Magnetron sputtering is a plasma-based thin-film deposition technique widely used in industries for coating substrates with high-quality materials. The process involves bombarding a target material with high-energy ions, causing atoms to be ejected from the target surface and deposited onto a substrate. A magnetic field is used to control the movement of charged particles, enhancing plasma density and deposition efficiency. This method operates in a high-vacuum environment, utilizing inert gases like argon to create plasma. The combination of electric and magnetic fields ensures a stable and efficient sputtering process, making it ideal for applications requiring precise and uniform coatings.
Key Points Explained:
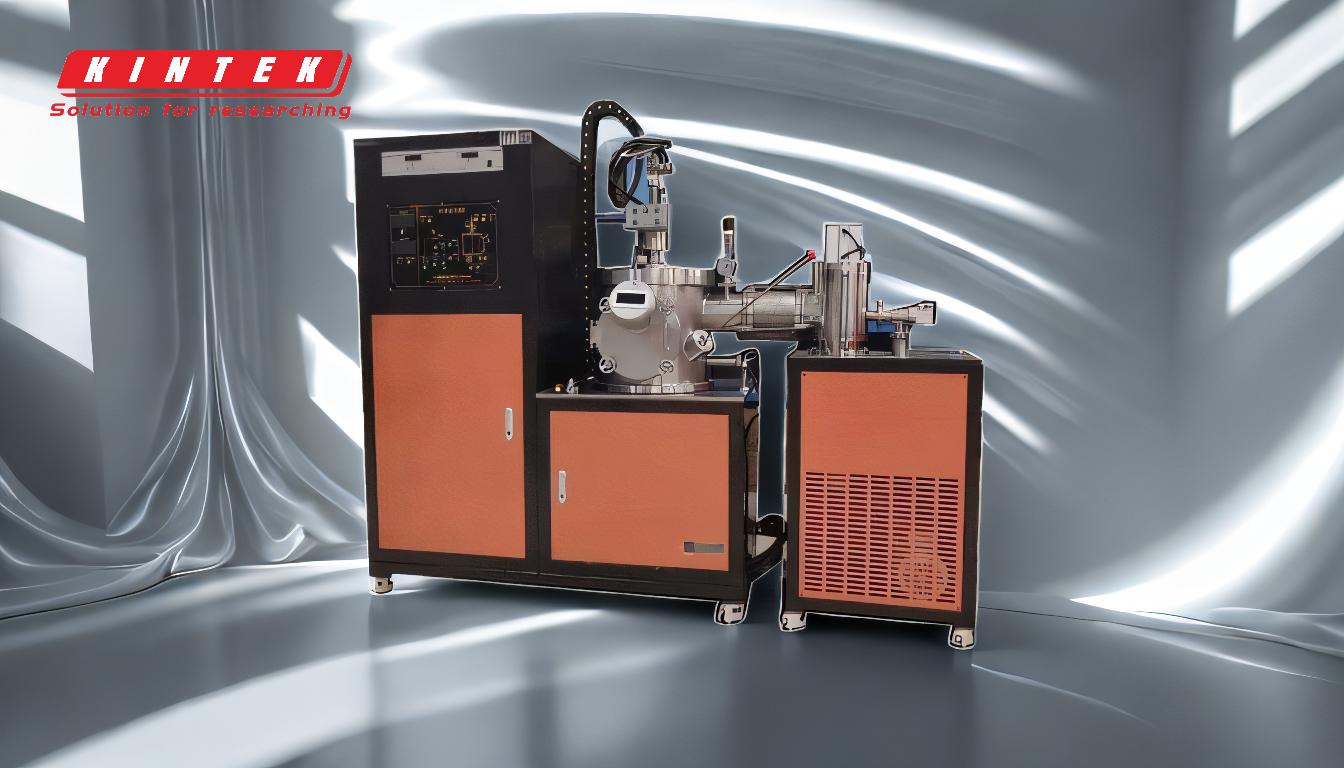
-
Basic Principle of Magnetron Sputtering:
- Magnetron sputtering relies on the bombardment of a target material with high-energy ions, typically from an inert gas like argon.
- The target material is negatively charged, attracting positively charged ions from the plasma.
- When these ions collide with the target, they transfer kinetic energy, causing atoms to be ejected from the target surface in a process called sputtering.
-
Role of Magnetic Fields:
- A magnetic field is applied near the target surface to confine electrons in a cycloidal motion.
- This confinement increases the residence time of electrons in the plasma, enhancing collisions with gas atoms and boosting ionization.
- The magnetic field also prevents high-energy ions from damaging the substrate, ensuring a controlled and efficient deposition process.
-
Plasma Generation and Glow Discharge:
- The process occurs in a high-vacuum chamber to minimize contamination and maintain a low-pressure environment.
- A high negative voltage is applied between the cathode (target) and anode, ionizing the inert gas and creating a plasma.
- The plasma emits a glow discharge, consisting of electrons and ions, which are essential for sustaining the sputtering process.
-
Ejection and Deposition of Target Atoms:
- Energetic ions from the plasma strike the target, ejecting atoms in a line-of-sight cosine distribution.
- These ejected atoms travel through the vacuum and condense on the substrate surface, forming a thin film.
- The uniformity and quality of the coating depend on the energy of the sputtered atoms and the conditions within the chamber.
-
Advantages of Magnetron Sputtering:
- High plasma density and ion energy enable the deposition of high-quality, dense coatings.
- The magnetic field enhances deposition rates while minimizing substrate damage.
- The process is versatile and can be used with a wide range of target materials, including metals, alloys, and ceramics.
-
Applications of Magnetron Sputtering:
- Commonly used in the semiconductor industry for depositing thin films on silicon wafers.
- Applied in optical coatings, such as anti-reflective layers on lenses.
- Used in the production of hard coatings for tools and wear-resistant surfaces.
-
Key Components of the System:
- Vacuum Chamber: Maintains a low-pressure environment to facilitate plasma generation and prevent contamination.
- Target Material: The source of atoms to be deposited, typically made of the desired coating material.
- Magnetron: Generates the magnetic field and supplies power to the target.
- Substrate: The surface onto which the sputtered atoms are deposited.
By combining electric and magnetic fields, magnetron sputtering achieves a highly efficient and controlled deposition process, making it a cornerstone of modern thin-film technology.
Summary Table:
Key Aspect | Description |
---|---|
Basic Principle | Bombardment of a target material with high-energy ions to eject atoms. |
Role of Magnetic Fields | Confines electrons, enhances plasma density, and minimizes substrate damage. |
Plasma Generation | High-vacuum chamber with inert gas (e.g., argon) ionized to create plasma. |
Deposition Process | Ejected atoms condense on a substrate, forming a uniform thin film. |
Advantages | High-quality coatings, versatility, and efficient deposition rates. |
Applications | Semiconductors, optical coatings, and wear-resistant surfaces. |
Key Components | Vacuum chamber, target material, magnetron, and substrate. |
Discover how magnetron sputtering can elevate your thin-film applications—contact our experts today!