Arc formation is a complex phenomenon primarily caused by the ionization of air or gas between two conductive electrodes, leading to the creation of a plasma channel that allows electric current to flow. This process is influenced by factors such as voltage, electrode material, gap distance, and environmental conditions. The breakdown of the insulating medium (e.g., air) occurs when the electric field strength exceeds its dielectric strength, resulting in the formation of an arc. Arcs are commonly observed in electrical discharges, welding, and circuit breakers, and understanding their causes is critical for designing safe and efficient electrical systems.
Key Points Explained:
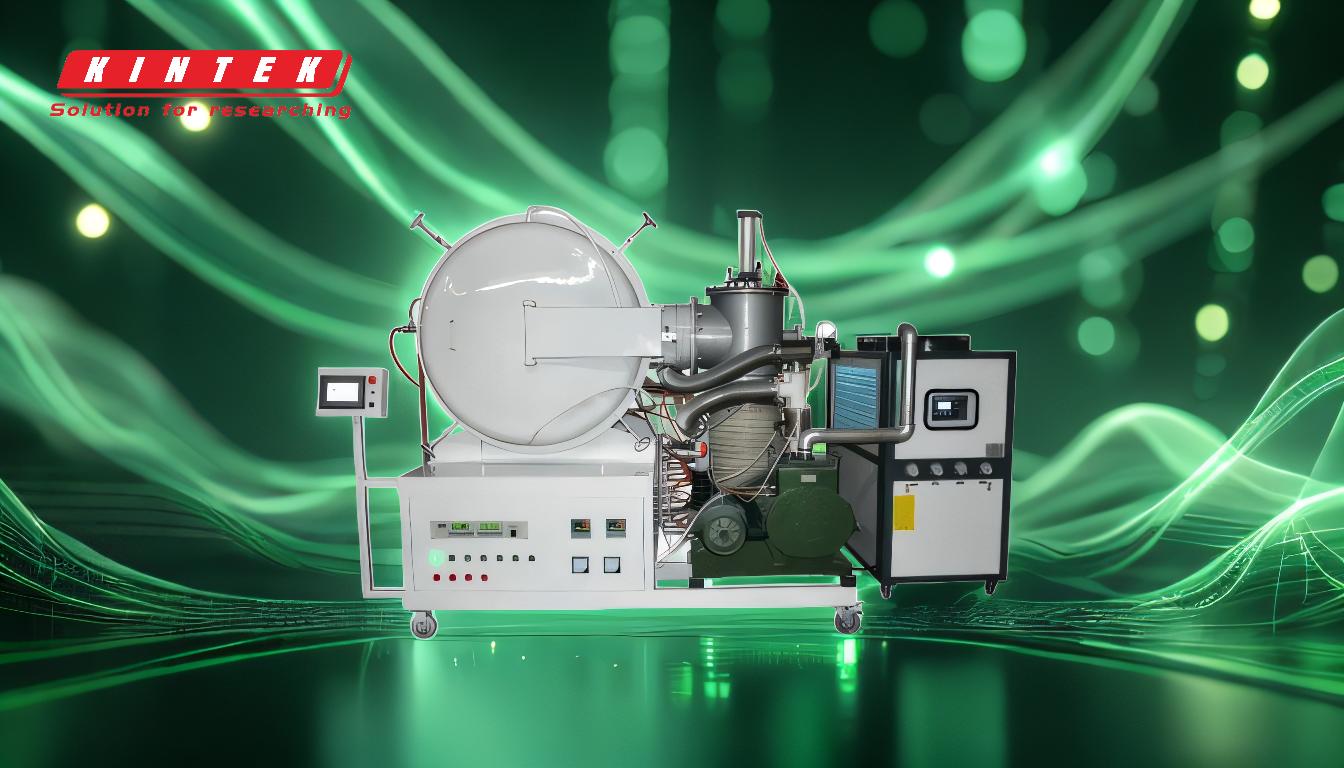
-
Ionization of the Medium:
- Explanation: Arc formation begins with the ionization of the medium (e.g., air, gas, or vacuum) between two electrodes. When a high voltage is applied, the electric field strength increases, causing electrons to be stripped from atoms or molecules in the medium. This creates a plasma of charged particles (ions and free electrons) that can conduct electricity.
