When selecting the best material for a crucible, the choice depends on the specific application, including the type of material being melted, the operating temperature, and the required chemical and thermal properties. Common materials include fused quartz, silicon carbide, boron nitride, graphite, and platinum, each offering unique advantages such as thermal shock resistance, durability, thermal insulation, and chemical inertness. The decision should also consider operational factors like furnace type, melting temperatures, and contamination risks. Ultimately, the best crucible material is one that aligns with the specific requirements of the process, ensuring efficiency, durability, and minimal contamination.
Key Points Explained:
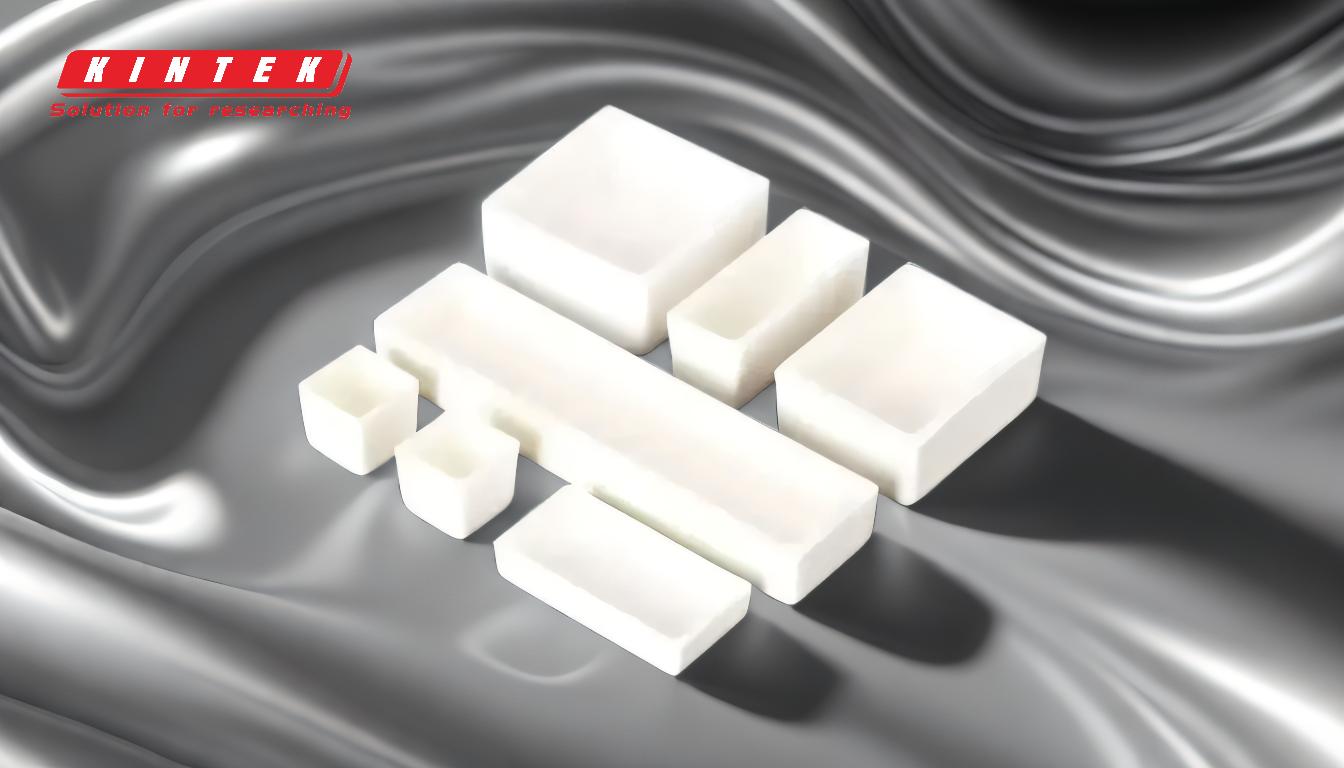
-
Material Selection Based on Application:
- The type of material being melted or processed is the primary factor in choosing a crucible material. For example:
- Fused Quartz: Ideal for melting metals due to its resistance to thermal shock.
- Silicon Carbide: Used in semiconductor production for its durability and high-temperature strength.
- Boron Nitride: Suitable for high-temperature vacuum furnaces due to its excellent thermal insulation properties.
- Graphite: Offers thermal stability, corrosion resistance, and energy efficiency, making it suitable for a wide range of applications.
- Platinum or Zirconium: Used in laboratory settings to prevent contamination of sensitive analytes.
- The type of material being melted or processed is the primary factor in choosing a crucible material. For example:
-
Thermal and Chemical Properties:
- A crucible must withstand extreme temperatures and resist chemical reactions with the melt. Key properties to consider include:
- High Melting Point: The crucible material must have a melting point significantly higher than the material being processed.
- Thermal Shock Resistance: Important for processes involving rapid temperature changes.
- Chemical Stability: The material should not react with the melt, ensuring purity and preventing contamination.
- A crucible must withstand extreme temperatures and resist chemical reactions with the melt. Key properties to consider include:
-
Operational Considerations:
- Beyond material properties, operational factors play a crucial role in selecting a crucible:
- Furnace Compatibility: The crucible must fit the furnace's capacity, dimensions, and type.
- Temperature Requirements: The material should handle both melting and holding temperatures.
- Process-Specific Needs: Consideration of fluxes, degassing, slag removal, and alloy cross-contamination risks.
- Beyond material properties, operational factors play a crucial role in selecting a crucible:
-
Advantages of Common Crucible Materials:
-
Graphite Crucibles:
- Excellent thermal conductivity and stability.
- Resistant to acids, alkalis, and corrosion.
- Reduces melting time and energy consumption.
-
Platinum Crucibles:
- Inert and non-reactive, ideal for analytical chemistry.
- Ensures sample purity and accurate results.
-
Silicon Carbide Crucibles:
- High strength and durability at extreme temperatures.
- Suitable for demanding industrial applications.
-
Graphite Crucibles:
-
Historical and Modern Materials:
- Historically, clay was commonly used for crucibles due to its availability and high-temperature resistance.
- Modern materials like graphite, silicon carbide, and advanced ceramics offer superior performance and are tailored to specific industrial and laboratory needs.
-
Customization for Specific Processes:
- The choice of crucible material should be tailored to the specific process requirements, such as:
- Melting Alloys: Compatibility with the alloy type and melting temperature.
- Contamination Prevention: Use of inert materials like platinum for sensitive applications.
- Energy Efficiency: Materials like graphite that reduce melting time and energy usage.
- The choice of crucible material should be tailored to the specific process requirements, such as:
In conclusion, the best crucible material depends on the specific application, balancing thermal and chemical properties with operational requirements. Whether for industrial metal melting, semiconductor production, or laboratory analysis, selecting the right crucible material ensures efficiency, durability, and high-quality results.
Summary Table:
Material | Key Properties | Applications |
---|---|---|
Fused Quartz | Thermal shock resistance, durability | Melting metals |
Silicon Carbide | High-temperature strength, durability | Semiconductor production |
Boron Nitride | Thermal insulation, chemical inertness | High-temperature vacuum furnaces |
Graphite | Thermal stability, corrosion resistance, energy efficiency | Wide range of industrial applications |
Platinum | Chemical inertness, contamination prevention | Laboratory analysis, sensitive applications |
Need help choosing the right crucible material for your application? Contact our experts today for personalized advice!