The cooling rate of a muffle furnace depends on the temperature range and the cooling method employed. Below 500°C, a fast cooling device can increase the cooling rate to 10-12 K/min, maintaining effectiveness (>2 K/min) even at 200°C. Above 500°C, natural cooling is recommended to avoid damaging the furnace. Factors such as furnace size, construction materials, and operational conditions also influence cooling rates. Proper cooling practices, like avoiding immediate door opening and maintaining environmental conditions, ensure safety and prolong the furnace's lifespan.
Key Points Explained:
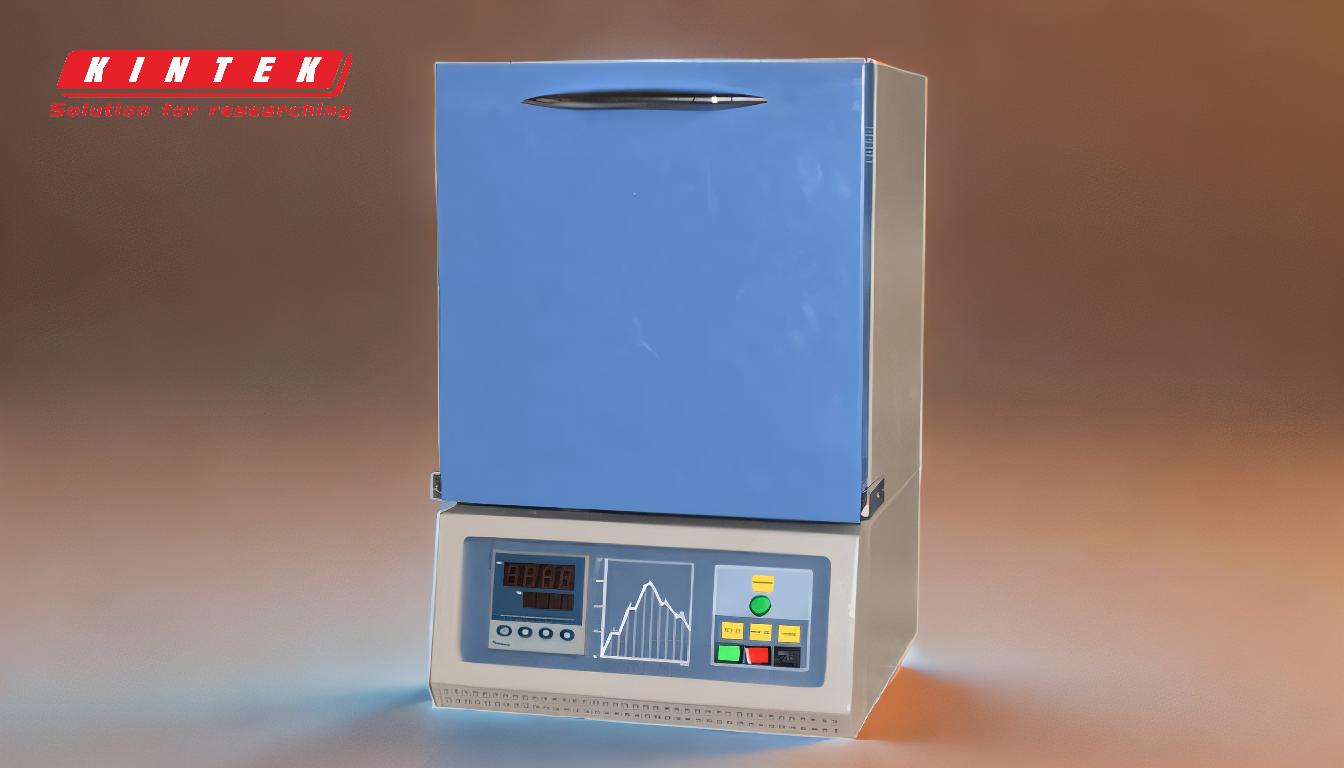
-
Cooling Rate Below 500°C:
- A fast cooling device can be used below 500°C to achieve a cooling rate of 10-12 K/min.
- This method remains effective (>2 K/min) even at 200°C.
- Fast cooling is designed to protect the inner muffle from damage by avoiding rapid temperature changes at higher temperatures.
-
Natural Cooling Above 500°C:
- Above 500°C, natural cooling is recommended to prevent thermal shock and damage to the furnace.
- The power should be cut off, and the furnace allowed to cool naturally.
- Opening the furnace door immediately after use is discouraged to avoid safety hazards.
-
Factors Influencing Cooling Rate:
- Furnace Size and Construction: Larger furnaces or those made with specific materials may cool at different rates.
- Operational Conditions: Environmental factors like humidity, dust, and gas presence can affect cooling.
- Load Condition: The amount and type of material inside the furnace can influence the cooling process.
-
Safety and Longevity Considerations:
- Operating the furnace 50°C below its maximum temperature ensures a longer lifespan for the heating elements.
- Proper environmental conditions (e.g., humidity below 85%, absence of corrosive gases) are crucial for safe operation.
- Sealed containers or appropriate openings should be used when heating materials that release volatile gases to prevent corrosion of heating elements.
-
General Operational Guidelines:
- Muffle furnaces typically operate between 1000°C and 1800°C, making them suitable for high-temperature applications.
- Refractory materials must be used inside the furnace to withstand high temperatures.
- The purpose of use and operational methods should guide the selection of an appropriate muffle furnace.
-
Factors Affecting Heating and Cooling:
- Supply Voltage and Heating Elements: These directly impact the furnace's ability to reach and maintain temperatures.
- Furnace Chamber Size and Structure: Larger chambers may require more time to heat and cool.
- Temperature Controller Precision: Accurate temperature control ensures consistent heating and cooling rates.
- Furnace Sealing and Insulation: Proper sealing and insulation improve efficiency and safety.
- Operational Practices: Frequent door opening or improper use can disrupt heating and cooling processes.
By understanding these key points, users can optimize the cooling process of a muffle furnace, ensuring both safety and efficiency in their operations.
Summary Table:
Temperature Range | Cooling Method | Cooling Rate | Key Considerations |
---|---|---|---|
Below 500°C | Fast Cooling Device | 10-12 K/min | Protects inner muffle, effective even at 200°C (>2 K/min) |
Above 500°C | Natural Cooling | Variable | Prevents thermal shock, avoid immediate door opening |
Factors Influencing Cooling Rate | Details | ||
Furnace Size & Construction | Larger furnaces or specific materials affect cooling rates | ||
Operational Conditions | Humidity, dust, and gas presence impact cooling | ||
Load Condition | Amount and type of material influence cooling | ||
Safety & Longevity | Guidelines | ||
Operating Temperature | Keep 50°C below max temperature for longer lifespan | ||
Environmental Conditions | Maintain humidity below 85%, avoid corrosive gases | ||
Sealed Containers | Use for volatile materials to prevent corrosion |
Need help optimizing your muffle furnace cooling process? Contact our experts today for personalized advice!