Sintering, also known as 'frittage,' is a manufacturing process that uses heat and pressure to form a solid mass of material without reaching the point of liquefaction. This process relies on atomic diffusion across particle boundaries, causing particles to fuse into a cohesive structure. Sintering is widely used in industries such as metallurgy, ceramics, and powder metallurgy to create durable and complex components. The process is facilitated by specialized equipment like a sintering furnace, which employs heating methods such as ceramic elements (e.g., molybdenum disilicide or silicon carbide) or microwaves to achieve the desired results.
Key Points Explained:
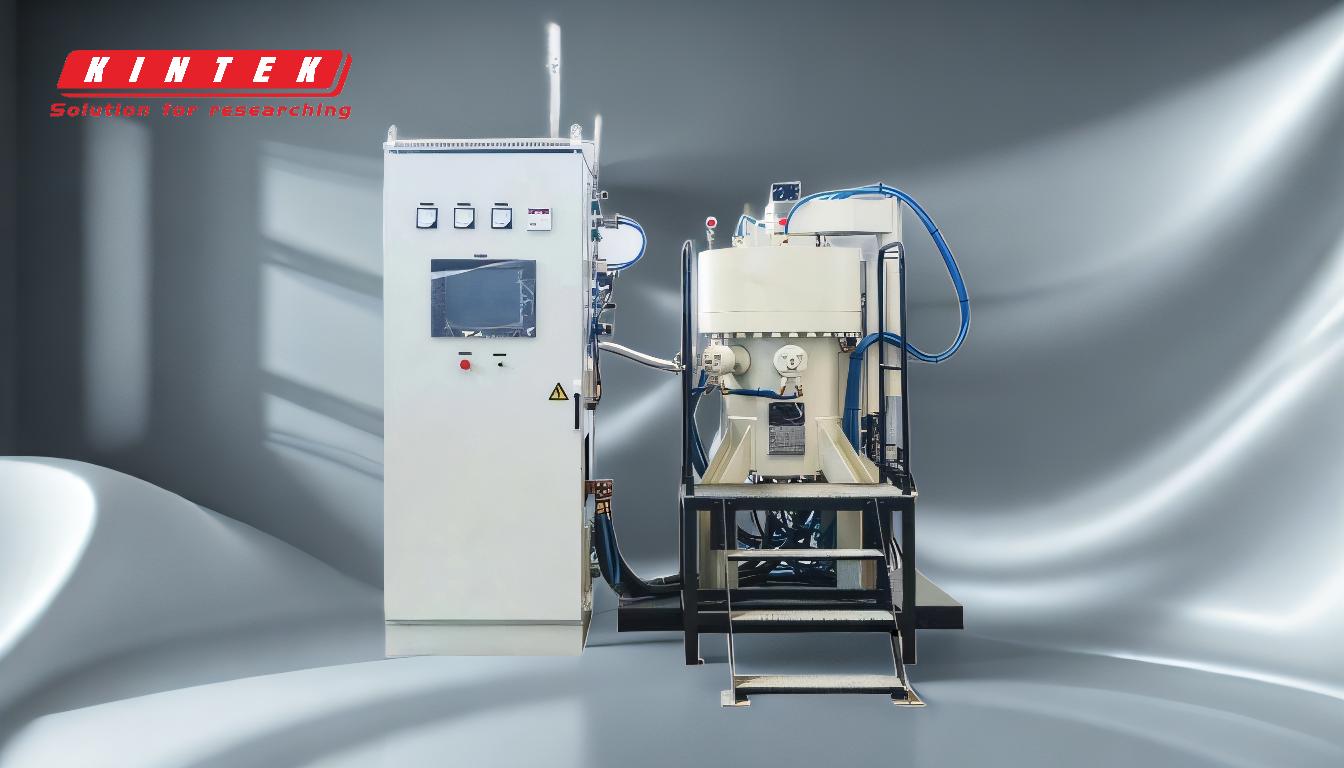
-
Definition of Sintering:
- Sintering, or 'frittage,' is a process that bonds particles together using heat and pressure without melting the material completely. This allows the creation of solid structures with improved mechanical properties, such as strength and density.
-
Mechanism of Sintering:
- The process involves atomic diffusion, where atoms move across particle boundaries and fuse together. This results in the reduction of porosity and the formation of a dense, cohesive material.
-
Applications of Sintering:
- Sintering is used in various industries, including:
- Metallurgy: To produce metal parts with high strength and durability.
- Ceramics: To create complex shapes and structures with enhanced properties.
- Powder Metallurgy: To manufacture components from metal powders, such as gears and bearings.
- Sintering is used in various industries, including:
-
Role of a Sintering Furnace:
- A sintering furnace is essential for the sintering process. It provides the controlled environment needed to apply heat and pressure effectively. The furnace ensures uniform heating and precise temperature control, which are critical for achieving consistent results.
-
Heating Methods in Sintering:
- Sintering furnaces employ two primary heating methods:
- Ceramic Elements: Made from materials like molybdenum disilicide (MoSi2) or silicon carbide (SiC), these elements are widely used due to their high-temperature stability and efficiency.
- Microwave Sintering: A newer technology that uses microwave energy to heat materials uniformly and rapidly. This method is gaining popularity for its energy efficiency and ability to produce fine-grained microstructures.
- Sintering furnaces employ two primary heating methods:
-
Advantages of Sintering:
- The sintering process offers several benefits, including:
- The ability to produce complex shapes with high precision.
- Improved material properties, such as increased strength and reduced porosity.
- Cost-effectiveness in manufacturing, especially for large-scale production.
- The sintering process offers several benefits, including:
By understanding the principles and applications of sintering, as well as the role of a sintering furnace, manufacturers can optimize their processes to create high-quality components efficiently.
Summary Table:
Aspect | Details |
---|---|
Definition | Sintering, or 'frittage,' bonds particles using heat and pressure without melting. |
Mechanism | Atomic diffusion fuses particles, reducing porosity and forming dense structures. |
Applications | Used in metallurgy, ceramics, and powder metallurgy for durable components. |
Role of Sintering Furnace | Provides controlled heat and pressure for uniform heating and precise results. |
Heating Methods | Ceramic elements (e.g., MoSi2, SiC) or microwave sintering for efficiency. |
Advantages | Produces complex shapes, improves strength, and reduces manufacturing costs. |
Ready to optimize your sintering process? Contact our experts today to learn more!