Sintering in porcelain is a critical process that transforms a porous, fragile ceramic body into a dense, strong, and durable material. It involves heating the shaped ceramic (green body) in a sintering furnace to high temperatures, causing the particles to bond at their surfaces without melting the entire material. This process reduces porosity, increases density, and enhances mechanical properties. The sintering process typically occurs in three stages: shaping the powder blend with a bonding agent, removing the bonding agent through heating, and fusing the particles at high temperatures to achieve the final product.
Key Points Explained:
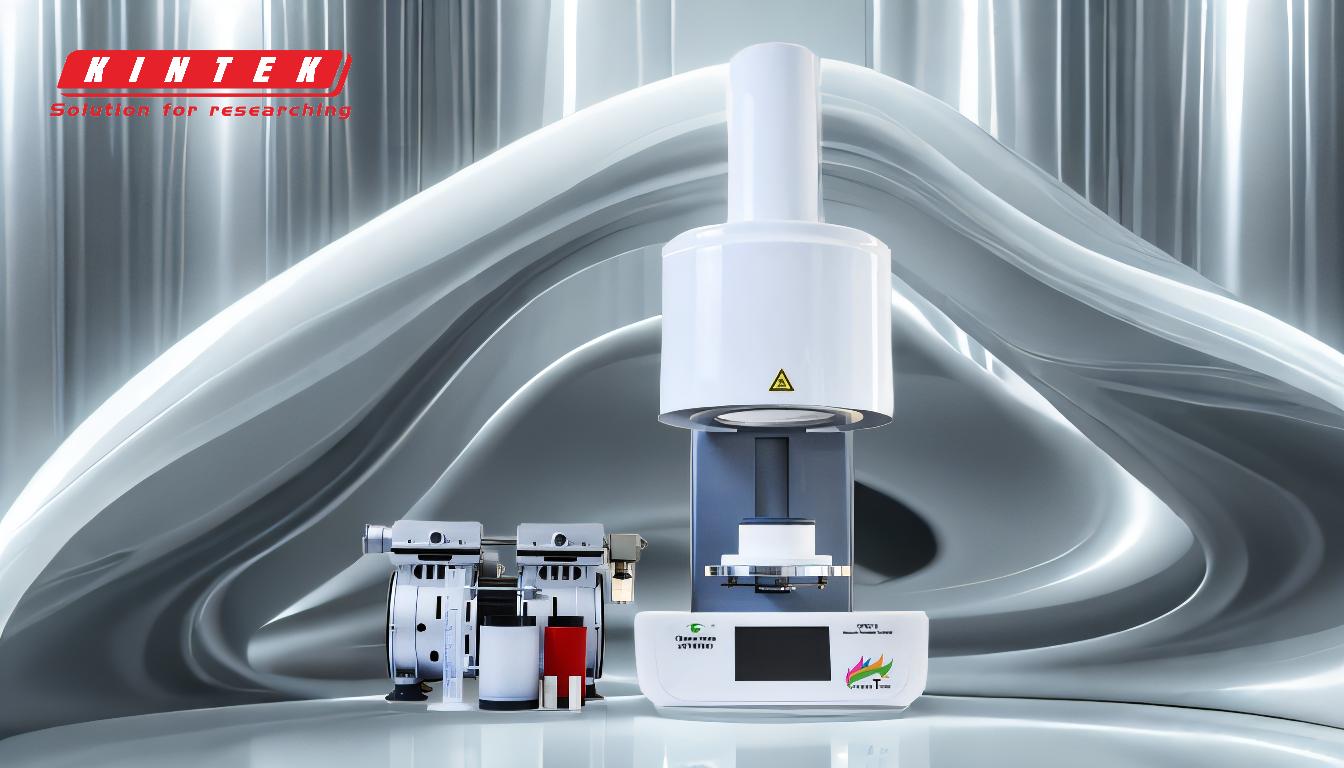
-
Definition of Sintering in Porcelain:
- Sintering is a thermal process used to compact and strengthen ceramic materials, such as porcelain, by applying high temperatures below the material's melting point. This process forces atoms to bond more tightly, resulting in a denser and stronger final product.
- The primary goal is to reduce porosity and increase the mechanical strength of the ceramic body.
-
Stages of the Sintering Process:
-
Stage 1: Forming the Green Body:
- A mixture of ceramic powder and a bonding agent (e.g., water, wax, or polymer) is shaped into the desired form. The bonding agent holds the powder particles together temporarily.
-
Stage 2: Removal of the Bonding Agent:
- The green body is heated in a sintering furnace to evaporate or burn away the bonding agent. This step is crucial to prepare the material for the final sintering stage.
-
Stage 3: Particle Fusion:
- The temperature is increased further, causing the ceramic particles to bond at their surfaces. This fusion reduces porosity and increases the material's density and strength.
-
Stage 1: Forming the Green Body:
-
Role of the Sintering Furnace:
- The sintering furnace is essential for achieving the high temperatures required for the sintering process. It provides controlled heating to ensure uniform particle bonding and prevent defects in the final product.
- The furnace must maintain precise temperature control to avoid over-sintering, which can lead to warping or melting of the ceramic material.
-
Benefits of Sintering in Porcelain:
- Increased Density: Sintering reduces the porosity of the ceramic body, making it denser and more durable.
- Enhanced Strength: The bonding of particles at high temperatures significantly improves the mechanical strength of the porcelain.
- Improved Hardness: Sintering results in a harder material, making it suitable for applications requiring wear resistance.
- Dimensional Stability: The process minimizes volume shrinkage and ensures the final product retains its intended shape.
-
Applications of Sintered Porcelain:
- Sintered porcelain is widely used in industries such as electronics, aerospace, and medical devices due to its excellent mechanical and thermal properties.
- Common applications include insulators, dental ceramics, and high-performance components requiring precision and durability.
-
Challenges in the Sintering Process:
- Temperature Control: Achieving the right temperature is critical to avoid defects like cracking or warping.
- Uniform Heating: Uneven heating can lead to inconsistent material properties.
- Material Selection: The choice of ceramic powder and bonding agent affects the sintering outcome.
In summary, sintering is a vital process in porcelain manufacturing that transforms a fragile green body into a strong, dense, and durable material. The use of a sintering furnace ensures precise temperature control, enabling the successful fusion of ceramic particles and the production of high-quality porcelain products.
Summary Table:
Key Aspect | Details |
---|---|
Definition | Thermal process to compact and strengthen porcelain below melting point. |
Stages | 1. Forming the green body 2. Removing bonding agent 3. Particle fusion |
Role of Sintering Furnace | Ensures precise temperature control for uniform particle bonding. |
Benefits | Increased density, enhanced strength, improved hardness, dimensional stability. |
Applications | Electronics, aerospace, medical devices, dental ceramics. |
Challenges | Temperature control, uniform heating, material selection. |
Discover how sintering can enhance your porcelain manufacturing—contact our experts today!