Sputtering metal refers to a physical vapor deposition (PVD) process where metal atoms are ejected from a solid target material due to bombardment by high-energy ions, typically from an inert gas like argon. These ejected atoms then deposit onto a substrate, forming a thin, uniform metal film. This technique is widely used in industries such as semiconductors, optics, aerospace, and consumer electronics to create high-quality coatings for various applications. Sputtering is valued for its precision, ability to deposit complex materials, and versatility in producing thin films with specific properties like conductivity, reflectivity, or corrosion resistance.
Key Points Explained:
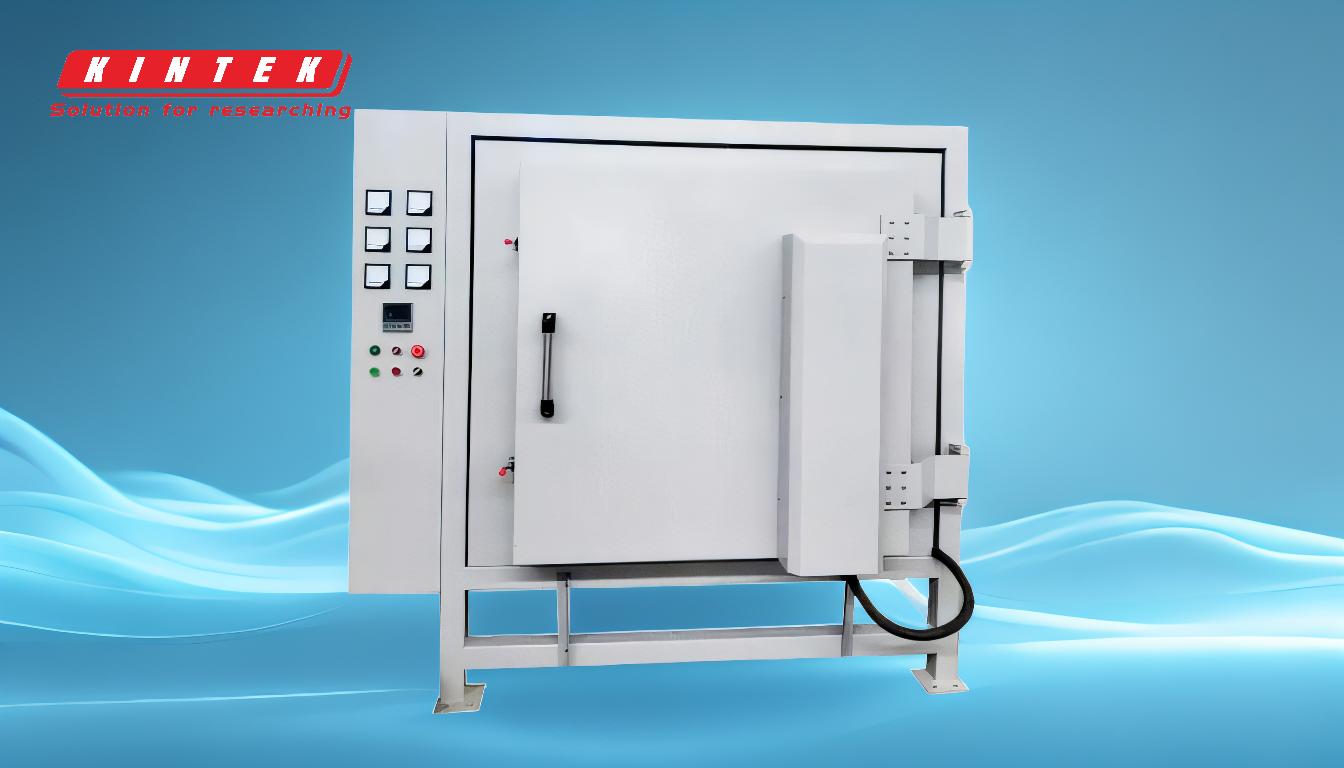
-
What is Sputtering?
- Sputtering is a physical process where ions of an inert gas (e.g., argon) are accelerated into a solid metal target, causing atoms from the target to be ejected.
- These ejected atoms are neutral and travel through a vacuum chamber to deposit onto a substrate, forming a thin film.
-
How Does Sputtering Work?
- A vacuum chamber is used to create a controlled environment.
- Inert gas ions are introduced and accelerated toward the target material using an electric field.
- The high-energy ions collide with the target, transferring energy and ejecting target atoms.
- The ejected atoms travel through the vacuum and deposit onto a substrate, forming a thin film.
-
Applications of Sputtering Metal:
- Semiconductor Industry: Used to deposit thin films of metals and alloys in integrated circuit manufacturing.
- Optical Industry: Creates anti-reflective coatings, polarization filters, and reflective coatings for mirrors.
- Architectural Glass: Produces low-emissivity coatings for energy-efficient windows.
- Aerospace and Defense: Applies specialized coatings like gadolinium films for neutron radiography.
- Consumer Electronics: Used in the production of CDs, DVDs, hard disks, and packaging materials.
- Medical Devices: Deposits dielectric stacks to electrically isolate surgical tools.
- Solar Energy: Manufactures photovoltaic solar cells and optical waveguides.
-
Advantages of Sputtering:
- Precision: Allows for the deposition of extremely thin and uniform films, ranging from nanometers to micrometers in thickness.
- Versatility: Can deposit a wide range of materials, including metals, alloys, and compounds.
- High-Quality Coatings: Produces coatings with excellent adhesion, uniformity, and specific functional properties.
- Scalability: Suitable for both small-scale research and large-scale industrial production.
-
Materials Used in Sputtering:
- Target Materials: Metals like aluminum, copper, gold, and titanium, as well as alloys and compounds.
- Inert Gases: Typically argon, due to its inert nature and ability to generate high-energy ions.
-
Historical Context:
- Sputtering has been a well-established technique since the early 1800s.
- It has evolved over time to become a critical process in modern manufacturing and material science.
-
Industrial Impact:
- Enables the production of smaller, lighter, and more durable products.
- Plays a key role in advancing technologies in electronics, optics, and renewable energy.
By understanding sputtering metal, purchasers of equipment and consumables can better appreciate its role in creating high-performance materials and coatings, ensuring they select the right tools and materials for their specific applications.
Summary Table:
Aspect | Details |
---|---|
What is Sputtering? | A PVD process where metal atoms are ejected from a target and deposited onto a substrate. |
How It Works | Inert gas ions bombard a target, ejecting atoms that form a thin film on a substrate. |
Applications | Semiconductors, optics, aerospace, consumer electronics, medical devices, solar energy. |
Advantages | Precision, versatility, high-quality coatings, scalability. |
Materials Used | Target materials: aluminum, copper, gold, titanium; Inert gases: argon. |
Industrial Impact | Enables smaller, lighter, and more durable products in electronics and optics. |
Discover how sputtering metal can enhance your manufacturing process—contact our experts today!