SPS (Spark Plasma Sintering) processing is an advanced materials fabrication technique that combines the principles of hot pressing and pulsed electric current to achieve rapid and efficient sintering of materials. This process is characterized by its ability to produce materials with unique microstructures and properties through precise control of temperature, pressure, and heating rates. SPS operates in a vacuum or controlled atmosphere to prevent oxidation and ensure material purity. The process involves four main stages: gas removal and vacuum creation, pressure application, resistive heating, and cooling. The spark plasma effect, generated by pulsed currents, inhibits particle growth and enables the creation of materials with tailored compositions and properties. SPS is widely used in research and industrial applications, particularly for synthesizing advanced materials like ultra-high temperature ceramics.
Key Points Explained:
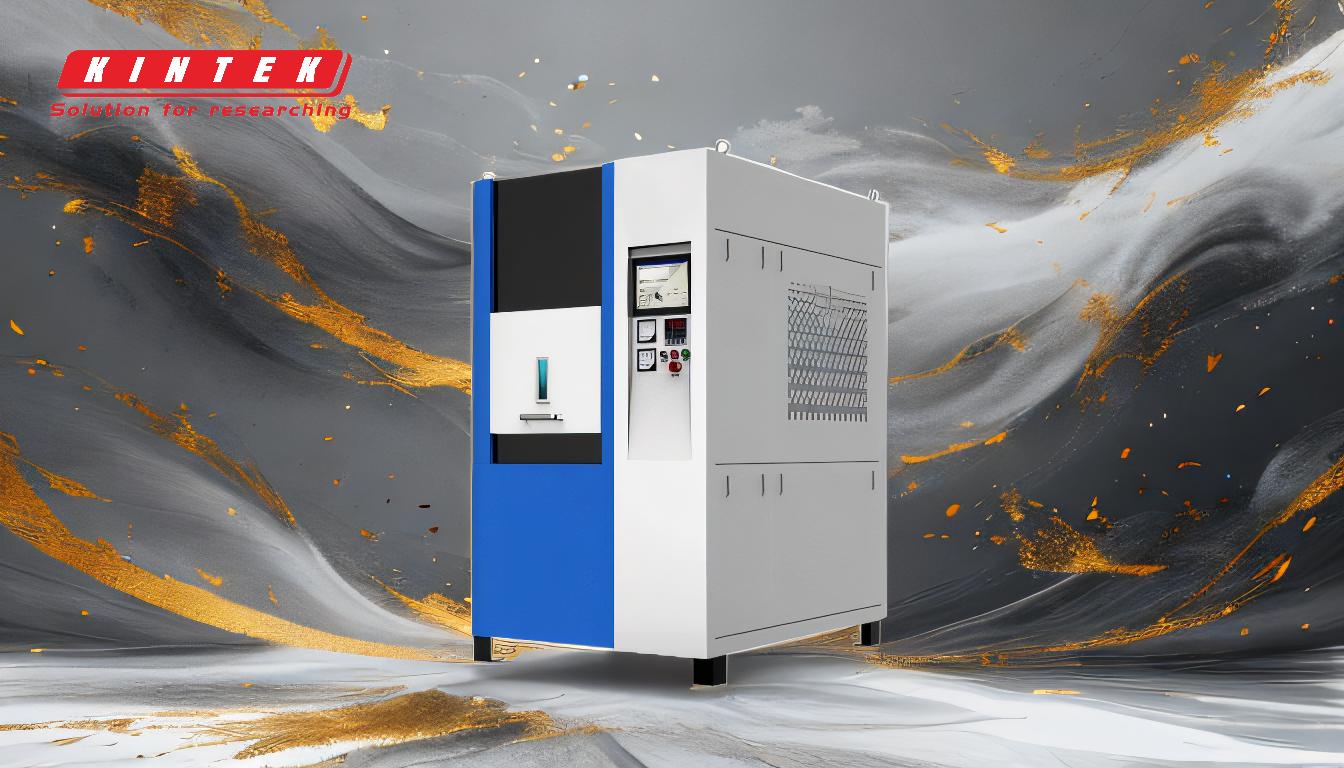
-
Definition and Purpose of SPS Processing:
- SPS, or Spark Plasma Sintering, is a materials fabrication technique that combines hot pressing with pulsed electric currents to sinter materials efficiently.
