Fused quartz is a high-purity form of silicon dioxide with exceptional mechanical, thermal, and optical properties. While the provided references highlight its thermal resistance, chemical purity, and optical clarity, they do not explicitly mention its compressive strength. However, based on general material science knowledge, fused quartz is known for its extreme rigidity and hardness, which contribute to its high compressive strength. This makes it suitable for applications requiring durability under pressure, such as precision optics, high-temperature environments, and protective components. Below, we explore the key aspects of fused quartz's properties and their relevance to compressive strength.
Key Points Explained:
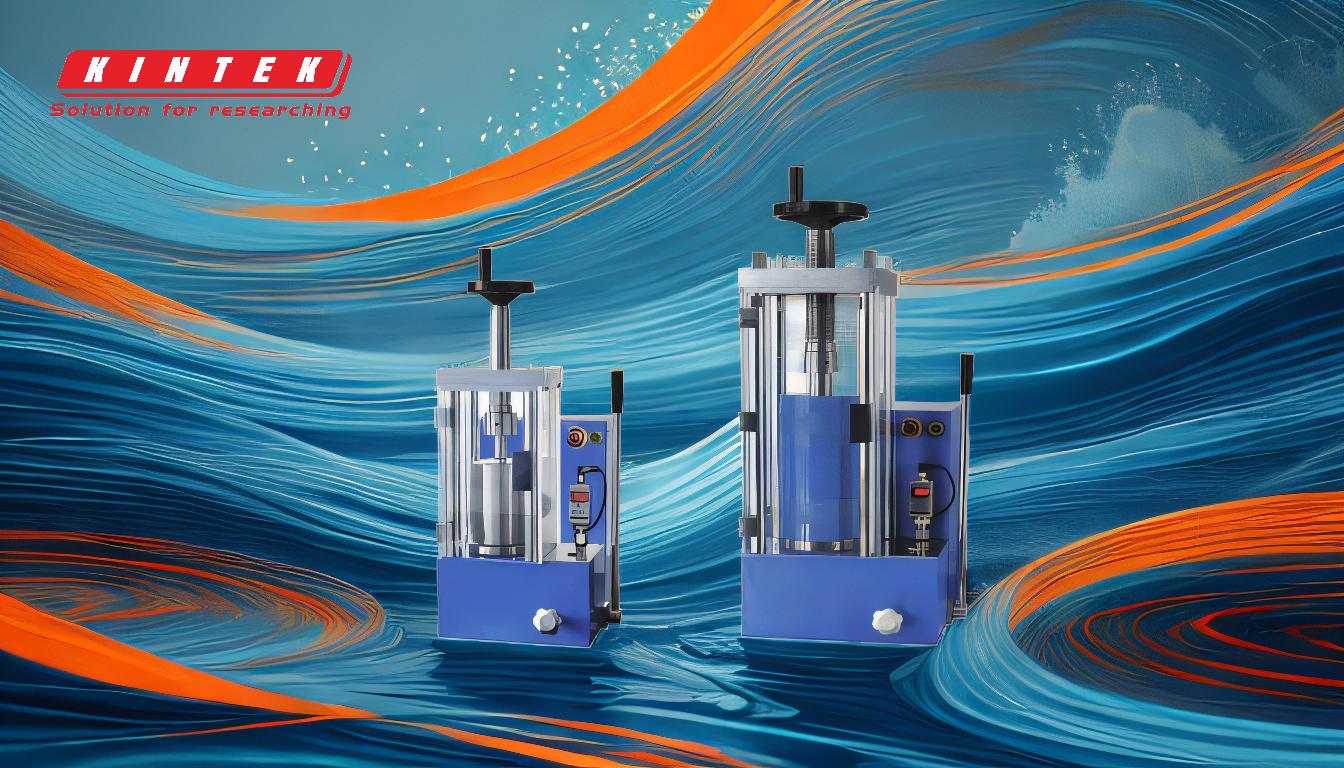
-
Definition and Composition of Fused Quartz
- Fused quartz is a synthetic material made by melting high-purity silicon dioxide (SiO₂) at extremely high temperatures.
- It is distinct from natural quartz due to its lack of impurities and crystalline structure, resulting in superior mechanical and thermal properties.
-
General Mechanical Properties
- Fused quartz is known for its extreme rigidity and high hardness, which are indicators of its ability to withstand compressive forces.
- While the exact compressive strength is not provided in the references, fused quartz typically exhibits a compressive strength in the range of 1,100 to 1,400 MPa (megapascals), depending on its purity and manufacturing process.
-
Factors Influencing Compressive Strength
- Purity: High-purity fused quartz has fewer defects, enhancing its structural integrity and compressive strength.
- Thermal Resistance: Its ability to withstand high temperatures without degrading contributes to maintaining strength under extreme conditions.
- Low Thermal Expansion: The low coefficient of thermal expansion minimizes stress under temperature fluctuations, preserving compressive strength.
-
Applications Demonstrating Compressive Strength
- Precision Optics: Fused quartz is used in lenses and mirrors due to its ability to maintain shape and clarity under pressure.
- High-Temperature Environments: Its use in thermocouple protection tubes and high-temperature lamps highlights its durability under mechanical and thermal stress.
- Protective Components: Its rigidity and resistance to deformation make it ideal for protective applications in harsh environments.
-
Comparison with Other Materials
- Compared to ordinary glass, fused quartz has significantly higher compressive strength due to its purity and lack of crystalline boundaries.
- It outperforms many metals and ceramics in terms of rigidity and resistance to deformation under pressure.
-
Testing and Standards
- Compressive strength is typically measured using standardized tests, such as ASTM C1424 for advanced ceramics, which can also be applied to fused quartz.
- These tests involve applying a uniaxial load until the material fractures, providing a quantitative measure of its compressive strength.
-
Practical Considerations for Equipment Purchasers
- When selecting fused quartz for applications requiring high compressive strength, ensure the material meets the required purity and thermal resistance standards.
- Consider the specific environmental conditions (e.g., temperature, pressure, and chemical exposure) to ensure optimal performance.
In summary, while the provided references do not explicitly state the compressive strength of fused quartz, its extreme rigidity, hardness, and resistance to deformation suggest a high compressive strength, typically in the range of 1,100 to 1,400 MPa. This makes it an excellent choice for applications requiring durability under pressure, such as precision optics, high-temperature environments, and protective components. Equipment purchasers should prioritize high-purity fused quartz and verify its compliance with relevant standards for their specific application needs.
Summary Table:
Property | Details |
---|---|
Compressive Strength | 1,100–1,400 MPa |
Key Properties | Extreme rigidity, high hardness, thermal resistance, low thermal expansion |
Applications | Precision optics, high-temperature environments, protective components |
Testing Standards | ASTM C1424 for advanced ceramics |
Practical Considerations | Ensure high purity and compliance with application-specific standards |
Need high-purity fused quartz for your application? Contact us today to find the perfect solution!