The controlled atmosphere brazing (CAB) process is a specialized joining technique used to create strong, reliable bonds between metal parts without oxidation or contamination. It involves heating the parts and a filler material in a controlled environment, typically filled with inert or reducing gases, to prevent oxidation and ensure a clean joint. The filler material melts and flows into the gaps between the parts through capillary action, creating a durable bond. This process is widely used in industries requiring high precision and quality, such as aerospace, automotive, and electronics. CAB offers advantages like minimal distortion, clean joints, and the ability to join dissimilar materials, but it requires careful control of parameters like temperature, atmosphere composition, and filler material selection.
Key Points Explained:
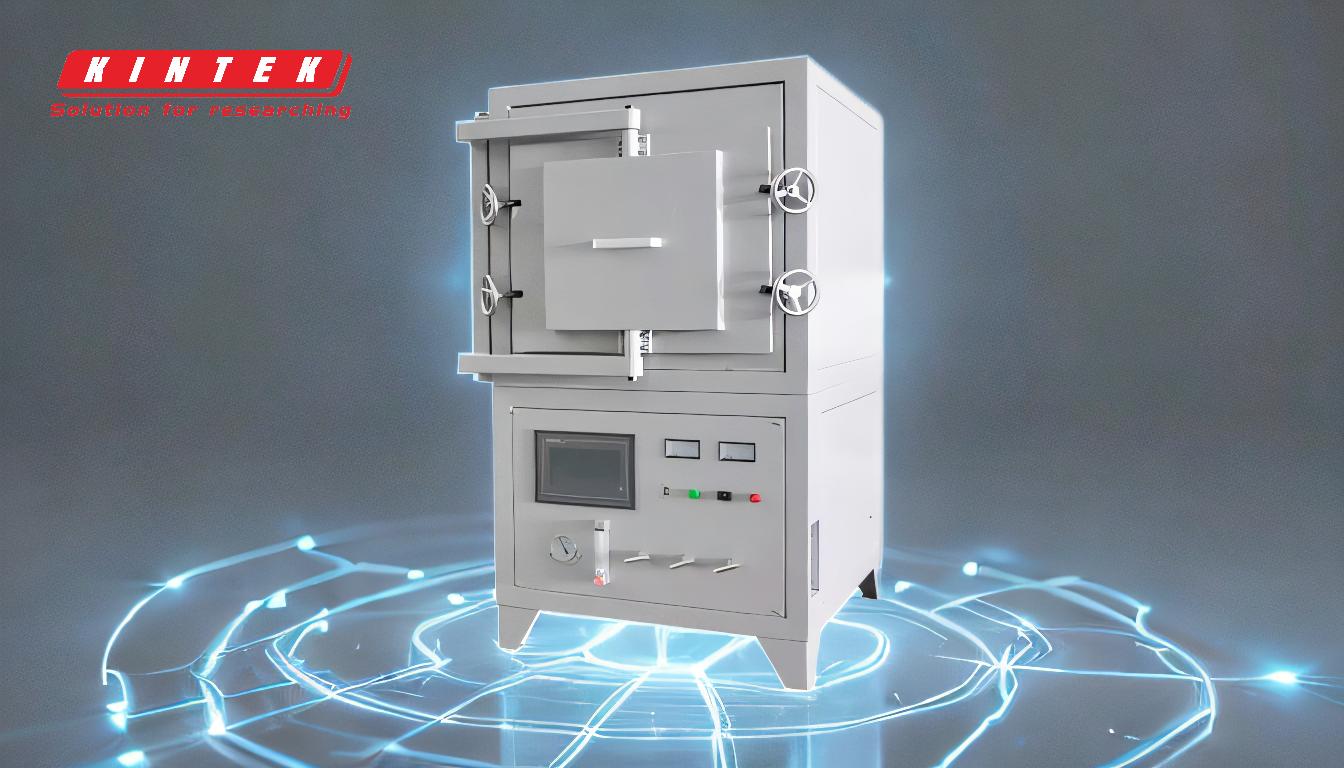
-
Definition of Controlled Atmosphere Brazing (CAB):
- CAB is a brazing process conducted in a controlled environment, typically using inert or reducing gases like nitrogen, hydrogen, or argon. This atmosphere prevents oxidation and contamination of the parts and filler material during heating, ensuring a clean and strong joint.
-
How CAB Works:
- The process involves heating the parts and filler material to a temperature above the filler's melting point but below the base materials' melting points. The filler material melts and flows into the gaps between the parts via capillary action, forming a strong bond upon cooling.
-
Key Components of CAB:
- Filler Material: Must have a lower melting point than the base materials and be compatible with them. Common fillers include silver, copper, and nickel-based alloys.
- Controlled Atmosphere: Inert or reducing gases are used to prevent oxidation and contamination, ensuring a clean joint.
- Heating Method: Typically performed in specialized furnaces that can maintain precise temperature and atmosphere control.
-
Advantages of CAB:
- Oxidation Prevention: The controlled atmosphere eliminates oxidation, resulting in clean, high-quality joints.
- Minimal Distortion: The process avoids excessive heating, reducing thermal stress and distortion in the parts.
- Versatility: Suitable for joining dissimilar materials and complex geometries.
- Strong Joints: Produces durable, leak-tight joints with excellent mechanical properties.
-
Challenges in CAB:
- Filler Material Selection: Choosing the right filler material based on the required bonding strength, conductivity, and compatibility with base materials.
- Atmosphere Control: Requires precise control of gas composition and flow rates to maintain a clean environment.
- Temperature and Time: Accurate calculation of heating time and temperature is critical to avoid defects like incomplete bonding or overheating.
- Technical Expertise: Operators need specialized knowledge of furnace operation and gas handling.
-
Applications of CAB:
- Aerospace: Used for joining critical components like heat exchangers and turbine blades.
- Automotive: Common in manufacturing radiators, air conditioning systems, and fuel systems.
- Electronics: Ideal for creating precise, reliable joints in circuit boards and sensors.
- Medical Devices: Ensures clean, strong joints in surgical instruments and implants.
-
Comparison with Other Brazing Methods:
- Vacuum Brazing: Similar to CAB but performed in a vacuum environment. While vacuum brazing eliminates oxidation entirely, it is more expensive and less suitable for high-volume production.
- Flame Brazing: Uses a torch to heat the parts, but the open flame can cause oxidation and contamination, making it less suitable for high-precision applications.
-
Future Trends in CAB:
- Automation: Increasing use of automated systems for precise control of temperature, atmosphere, and filler material application.
- Advanced Materials: Development of new filler materials and coatings to improve joint strength and compatibility with advanced alloys.
- Sustainability: Efforts to reduce energy consumption and gas usage in the process to make it more environmentally friendly.
By understanding these key points, equipment and consumable purchasers can make informed decisions about implementing CAB in their manufacturing processes, ensuring high-quality, reliable joints for their products.
Summary Table:
Aspect | Details |
---|---|
Definition | A brazing process in a controlled environment to prevent oxidation. |
Key Components | Filler material, controlled atmosphere, and precise heating methods. |
Advantages | Clean joints, minimal distortion, and compatibility with dissimilar metals. |
Challenges | Requires precise control of temperature, atmosphere, and filler selection. |
Applications | Aerospace, automotive, electronics, and medical devices. |
Future Trends | Automation, advanced materials, and sustainability improvements. |
Discover how controlled atmosphere brazing can enhance your manufacturing process—contact our experts today!