The best frequency for induction heating depends on several factors, including the material type, size, thickness, and desired heating depth. Intermediate frequency induction heating ranges from 500 Hz to 10,000 Hz, while high-frequency induction heating operates between 100 kHz and 500 kHz. Higher frequencies are suitable for smaller, thinner materials as they provide shallow heating depths, whereas lower frequencies are better for larger, thicker materials, offering deeper heat penetration. The selection of frequency should also consider the workpiece's material properties, process requirements, and cost constraints. Ultimately, the optimal frequency balances heating efficiency, material characteristics, and application-specific needs.
Key Points Explained:
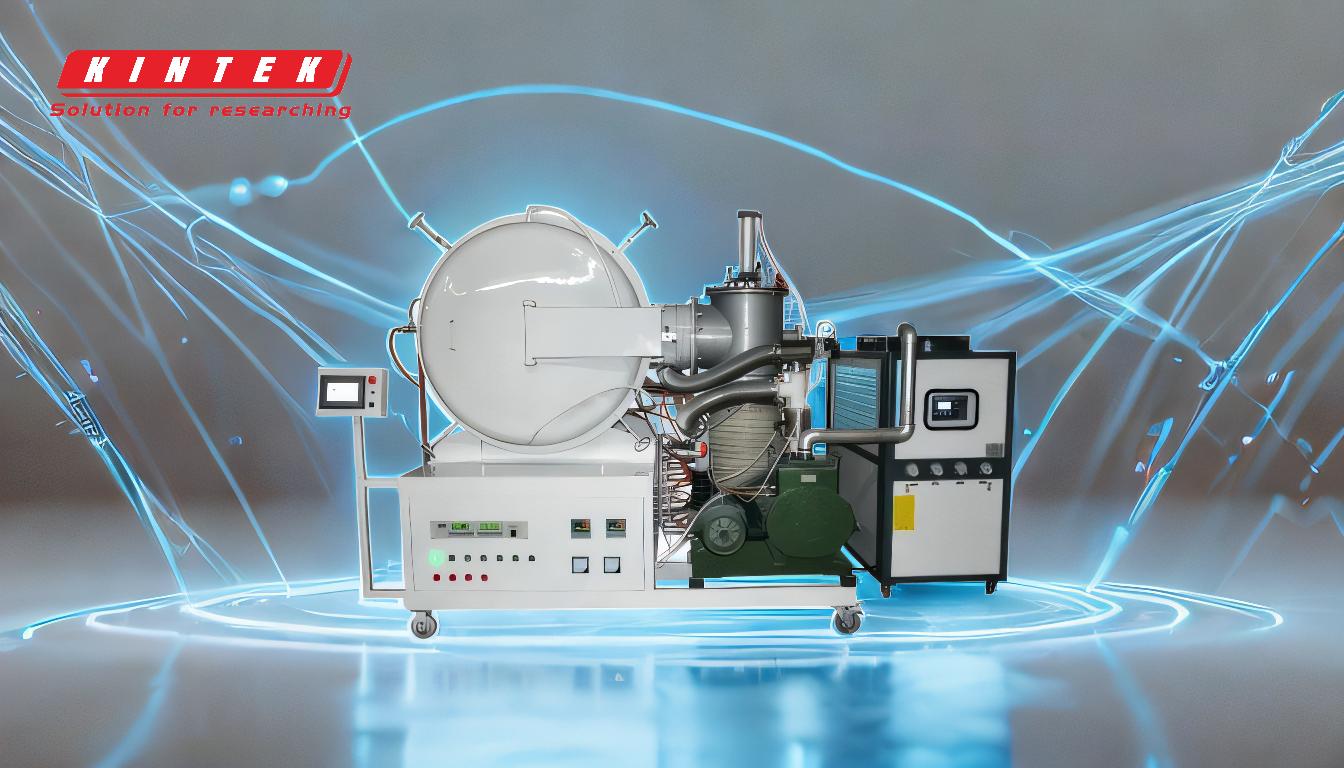
-
Frequency Ranges for Induction Heating:
- Intermediate Frequency: 500 Hz to 10,000 Hz.
- High Frequency: 100 kHz to 500 kHz.
- These ranges are determined by the material's size, thickness, and heating depth requirements.
-
Impact of Frequency on Heating Depth:
- Higher frequencies (e.g., 100 kHz to 500 kHz) result in shallower heating depths, making them ideal for small and thin materials.
- Lower frequencies (e.g., 500 Hz to 10,000 Hz) provide deeper heat penetration, suitable for larger and thicker materials.
-
Material Properties and Frequency Selection:
- Material Type: Metals and conductive materials are typically used in induction heating.
- Resistivity: Materials with higher resistivity heat faster.
- Specific Heat and Mass: These factors influence the power supply capacity required for heating.
-
Workpiece Characteristics:
- Size and Thickness: Smaller and thinner materials heat faster with higher frequencies.
- Desired Heating Depth: The frequency must match the required depth of heat generation in the material.
-
Process Requirements:
- The frequency selection should align with the desired temperature rise, heat loss, and efficiency.
- For example, melting applications may require specific frequencies to achieve the desired stirring effect and melting efficiency.
-
Cost and Practical Considerations:
- The frequency band selection should balance the customer's purchase cost, workpiece material, and process requirements.
- Low-power high-frequency equipment and higher-power ultra-audio equipment may offer similar heating effects for certain workpieces, depending on the application.
-
Design of the Inductor and Power Supply:
- The design of the inductor coil and power supply capacity must account for the material's specific heat, mass, and required temperature rise.
- The frequency of the alternating current in the coil controls the frequency of the current induced in the workpiece, affecting the heating depth.
-
Efficiency of Induction Heating:
- Efficiency depends on the part's characteristics, inductor design, power supply capacity, and the required temperature change.
- Higher induction heating power is often utilized to accommodate a wide range of temperature variations.
-
Customization of Frequency:
- The working frequency of medium-frequency induction melting machines can be adjusted by changing the coil and compensating capacitor based on factors like melting material, quantity, and desired stirring effect.
-
Practical Example:
- For a thin metal sheet requiring surface heating, a high-frequency range (100 kHz to 500 kHz) would be optimal.
- For a thick metal block requiring deep heat penetration, an intermediate frequency range (500 Hz to 10,000 Hz) would be more suitable.
By considering these factors, the best frequency for induction heating can be determined to achieve optimal heating efficiency and meet specific application requirements.
Summary Table:
Factor | Details |
---|---|
Frequency Ranges | Intermediate: 500 Hz to 10,000 Hz; High: 100 kHz to 500 kHz |
Heating Depth | Higher frequencies = shallow depth; Lower frequencies = deeper penetration |
Material Properties | Metals, resistivity, specific heat, and mass influence frequency selection |
Workpiece Characteristics | Size, thickness, and desired heating depth determine optimal frequency |
Process Requirements | Align frequency with temperature rise, heat loss, and efficiency needs |
Cost Considerations | Balance frequency selection with cost and application-specific requirements |
Need help selecting the right frequency for your induction heating process? Contact our experts today for tailored solutions!