Cold isostatic pressing (CIP) is a manufacturing process used to compact powdered materials into a solid form by applying uniform pressure from all directions using a liquid medium, typically an oil-water mixture. This method is particularly beneficial for producing large or complex-shaped components that require uniform density and strength in all directions. CIP is widely used across various industries, including aerospace, automotive, oil and gas, medical devices, and energy storage technologies, to produce items like refractory nozzles, ceramic insulators, metal filters, and preforms. The process is also valued for its ability to improve mechanical properties, corrosion resistance, and suitability for powder metallurgy and sintering preparations.
Key Points Explained:
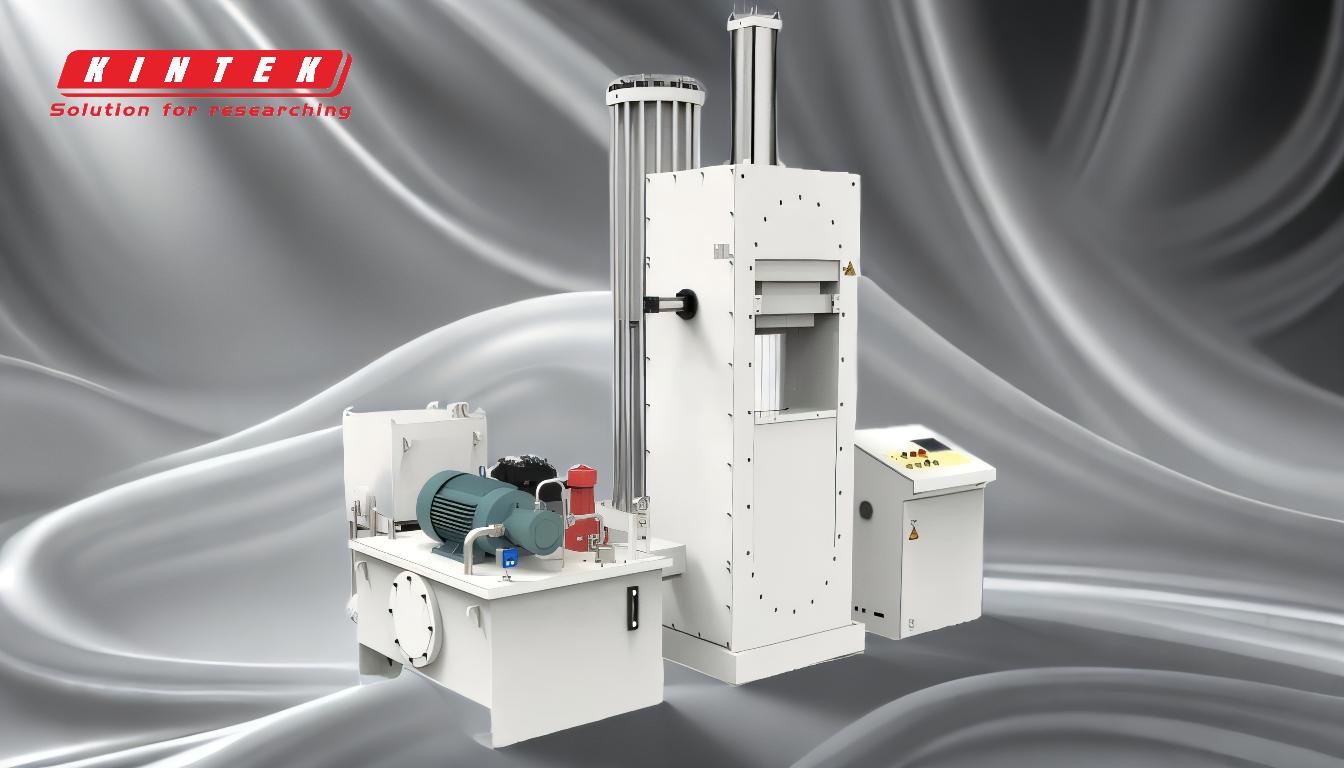
-
Definition and Process of Cold Isostatic Pressing (CIP):
- Cold isostatic pressing involves placing powdered material into a flexible mold, which is then subjected to high pressure from all directions using a liquid medium. This uniform pressure ensures that the final product has consistent density and strength throughout.
- The pressure in a CIP chamber can reach up to 100,000 psi, making it suitable for compacting a wide range of materials, including ceramics, metals, composites, and plastics.
-
Applications of CIP:
- CIP is used to produce a variety of components, such as refractory nozzles, blocks, crucibles, cemented carbides, isotropic graphite, ceramic insulators, tubes for special chemical applications, ferrites, metal filters, preforms, and plastic tubes and rods.
- It is also employed in the manufacturing of advanced ceramics for aerospace and automotive industries, high-performance components for the oil and gas industry, medical devices, and electrical connectors. Additionally, CIP is applied in energy storage technologies, including lithium-ion batteries and fuel cells.
-
Advantages of CIP:
- Uniform Density and Strength: The all-around pressure ensures that the product has uniform density and strength in all directions, which is crucial for components that require high reliability and performance.
- Shape Flexibility: CIP allows for the production of complex shapes that would be difficult or impossible to achieve with uniaxial pressing methods.
- Improved Mechanical Properties: The process enhances the mechanical properties of the materials, making them more suitable for demanding applications.
- Corrosion Resistance: CIP can improve the corrosion resistance of materials, which is particularly important for components used in harsh environments.
- Versatility: CIP can be used with a wide range of materials, including ceramics, metals, composites, and plastics, making it a versatile manufacturing process.
-
Industrial and Research Applications:
- CIP is widely used in industries that require high-performance materials, such as aerospace, automotive, oil and gas, and medical devices. It is also crucial in the production of energy storage technologies.
- In research and development, laboratory or developmental CIP services may perform process parameter studies or produce powder samples for further analysis and testing.
-
Comparison with Other Pressing Methods:
- Unlike uniaxial pressing, which applies pressure in a single direction, CIP applies pressure uniformly from all directions. This results in a more homogeneous product with fewer defects.
- CIP is particularly useful for parts that are too large or complex for uniaxial presses and for materials that do not require high precision in the sintered state.
-
Future Trends and Innovations:
- As industries continue to demand materials with higher performance and reliability, the use of CIP is expected to grow. Innovations in mold design, pressure control, and material science are likely to further enhance the capabilities of CIP.
In summary, cold isostatic pressing is a versatile and effective method for producing high-quality components with uniform density and strength. Its applications span a wide range of industries, and its advantages make it a preferred choice for many manufacturing processes. For more detailed information on the equipment used in this process, you can refer to the topic on isostatic press.
Summary Table:
Aspect | Details |
---|---|
Process | Applies uniform pressure from all directions using a liquid medium. |
Pressure Range | Up to 100,000 psi. |
Applications | Aerospace, automotive, oil & gas, medical devices, energy storage. |
Key Advantages | Uniform density, shape flexibility, improved mechanical properties. |
Materials Used | Ceramics, metals, composites, plastics. |
Future Trends | Innovations in mold design, pressure control, and material science. |
Interested in how cold isostatic pressing can benefit your industry? Contact us today to learn more!