Annealing is a heat treatment process widely used in industry to alter the physical and mechanical properties of materials, primarily metals. The process involves heating the material to a specific temperature, holding it at that temperature to allow changes in its microstructure, and then cooling it slowly. This process reduces hardness, increases ductility, and relieves internal stresses, making the material easier to machine, shape, or further process. Annealing is particularly useful for reversing the effects of work hardening, improving electrical properties, and preparing materials for subsequent manufacturing steps. It is a critical process in industries such as metalworking, electronics, and manufacturing, where material workability and performance are essential.
Key Points Explained:
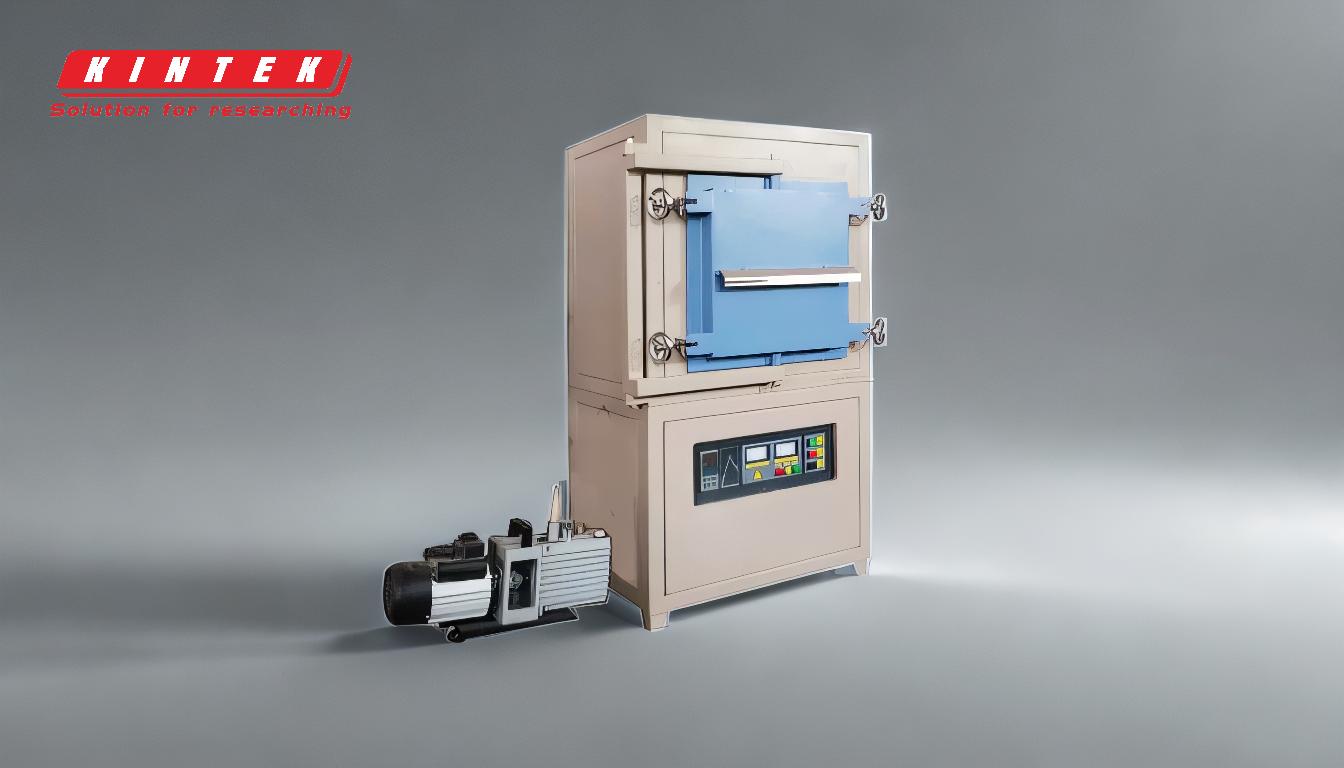
-
Purpose of Annealing:
- Annealing is primarily used to improve the machinability, mechanical properties, and electrical properties of materials.
- It relieves internal stresses caused by processes like cold working, welding, or machining.
- It increases ductility, making the material less brittle and more workable.
- It reduces hardness, which is beneficial for further processing such as machining or cold working.
-
Annealing Process Steps:
- Heating: The material is heated to a specific temperature where its crystalline structure becomes fluid but remains in a solid state. This temperature varies depending on the material.
- Soaking: The material is held at this temperature for a period of time to allow defects in the microstructure to repair themselves.
- Cooling: The material is cooled slowly to room temperature, which promotes the formation of a more ductile and uniform crystalline structure.
-
Applications of Annealing:
- Reversing Work Hardening: Annealing is used to counteract the effects of work hardening, which occurs during processes like cold forming, drawing, or bending. This restores the material's ductility, allowing for further shaping without cracking.
- Stress Relief: It removes internal stresses induced by welding, grinding, or machining, preventing distortion or failure during subsequent processing or service.
- Improving Electrical Properties: In some cases, annealing enhances the electrical conductivity of materials, making them more suitable for electrical applications.
- Preparation for Further Processing: Annealing softens the material, making it easier to machine or undergo additional heat treatments.
-
Benefits of Annealing:
- Increased Ductility: The material becomes more pliable and less prone to cracking under stress.
- Reduced Hardness: This makes the material easier to cut, shape, or machine.
- Improved Microstructure: Annealing produces a more uniform and homogeneous internal structure, enhancing the material's overall performance.
- Stress Relief: It eliminates residual stresses that could lead to failure or distortion during use.
-
Industries and Materials:
- Annealing is widely used in metalworking for materials like steel, aluminum, copper, and brass.
- It is essential in industries such as automotive, aerospace, electronics, and manufacturing, where material properties like ductility, hardness, and stress resistance are critical.
-
Types of Annealing:
- Full Annealing: Involves heating the material to a high temperature and cooling it slowly to achieve maximum softness and ductility.
- Process Annealing: Used to soften the material for further cold working, typically at lower temperatures than full annealing.
- Stress Relief Annealing: Focuses on relieving internal stresses without significantly altering the material's hardness or microstructure.
By understanding the annealing process, industries can optimize material properties for specific applications, ensuring better performance, durability, and ease of manufacturing.
Summary Table:
Aspect | Details |
---|---|
Purpose | Improves machinability, mechanical properties, and electrical properties. |
Process Steps | Heating, soaking, and slow cooling. |
Applications | Reverses work hardening, relieves stress, improves electrical conductivity. |
Benefits | Increases ductility, reduces hardness, improves microstructure. |
Industries | Metalworking, automotive, aerospace, electronics, manufacturing. |
Types of Annealing | Full, process, and stress relief annealing. |
Optimize your material properties with annealing—contact our experts today to learn more!