Press forging is a manufacturing process that involves shaping metal using compressive forces applied through a press. This method is widely used across various industries due to its ability to produce high-strength, precise, and complex components. The applications of press forging are extensive, ranging from automotive and aerospace industries to construction and heavy machinery. It is particularly valued for its efficiency, ability to handle large volumes, and the production of parts with superior mechanical properties. The process is also adaptable to different materials, including steel, aluminum, and titanium, making it versatile for a wide range of applications.
Key Points Explained:
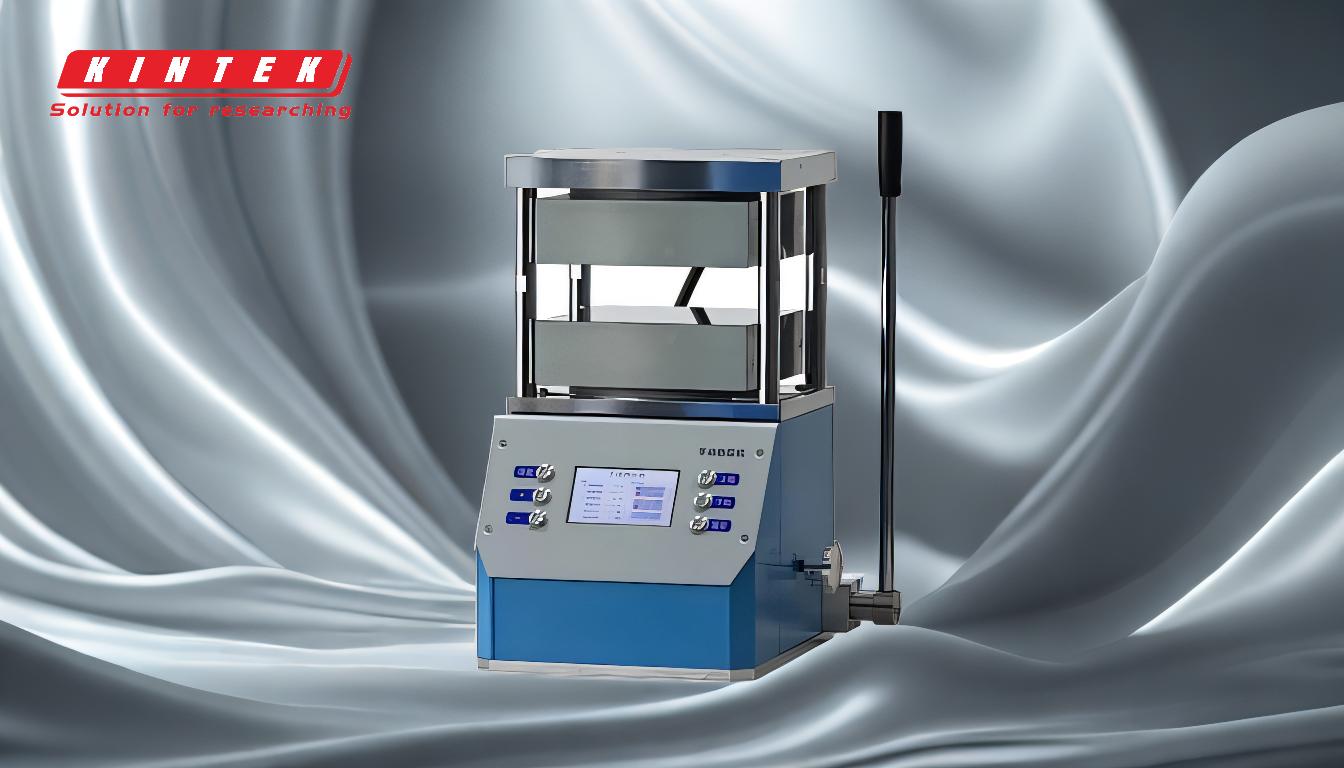
-
Automotive Industry:
- Engine Components: Press forging is extensively used to manufacture critical engine parts such as crankshafts, connecting rods, and camshafts. These components require high strength and durability, which press forging can provide.
