The cost of a vacuum brazing furnace can vary significantly depending on its specifications, features, and intended applications. These furnaces are highly specialized equipment designed for precision brazing in industries such as aerospace, particle physics, and metallurgical research. Key factors influencing the cost include temperature uniformity, programmability, compliance with industry standards like NADCAP, and the ability to handle large or complex workpieces. While the exact price can range from tens of thousands to hundreds of thousands of dollars, understanding the specific requirements of your application is crucial to determining the most suitable and cost-effective option.
Key Points Explained:
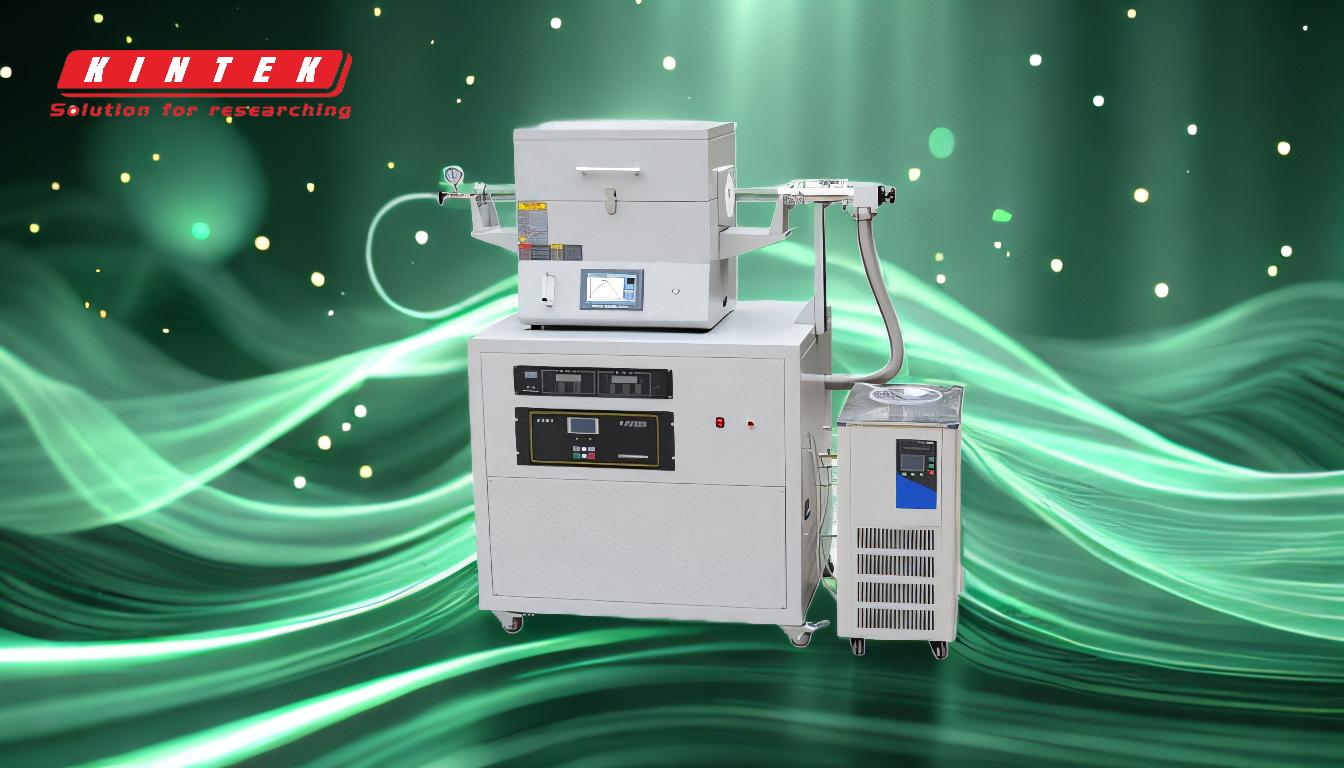
-
Temperature Uniformity and Hot Zone Design:
- A vacuum brazing furnace is designed to maintain high temperature uniformity within its hot zone. This ensures consistent heating cycles for multiple loads or continuous brazing of larger pieces.
- The ability to achieve identical heating cycles is critical for industries like aerospace and metallurgical research, where precision is paramount.
- The cost of the furnace is influenced by the quality of the hot zone design and the materials used to achieve this uniformity.
-
Programmability and Automation:
- Advanced vacuum brazing furnaces often feature barcode-linked cycle programs, enabling the furnace to recognize workpieces and apply precise heating cycles tailored to each piece.
- This level of automation and programmability increases the furnace's cost but also enhances its efficiency and suitability for high-volume or complex production environments.
-
Oxide Layer Removal:
- The furnace operates at temperatures higher than oxide formation, allowing oxidized pieces to lose their oxide layer before brazing. This feature is essential for achieving strong, defect-free brazed joints.
- The ability to handle oxidized materials adds to the complexity and cost of the furnace.
-
Applications and Industry Compliance:
- Vacuum brazing furnaces are designed for demanding applications in aerospace, particle physics, and metallurgical research. These industries require equipment that meets stringent standards, such as NADCAP compliance.
- Compliance with such standards often involves additional testing, documentation, and quality control measures, which contribute to the overall cost.
-
Size and Capacity:
- The size of the furnace and its capacity to handle larger or more complex workpieces can significantly impact the cost. Larger furnaces with higher capacities are generally more expensive due to the increased materials and engineering required.
-
Additional Features:
- Features such as sophisticated cycle programming, advanced cooling systems, and enhanced safety mechanisms can further increase the cost of a vacuum brazing furnace.
- These features are often necessary for specialized applications but may not be required for simpler brazing tasks.
In summary, the cost of a vacuum brazing furnace is influenced by a combination of factors, including temperature uniformity, programmability, compliance with industry standards, size, and additional features. Understanding your specific application requirements will help you determine the most suitable and cost-effective option.
Summary Table:
Factor | Impact on Cost |
---|---|
Temperature Uniformity | High-quality hot zone design increases cost for precision heating. |
Programmability | Advanced automation and cycle programming raise costs but improve efficiency. |
Oxide Layer Removal | Ability to handle oxidized materials adds complexity and cost. |
Industry Compliance | NADCAP and other standards require additional testing, increasing costs. |
Size and Capacity | Larger furnaces with higher capacities are more expensive due to materials used. |
Additional Features | Advanced cooling, safety mechanisms, and programming further increase costs. |
Ready to find the perfect vacuum brazing furnace for your needs? Contact us today for expert guidance!