- It is designed to produce materials with unique microstructures and properties, such as high-density ceramics, nanomaterials, and composites, which are difficult to achieve using conventional methods.
-
Core Mechanism: Spark Plasma Effect:
- The process relies on the "spark plasma effect," where pulsed electric currents generate localized high temperatures at particle surfaces.
- This effect causes evaporation, melting, and the formation of necks between particles, leading to rapid densification and sintering.
- The spark plasma effect also inhibits particle growth, enabling the creation of fine-grained materials with enhanced mechanical and thermal properties.
-
Key Stages of the SPS Process:
-
Stage 1: Gas Removal and Vacuum Creation:
- The chamber is evacuated to remove gases and create a vacuum, preventing oxidation and ensuring material purity.
-
Stage 2: Pressure Application:
- Uniaxial pressure is applied to the powder compact to facilitate particle rearrangement and densification.
-
Stage 3: Resistive Heating:
- Pulsed electric currents flow through the graphite die and the sample, generating heat through resistive heating.
-
Stage 4: Cooling:
- After sintering, the sample is cooled under controlled conditions to preserve the desired microstructure and properties.
-
Stage 1: Gas Removal and Vacuum Creation:
-
Advantages of SPS Processing:
-
High Heating Rates and Short Processing Times:
- SPS achieves heating rates of up to hundreds of degrees per minute, significantly reducing processing times compared to conventional sintering methods.
-
Low Sintering Temperatures:
- The process operates at lower temperatures than traditional sintering, minimizing grain growth and preserving fine microstructures.
-
Precise Control:
- Temperature, pressure, and heating rates can be precisely controlled, enabling the fabrication of materials with tailored properties.
-
Versatility:
- SPS is suitable for a wide range of materials, including ceramics, metals, composites, and nanomaterials.
-
High Heating Rates and Short Processing Times:
-
Applications of SPS Technology:
-
Synthesis of Advanced Materials:
- SPS is used to produce ultra-high temperature ceramics (e.g., ZrC), nanomaterials, and functionally graded materials.
-
Research and Development:
- The technique is widely used in material science research to explore new compositions and properties.
-
Industrial Manufacturing:
- SPS is employed in industries requiring high-performance materials, such as aerospace, automotive, and electronics.
-
Synthesis of Advanced Materials:
-
Equipment and Process Control:
-
Graphite Dies:
- Graphite is commonly used for the pressing die due to its high thermal and electrical conductivity.
-
Touch Screen Interface:
- The process is controlled and programmed using a touch screen, allowing for precise adjustment of parameters and real-time monitoring.
-
Vacuum or Controlled Atmosphere:
- The process is conducted in a vacuum or inert gas environment to prevent contamination and ensure material purity.
-
Graphite Dies:
-
Comparison with Conventional Methods:
- SPS offers significant advantages over conventional sintering methods, such as faster processing times, lower energy consumption, and the ability to produce materials with unique properties.
- Conventional methods often require higher temperatures and longer processing times, leading to grain growth and reduced material performance.
In summary, SPS processing is a cutting-edge technology that enables the rapid and precise fabrication of advanced materials. Its unique combination of pulsed electric currents, controlled pressure, and high heating rates makes it a powerful tool for material scientists and engineers. Whether for research or industrial applications, SPS offers unparalleled control and versatility, making it a key technology in the development of next-generation materials.
Summary Table:
Aspect | Details |
---|---|
Definition | Combines hot pressing and pulsed electric currents for efficient sintering. |
Core Mechanism | Spark plasma effect enables rapid densification and fine-grained materials. |
Key Stages | Gas removal, pressure application, resistive heating, and controlled cooling. |
Advantages | High heating rates, low sintering temperatures, precise control, versatility. |
Applications | Synthesis of ceramics, nanomaterials, and industrial high-performance materials. |
Equipment | Graphite dies, touch screen interface, vacuum/controlled atmosphere. |
Comparison | Faster, lower energy consumption, and superior material properties vs. conventional methods. |
Unlock the potential of advanced materials with SPS technology—contact our experts today to learn more!