- Relevance: Ionization is the fundamental process that enables the arc to form. Without ionization, the medium remains insulating, and no current flows.
-
Breakdown of Dielectric Strength:
- Explanation: Every insulating medium has a dielectric strength, which is the maximum electric field it can withstand before breaking down. When the applied voltage exceeds this threshold, the medium loses its insulating properties, and an arc forms.
- Relevance: The breakdown of dielectric strength is a critical factor in arc formation. It explains why arcs occur at specific voltage levels and gap distances.
-
Electrode Material and Surface Conditions:
- Explanation: The material and surface conditions of the electrodes play a significant role in arc formation. Rough surfaces or contaminants can create localized high electric fields, promoting ionization. Additionally, certain materials (e.g., tungsten) are more prone to emitting electrons, which facilitates arc initiation.
- Relevance: Electrode properties directly influence the ease of arc formation and its stability. This is particularly important in applications like welding, where electrode selection is crucial.
-
Gap Distance and Voltage:
- Explanation: The distance between the electrodes (gap) and the applied voltage determine the electric field strength. A larger gap requires a higher voltage to achieve the same field strength. Paschen's Law describes the relationship between voltage, gap distance, and pressure for breakdown in gases.
- Relevance: Understanding the interplay between gap distance and voltage is essential for predicting and controlling arc formation in electrical systems.
-
Environmental Factors:
- Explanation: Environmental conditions such as temperature, pressure, and humidity affect the dielectric strength of the medium. For example, higher humidity can lower the breakdown voltage of air, making arc formation more likely.
- Relevance: Environmental factors must be considered when designing systems to prevent unintended arcing or to optimize arc performance in controlled applications.
-
Thermal Effects and Plasma Formation:
- Explanation: Once an arc is initiated, the plasma channel heats up due to the flow of current. This thermal energy further ionizes the surrounding medium, sustaining the arc. The high temperature can also cause electrode erosion and material vaporization.
- Relevance: Thermal effects are critical for maintaining the arc and understanding its behavior over time. They also influence the longevity and performance of electrodes.
-
Applications and Implications:
- Explanation: Arcs are utilized in various applications, such as welding, lighting (e.g., arc lamps), and circuit breakers. However, unintended arcing in electrical systems can lead to equipment damage, fires, or safety hazards.
- Relevance: Understanding the causes of arc formation helps in both harnessing its benefits and mitigating its risks.
-
Prevention and Control:
- Explanation: Techniques to prevent or control arcing include using insulating materials, maintaining proper gap distances, and implementing arc suppression circuits. In welding, precise control of the arc is achieved through specialized power supplies and electrode materials.
- Relevance: Effective prevention and control strategies are essential for ensuring the safety and reliability of electrical systems.
By breaking down the causes of arc formation into these key points, we gain a comprehensive understanding of the phenomenon, enabling better design, control, and application of arcs in various fields.
Summary Table:
Key Factor | Explanation | Relevance |
---|---|---|
Ionization of the Medium | High voltage strips electrons, creating a plasma channel for current flow. | Fundamental process enabling arc formation. |
Breakdown of Dielectric Strength | Voltage exceeding the medium's dielectric strength causes insulation failure. | Determines the voltage and gap distance required for arcing. |
Electrode Material and Surface | Rough surfaces or specific materials (e.g., tungsten) facilitate arc initiation. | Influences arc stability and ease of formation, especially in welding. |
Gap Distance and Voltage | Larger gaps require higher voltage to achieve the same electric field strength. | Governed by Paschen's Law; critical for predicting arc formation. |
Environmental Factors | Temperature, pressure, and humidity affect dielectric strength. | Must be considered to prevent unintended arcing or optimize performance. |
Thermal Effects and Plasma | Plasma heats up, sustaining the arc and causing electrode erosion. | Critical for maintaining the arc and understanding its long-term behavior. |
Applications and Implications | Used in welding, lighting, and circuit breakers; unintended arcing poses risks. | Harnessing benefits while mitigating risks in electrical systems. |
Prevention and Control | Techniques include insulating materials, gap maintenance, and suppression circuits. | Essential for ensuring system safety and reliability. |
Need expert guidance on arc formation or electrical system design? Contact us today for tailored solutions!