Chemical vapor deposition (CVD) is a versatile and widely used chemical process for depositing high-purity, high-performance solid materials onto a substrate. This method involves the reaction or decomposition of gas molecules on a heated substrate surface, resulting in the formation of a thin film. CVD is employed across various industries, including electronics, cutting tools, and solar cell manufacturing, due to its ability to produce durable and precise coatings. The process operates under controlled conditions, often involving high temperatures and vacuum environments, to ensure the deposition of uniform and high-quality materials. CVD requires a high level of expertise due to its complexity and the need for precise control over parameters such as temperature, pressure, and gas flow.
Key Points Explained:
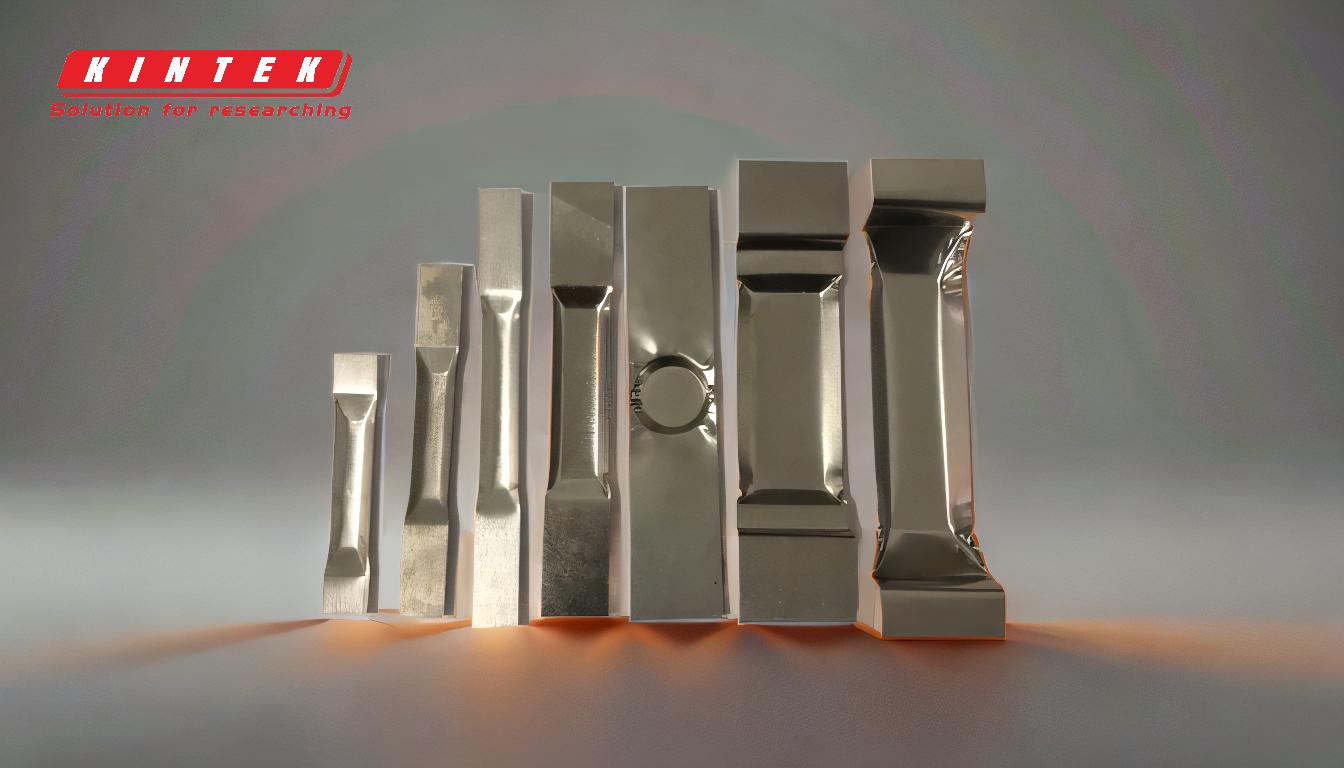
-
Definition and Process of CVD:
- Chemical vapor deposition (CVD) is a chemical process where gas-phase reactants are introduced into a reaction chamber containing a heated substrate.
- The gases react or decompose on the substrate's surface, forming a solid material film.
- This process is highly controlled, often involving vacuum environments and elevated temperatures (typically above 500°C) to ensure precise deposition.
-
Applications of CVD:
- Electronics: CVD is used to deposit thin films on semiconductors, which are essential for manufacturing integrated circuits and other electronic components.
- Cutting Tools: CVD coatings enhance the durability and performance of cutting tools by providing wear and corrosion resistance.
- Solar Cells: CVD is employed in the production of thin-film solar cells, where photovoltaic materials are deposited onto substrates to create efficient energy-harvesting devices.
-
Types of CVD Techniques:
- Thermal CVD: Involves heating a solid source material to produce vapor, which then deposits onto the substrate. This method is effective for creating uniform coatings.
- Aerosol Deposition: Uses high-speed ceramic particles to form dense coatings without requiring additional heat treatment.
- Sputtering: A physical vapor deposition method where high-energy ions bombard a target material, ejecting atoms that deposit onto the substrate.
-
Advantages of CVD:
- High Purity: CVD produces materials with exceptional purity, making it suitable for applications requiring precise material properties.
- Versatility: It can deposit coatings on a wide range of substrates, including glass, metals, and ceramics.
- Durability: CVD coatings are known for their strength and resistance to wear, corrosion, and high temperatures.
-
Challenges and Considerations:
- Complexity: CVD requires specialized equipment and expertise to control parameters such as temperature, pressure, and gas flow.
- Cost: The process can be expensive due to the need for high-purity gases and sophisticated equipment.
- Scalability: While CVD is highly effective for small-scale applications, scaling up for mass production can be challenging.
-
Comparison with Other Deposition Methods:
- Thermal Vapor Deposition: Similar to CVD but relies solely on thermal energy to vaporize the source material.
- Aerosol Deposition: Focuses on kinetic energy for particle deposition, eliminating the need for high temperatures.
- Sputtering: A physical process that does not involve chemical reactions, making it suitable for depositing metals and alloys.
In summary, chemical vapor deposition is a critical technology for creating high-performance coatings and thin films across various industries. Its ability to produce durable, precise, and high-purity materials makes it indispensable in fields such as electronics, manufacturing, and renewable energy. However, the complexity and cost of the process necessitate careful consideration and expertise for successful implementation.
Summary Table:
Aspect | Details |
---|---|
Definition | A chemical process depositing solid materials via gas reactions on a heated substrate. |
Applications | Electronics, cutting tools, solar cells. |
Techniques | Thermal CVD, aerosol deposition, sputtering. |
Advantages | High purity, versatility, durability. |
Challenges | Complexity, cost, scalability. |
Comparison | Thermal vapor deposition, aerosol deposition, sputtering. |
Discover how CVD can elevate your material coatings—contact our experts today!