A sealed quench furnace is a specialized type of furnace used primarily in heat treatment processes, particularly for metals and alloys. It is designed to provide a controlled atmosphere for heating and cooling materials, ensuring precise thermal treatment. The furnace is sealed to prevent contamination from external gases and to maintain specific atmospheric conditions, such as inert or reducing environments, which are crucial for achieving desired material properties. The quenching process, which involves rapid cooling, is performed within the sealed environment to prevent oxidation or other undesirable reactions. This type of furnace is widely used in industries like metallurgy, aerospace, automotive, and tool manufacturing, where precise heat treatment is critical for material performance.
Key Points Explained:
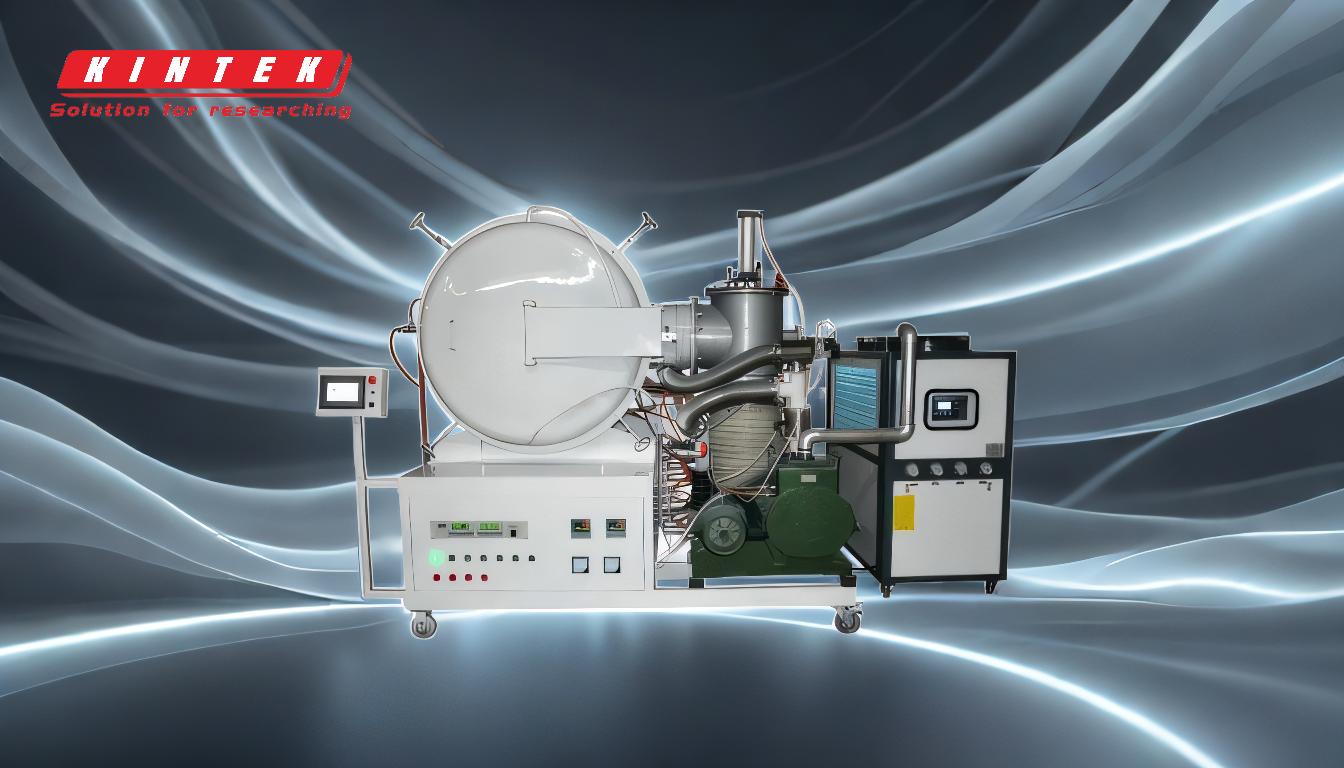
-
Purpose and Applications:
- A sealed quench furnace is primarily used for heat treatment processes, such as annealing, hardening, and tempering of metals and alloys.
- It is widely employed in industries like metallurgy, aerospace, automotive, and tool manufacturing, where precise thermal treatment is essential for material performance.
-
Controlled Atmosphere:
- The furnace is sealed to maintain a controlled atmosphere, which can be inert (e.g., nitrogen or argon) or reducing (e.g., hydrogen).
- This controlled environment prevents oxidation, decarburization, and other undesirable reactions during the heating and cooling processes.
-
Quenching Process:
- Quenching is the rapid cooling of materials to achieve specific mechanical properties, such as hardness or strength.
- In a sealed quench furnace, the quenching process is performed within the sealed environment using a gas quench system. This system circulates an inert gas (e.g., nitrogen) to extract heat from the load at the completion of the heating cycle.
-
Gas Quench System:
- The gas quench system is a critical component of the sealed quench furnace. It cools the inert quench gas, which in turn cools the materials being processed.
- The cooling gas and its pressure can be adjusted to accommodate different materials or desired properties. For example, higher gas pressure can result in faster cooling rates, which may be necessary for certain alloys.
-
Advantages of Sealed Quench Furnaces:
- Precision: The sealed environment allows for precise control over temperature and atmosphere, ensuring consistent and high-quality results.
- Versatility: The ability to adjust the quenching gas and pressure makes the furnace suitable for a wide range of materials and applications.
- Contamination Prevention: The sealed design prevents contamination from external gases, which is crucial for maintaining the integrity of sensitive materials.
-
Industrial Use Cases:
- Metallurgy: Used for heat treating steel, aluminum, and other metals to improve their mechanical properties.
- Aerospace: Critical for processing high-strength alloys used in aircraft components.
- Automotive: Essential for hardening and tempering parts like gears, shafts, and engine components.
- Tool Manufacturing: Used to produce durable and wear-resistant tools.
-
Comparison with Other Furnaces:
- Unlike open furnaces, sealed quench furnaces provide a controlled environment, which is essential for preventing oxidation and ensuring uniform heat treatment.
- Compared to oil or water quenching, gas quenching in a sealed environment is cleaner and reduces the risk of distortion or cracking in the materials.
In summary, a sealed quench furnace is a highly specialized and versatile piece of equipment used for precise heat treatment of metals and alloys. Its sealed design and gas quench system allow for controlled atmospheres and rapid cooling, making it indispensable in industries where material performance is critical.
Summary Table:
Feature | Description |
---|---|
Purpose | Heat treatment processes like annealing, hardening, and tempering of metals. |
Controlled Atmosphere | Sealed environment with inert or reducing gases to prevent oxidation. |
Quenching Process | Rapid cooling within a sealed environment using a gas quench system. |
Applications | Metallurgy, aerospace, automotive, and tool manufacturing industries. |
Advantages | Precision, versatility, and contamination prevention for sensitive materials. |
Learn how a sealed quench furnace can optimize your heat treatment processes—contact our experts today!