Arc melting and induction melting are two distinct methods used in metallurgical processes, each with unique mechanisms and applications. Arc melting involves using an electric arc to generate extreme heat, typically for melting refractory metals like titanium or zirconium. Induction melting, on the other hand, uses electromagnetic induction to heat and melt conductive materials, making it suitable for a wide range of metals, including steel and aluminum. The key differences lie in their heating mechanisms, energy efficiency, material compatibility, and operational control. Below, we explore these differences in detail to help you understand which method might be better suited for specific applications.
Key Points Explained:
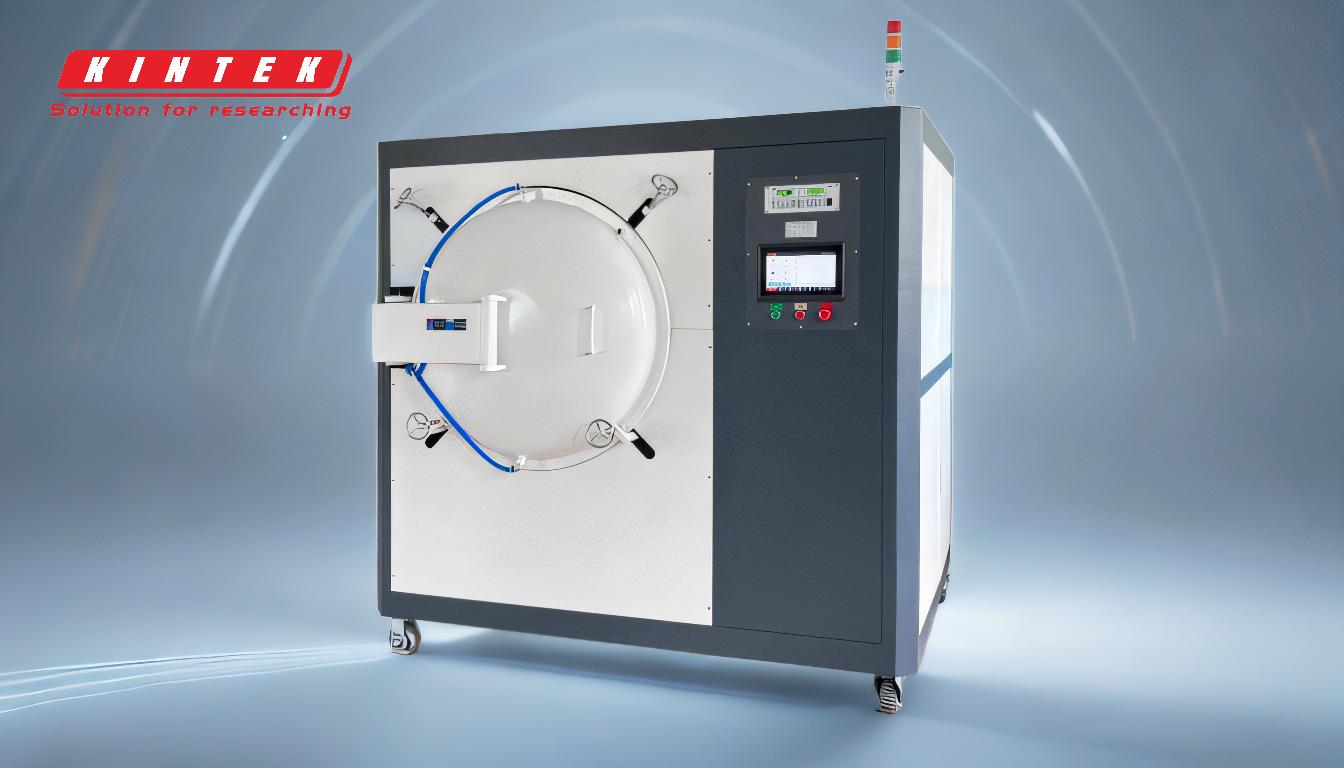
-
Heating Mechanism:
- Arc Melting: This method relies on an electric arc formed between an electrode and the material being melted. The arc generates temperatures exceeding 3,000°C, making it ideal for melting high-melting-point metals.
- Induction Melting: This process uses electromagnetic induction to create eddy currents within the material, which generate heat due to electrical resistance. It is highly efficient for melting conductive materials like steel, copper, and aluminum.
-
Energy Efficiency:
- Arc Melting: While effective for refractory metals, arc melting is less energy-efficient compared to induction melting. It often requires significant power input and can result in heat loss to the surroundings.
- Induction Melting: Induction melting is more energy-efficient because the heat is generated directly within the material, minimizing heat loss. It also allows for precise temperature control, reducing energy waste.
-
Material Compatibility:
- Arc Melting: Best suited for metals with extremely high melting points, such as titanium, zirconium, and tungsten. It is less effective for materials with lower melting points or those that are non-conductive.
- Induction Melting: Compatible with a wide range of conductive materials, including steel, aluminum, and copper alloys. It is not suitable for non-conductive materials like ceramics or glass.
-
Operational Control:
- Arc Melting: Offers limited control over the melting process, as the arc can be unstable and difficult to regulate. This makes it less suitable for applications requiring precise temperature or composition control.
- Induction Melting: Provides excellent control over the melting process, allowing for precise temperature regulation and uniform heating. This makes it ideal for applications requiring consistent material properties.
-
Applications:
- Arc Melting: Commonly used in specialized industries, such as aerospace and nuclear, where refractory metals are required. It is also used in research and development for creating high-purity alloys.
- Induction Melting: Widely used in foundries, metal casting, and recycling industries due to its versatility and efficiency. It is also used in precision manufacturing for producing high-quality metal components.
By understanding these key differences, you can make an informed decision about which melting method is best suited for your specific needs, whether you are working with refractory metals or more common conductive materials.
Summary Table:
Aspect | Arc Melting | Induction Melting |
---|---|---|
Heating Mechanism | Uses an electric arc to generate extreme heat (>3,000°C) for refractory metals. | Uses electromagnetic induction to heat conductive materials via eddy currents. |
Energy Efficiency | Less energy-efficient; significant heat loss to surroundings. | More energy-efficient; heat generated directly within the material. |
Material Compatibility | Best for high-melting-point metals (e.g., titanium, zirconium). | Suitable for conductive materials (e.g., steel, aluminum, copper). |
Operational Control | Limited control; arc can be unstable and difficult to regulate. | Precise temperature control and uniform heating for consistent results. |
Applications | Aerospace, nuclear, and R&D for high-purity alloys. | Foundries, metal casting, recycling, and precision manufacturing. |
Need help choosing the right melting method for your application? Contact our experts today for personalized guidance!