Annealing and quenching are two fundamental heat treatment processes used to alter the physical and mechanical properties of metals. Annealing involves heating the metal to a specific temperature and then cooling it slowly to increase ductility, reduce hardness, and relieve internal stresses. Quenching, on the other hand, involves rapidly cooling the metal after heating to achieve high hardness and strength, often at the expense of ductility. While annealing aims to soften the material and improve its workability, quenching is designed to harden it, making it more suitable for applications requiring wear resistance and durability.
Key Points Explained:
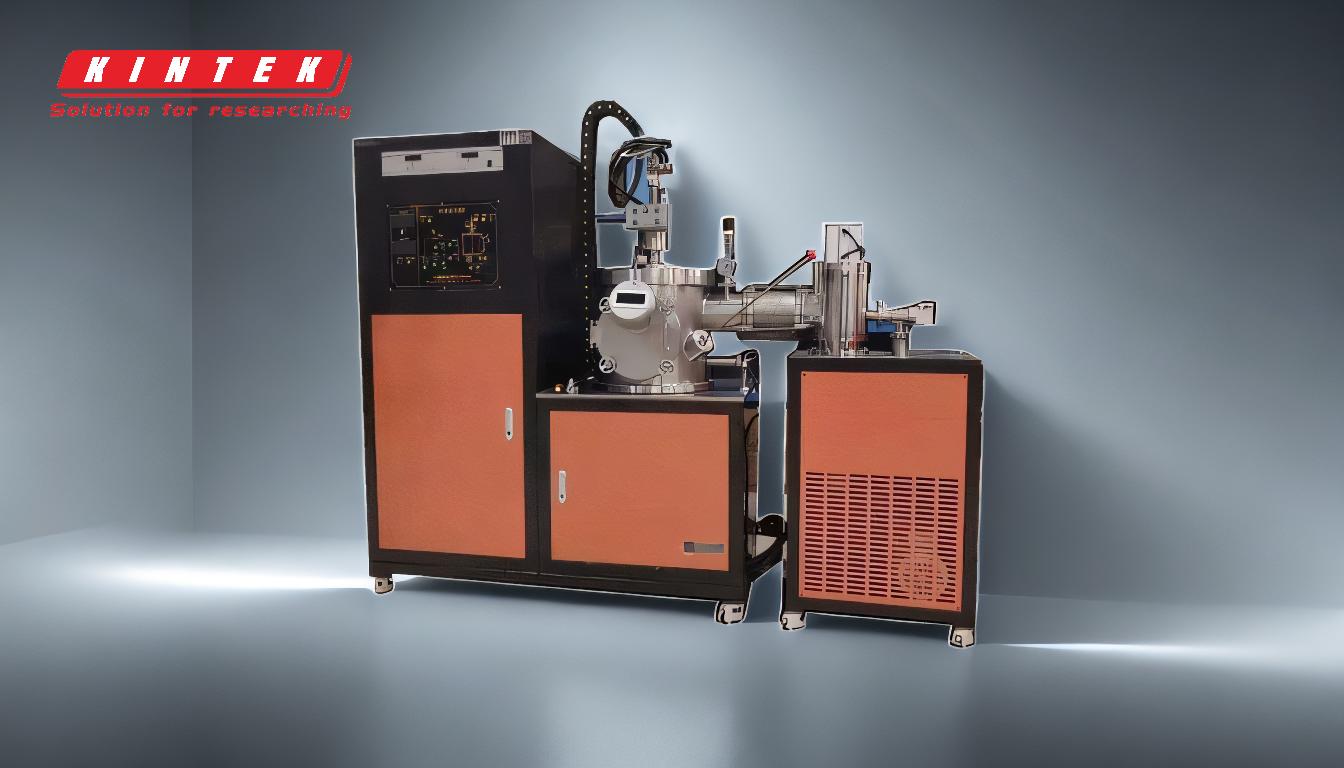
-
Purpose and Objectives:
- Annealing: The primary goal of annealing is to soften the metal, improve its ductility, and relieve internal stresses. This process makes the material easier to machine, form, or work with in subsequent manufacturing steps.
- Quenching: Quenching is aimed at increasing the hardness and strength of the metal. This is achieved by rapidly cooling the heated metal, which locks the microstructure in a hardened state, often making the material more brittle.
-
Temperature and Heating:
- Annealing: The metal is heated to a temperature above its recrystallization temperature but below its melting point. This temperature varies depending on the type of metal and the desired outcome.
- Quenching: The metal is also heated to a high temperature, typically above its critical temperature, to transform its microstructure into austenite, a phase that allows for subsequent hardening upon rapid cooling.
-
Cooling Process:
- Annealing: After heating, the metal is cooled slowly, often in a furnace or by burying it in an insulating material. This slow cooling allows the metal to form a more stable, softer microstructure.
- Quenching: The heated metal is rapidly cooled, usually by immersing it in a quenching medium such as water, oil, or air. This rapid cooling prevents the formation of softer phases and instead promotes the formation of harder structures like martensite.
-
Microstructural Changes:
- Annealing: The slow cooling process in annealing allows for the formation of larger, more uniform grains, which contribute to increased ductility and reduced hardness. Internal stresses are also relieved as the metal cools uniformly.
- Quenching: Rapid cooling in quenching results in the formation of a hard, brittle microstructure, typically martensite. This phase is characterized by a highly stressed lattice structure, which contributes to the material's increased hardness and reduced ductility.
-
Applications:
- Annealing: Commonly used in processes where the metal needs to be shaped, formed, or machined, such as in the manufacturing of wires, sheets, or forgings. It is also used to prepare metals for further heat treatment processes.
- Quenching: Often used in applications where high surface hardness and wear resistance are required, such as in the production of gears, cutting tools, and automotive components. Quenching is typically followed by tempering to reduce brittleness.
-
Effects on Mechanical Properties:
- Annealing: Increases ductility and toughness while reducing hardness and strength. This makes the metal more pliable and easier to work with.
- Quenching: Increases hardness and strength but decreases ductility and toughness. This makes the metal more resistant to wear but also more prone to cracking or breaking under impact.
-
Post-Treatment Processes:
- Annealing: Often used as a standalone process or as a preparatory step for other treatments. It does not typically require additional post-treatment.
- Quenching: Usually followed by tempering to reduce the brittleness introduced by the quenching process. Tempering involves reheating the quenched metal to a lower temperature to relieve some of the internal stresses and improve toughness.
In summary, annealing and quenching are complementary processes that serve different purposes in the heat treatment of metals. Annealing is used to soften and prepare metals for further processing, while quenching is used to harden metals for applications requiring high strength and wear resistance. Understanding the differences between these processes is crucial for selecting the appropriate heat treatment method based on the desired material properties and application requirements.
Summary Table:
Aspect | Annealing | Quenching |
---|---|---|
Purpose | Soften metal, improve ductility, relieve internal stresses | Increase hardness and strength, enhance wear resistance |
Temperature | Heated above recrystallization temperature, below melting point | Heated above critical temperature to form austenite |
Cooling Process | Slow cooling (furnace or insulating material) | Rapid cooling (water, oil, or air) |
Microstructural Change | Forms larger, uniform grains for increased ductility | Forms hard, brittle martensite for increased hardness |
Applications | Shaping, forming, machining (e.g., wires, sheets, forgings) | High wear resistance applications (e.g., gears, cutting tools) |
Mechanical Properties | Increases ductility, reduces hardness | Increases hardness, reduces ductility |
Post-Treatment | Standalone or preparatory step | Followed by tempering to reduce brittleness |
Need help selecting the right heat treatment process for your metals? Contact our experts today!