Joining stainless steel effectively requires careful consideration of the method used, as stainless steel has unique properties such as high corrosion resistance and thermal sensitivity. The best way to join stainless steel depends on the specific application, desired strength, and aesthetic requirements. Common methods include welding, brazing, and mechanical fastening. Each method has its advantages and limitations, and the choice often depends on factors like material thickness, joint design, and environmental conditions. Below, we explore the key methods and provide detailed insights into their application.
Key Points Explained:
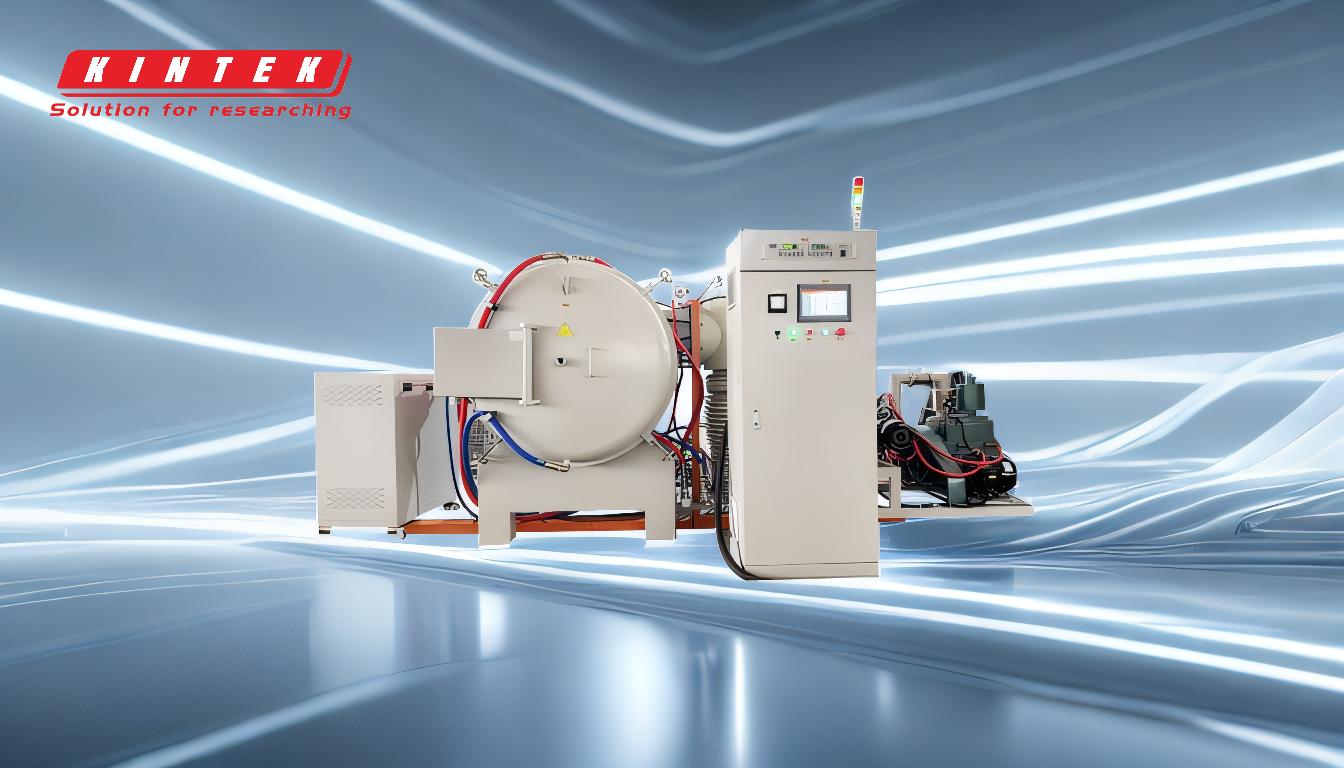
-
Welding Stainless Steel
- Welding is one of the most common methods for joining stainless steel, offering strong and durable joints.
- Key techniques include TIG (Tungsten Inert Gas) welding, MIG (Metal Inert Gas) welding, and spot welding.
- TIG Welding: Ideal for thin stainless steel sheets, providing precise control and clean welds.
- MIG Welding: Suitable for thicker materials and faster production, though it may require post-weld cleaning to remove spatter.
- Spot Welding: Used for joining overlapping sheets, commonly in automotive and appliance manufacturing.
- Heat Management: Stainless steel is sensitive to heat, so it's crucial to use low current settings and short welds (around 25 mm) to prevent overheating and warping.
- Stress Reduction: Techniques like grinding welds and using a ball peen hammer immediately after welding can help reduce residual stresses and improve joint integrity.
-
Brazing Stainless Steel
- Brazing is a lower-temperature joining method that uses a filler metal to bond stainless steel parts.
- Suitable for applications where welding might cause distortion or damage to the material.
- Heating Methods: Brazing can be performed using flame, induction, or furnace heating.
- Filler Materials: Silver-based or nickel-based filler metals are commonly used, depending on the application's corrosion resistance and strength requirements.
- Advantages: Brazing produces clean joints with minimal distortion and is ideal for complex or delicate assemblies.
-
Mechanical Fastening
- Mechanical fastening methods, such as screws, bolts, and rivets, are used when disassembly or non-permanent joints are required.
- Advantages: No heat is applied, preserving the material's properties and avoiding thermal distortion.
- Limitations: May not provide the same strength or leak-proof qualities as welding or brazing.
-
Adhesive Bonding
- Adhesives can be used to join stainless steel in applications where aesthetics and stress distribution are critical.
- Advantages: Provides uniform stress distribution and eliminates the need for heat.
- Limitations: Adhesive strength may be affected by environmental factors like temperature and humidity.
-
Selection Criteria for Joining Methods
- Material Thickness: Thin sheets are better suited for TIG welding or brazing, while thicker materials may require MIG welding.
- Joint Design: The complexity of the joint can influence the choice of method.
- Environmental Conditions: Corrosive environments may favor brazing or welding with corrosion-resistant filler metals.
- Aesthetic Requirements: Methods like TIG welding or brazing provide cleaner, more visually appealing joints.
-
Post-Joining Considerations
- Cleaning: Stainless steel joints should be cleaned to remove oxides, spatter, or residues that could compromise corrosion resistance.
- Passivation: A chemical treatment process that enhances the corrosion resistance of stainless steel after joining.
- Inspection: Ensure joints are free from defects like cracks, porosity, or incomplete fusion.
By carefully selecting the appropriate joining method and following best practices, stainless steel can be effectively joined to meet the desired performance and aesthetic standards. Each method has its unique advantages, and the choice depends on the specific requirements of the application.
Summary Table:
Method | Best For | Advantages | Limitations |
---|---|---|---|
Welding | Strong, durable joints; thin to thick materials | High strength, precise control (TIG), fast production (MIG) | Heat sensitivity, potential warping, post-weld cleaning required |
Brazing | Lower-temperature applications; delicate or complex assemblies | Minimal distortion, clean joints, no heat damage | Limited to specific filler metals, lower strength compared to welding |
Mechanical Fastening | Non-permanent joints; disassembly required | No heat applied, preserves material properties | Lower strength, not leak-proof |
Adhesive Bonding | Aesthetic joints; uniform stress distribution | No heat, uniform stress distribution | Affected by environmental factors like temperature and humidity |
Need help choosing the right method for your stainless steel project? Contact our experts today for personalized advice!