- Transmission Parts: Gears, shafts, and other transmission components are often produced using press forging due to the need for precise dimensions and high wear resistance.
- Chassis and Suspension: Components like control arms, steering knuckles, and axle beams are commonly forged to ensure they can withstand the stresses and strains of vehicle operation.
-
Aerospace Industry:
- Structural Components: Press forging is used to produce structural parts of aircraft, such as wing spars, landing gear, and engine mounts. These parts must be lightweight yet strong, and press forging meets these requirements.
- Turbine Blades: The aerospace industry also uses press forging to create turbine blades for jet engines, which must endure extreme temperatures and stresses.
-
Construction and Heavy Machinery:
- Cranes and Excavators: Components like hooks, pins, and brackets used in heavy machinery are often forged to ensure they can handle heavy loads and harsh working conditions.
- Construction Equipment: Parts such as bulldozer blades, excavator buckets, and hydraulic cylinders are typically forged to provide the necessary strength and durability.
-
Oil and Gas Industry:
- Drilling Equipment: Press forging is used to manufacture components for drilling rigs, such as drill bits, valves, and connectors, which must withstand high pressures and corrosive environments.
- Pipeline Components: Flanges, fittings, and other pipeline parts are often forged to ensure they can handle the high pressures and stresses associated with oil and gas transportation.
-
Defense and Military:
- Weapon Systems: Components for firearms, tanks, and other military equipment are often produced using press forging to ensure reliability and durability in combat conditions.
- Armor Plating: Forged armor plates are used in military vehicles and personnel protection due to their high strength and resistance to penetration.
-
Medical Industry:
- Surgical Instruments: High-precision surgical tools and implants are often forged to ensure they meet the stringent requirements for strength, durability, and biocompatibility.
- Orthopedic Implants: Components like hip and knee replacements are typically forged to provide the necessary mechanical properties and longevity.
-
Energy Sector:
- Wind Turbines: Press forging is used to produce components for wind turbines, such as gears and shafts, which must endure constant stress and environmental exposure.
- Nuclear Power Plants: Critical components for nuclear reactors, such as reactor vessel heads and steam generator parts, are often forged to ensure safety and reliability.
-
Railway Industry:
- Wheels and Axles: Railway wheels and axles are commonly forged to provide the necessary strength and durability for safe and reliable train operation.
- Couplers and Brake Systems: Components like couplers and brake system parts are often forged to ensure they can handle the stresses of heavy loads and frequent use.
-
Marine Industry:
- Propeller Shafts: Press forging is used to manufacture propeller shafts and other critical components for ships, which must withstand the harsh marine environment.
- Anchors and Chains: Forged anchors and chains are essential for the safe operation of marine vessels, providing the necessary strength and durability.
-
General Manufacturing:
- Tools and Dies: Press forging is used to produce high-strength tools and dies for various manufacturing processes, ensuring they can withstand the rigors of repeated use.
- Fasteners: Bolts, nuts, and other fasteners are often forged to provide the necessary strength and reliability for critical applications.
In summary, press forging is a versatile and essential manufacturing process used across a wide range of industries to produce high-strength, durable, and precise components. Its applications are vast, from automotive and aerospace to construction, defense, and beyond, making it a critical technology in modern manufacturing.
Summary Table:
Industry | Applications |
---|---|
Automotive | Engine components, transmission parts, chassis, and suspension systems |
Aerospace | Structural components, turbine blades, landing gear |
Construction | Cranes, excavators, bulldozer blades, hydraulic cylinders |
Oil and Gas | Drilling equipment, pipeline components, valves, and connectors |
Defense and Military | Weapon systems, armor plating, military vehicles |
Medical | Surgical instruments, orthopedic implants |
Energy | Wind turbine components, nuclear reactor parts |
Railway | Wheels, axles, couplers, brake systems |
Marine | Propeller shafts, anchors, chains |
General Manufacturing | Tools, dies, fasteners |
Interested in leveraging press forging for your industry? Contact us today to learn more!