Sintering is a critical process in powder metallurgy, used to transform compacted metal powders into strong, durable, and precise components. It involves heating the powder compact below its melting point in a controlled atmosphere, allowing particles to bond and densify. This process enhances the mechanical properties of the material, such as hardness, toughness, and abrasion resistance, while enabling the production of complex shapes that are difficult to achieve with traditional manufacturing methods. Sintering is widely applied in industries like automotive, aerospace, and tool manufacturing, where it enables cost-effective, high-precision production of parts such as gears, camshafts, and cutting tools.
Key Points Explained:
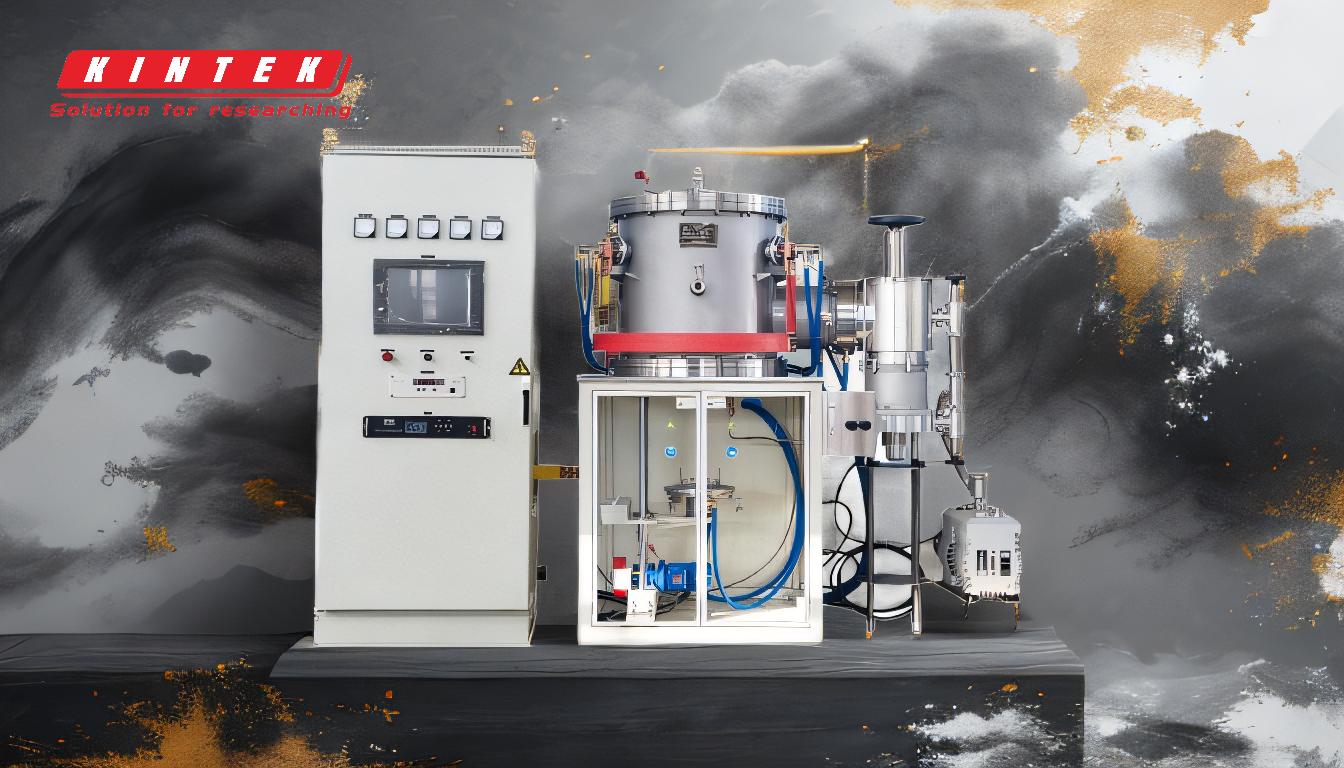
-
Definition and Purpose of Sintering in Powder Metallurgy:
- Sintering is a heat treatment process that bonds metal powder particles together without melting them, enhancing their strength and structural integrity.
- It transforms a "green compact" (a pressed powder form) into a dense, durable component with improved mechanical properties.
-
Key Advantages of Sintering:
- Complex Shapes and Precision: Sintering allows for the production of intricate geometries that are challenging to achieve with conventional methods like casting or forging.
- Material Flexibility: It can combine multiple materials, merging properties like toughness and abrasion resistance in a single component.
- Cost-Effectiveness: Lower tooling costs and the ability to mass-produce parts with high repeatability make sintering economically advantageous.
- Avoidance of Melting: Since sintering occurs below the melting point, it avoids issues like decomposition or excessive shrinkage associated with liquid-phase processes.
-
Mechanism of Sintering:
- The process involves heating the green compact to a temperature just below the metal's melting point in a controlled atmosphere.
- Heat causes the metal particles to bond through diffusion, closing porous spaces and increasing density.
- The controlled atmosphere prevents oxidation and ensures proper bonding, resulting in a strong, homogeneous structure.
-
Applications in Powder Metallurgy:
- Automotive Industry: Sintering is used to produce critical components like gears, camshafts, and valve seats, which require high precision and durability.
- Cutting Tools: Sintered materials are ideal for manufacturing cutting tools due to their hardness and wear resistance.
- Sintered Filters: Porous sintered components are used as filters in various industrial applications.
- Aerospace and Defense: Sintering is employed to create lightweight, high-strength parts for aircraft and military equipment.
-
Comparison with Traditional Manufacturing Methods:
- Unlike casting, forging, or extrusion, sintering does not require a solid-to-liquid phase change, making it more flexible and suitable for materials that decompose at high temperatures.
- It offers better dimensional accuracy and repeatability, making it ideal for high-volume production.
-
Industrial Examples of Sintering:
- Iron and Steel Production: Sintering is used to process iron ore mixed with coke, creating lumps suitable for blast furnace steel production.
- Ceramics and Glass: The process is also applied in the manufacture of ceramic and glass components, where it enhances strength and durability.
-
Future Trends and Innovations:
- Advances in sintering technology, such as spark plasma sintering (SPS) and microwave sintering, are improving efficiency and enabling the production of advanced materials.
- The growing demand for lightweight, high-performance components in industries like electric vehicles and renewable energy is driving further adoption of sintering in powder metallurgy.
By leveraging sintering, manufacturers can achieve a balance of cost, precision, and performance, making it a cornerstone of modern powder metallurgy and a key enabler of innovation in various industries.
Summary Table:
Key Aspect | Details |
---|---|
Definition | A heat treatment process bonding metal powders below melting point. |
Advantages | - Complex shapes & precision - Material flexibility - Cost-effective |
Mechanism | Heating in controlled atmosphere to bond particles and increase density. |
Applications | Automotive, aerospace, cutting tools, sintered filters. |
Future Trends | Spark plasma sintering, microwave sintering, lightweight components. |
Discover how sintering can revolutionize your manufacturing process—contact our experts today!