applies steady pressure for precise shaping. |
Force Generation | Generates up to 31,000 tons of force, ideal for deep penetration and deformation. |
Speed and Stroke | Slow operation with a long stroke ensures even pressure and flexibility. |
Applications | Used in automotive, aerospace, and heavy machinery for high-precision parts. |
Advantages | Consistent pressure, high force, and precision for complex geometries. |
Interested in screw press forging for your precision needs? Contact us today to learn more!