Batch furnaces and continuous furnaces differ significantly in their operation, design, and applications. Batch furnaces are closed systems that process materials in groups, making them suitable for cleanroom environments and inert atmospheres. They are simpler, easier to maintain, and have lower initial and operational costs. However, they require more preparation for loading and often need fixtures like baskets or racks. Continuous furnaces, in contrast, operate at a constant temperature with materials moving through the furnace at a steady speed. This design eliminates the need for racks or baskets, reduces energy consumption, and is ideal for high-volume production. However, they are more complex, expensive, and require frequent maintenance. The choice between the two depends on production volume, material type, and specific processing requirements.
Key Points Explained:
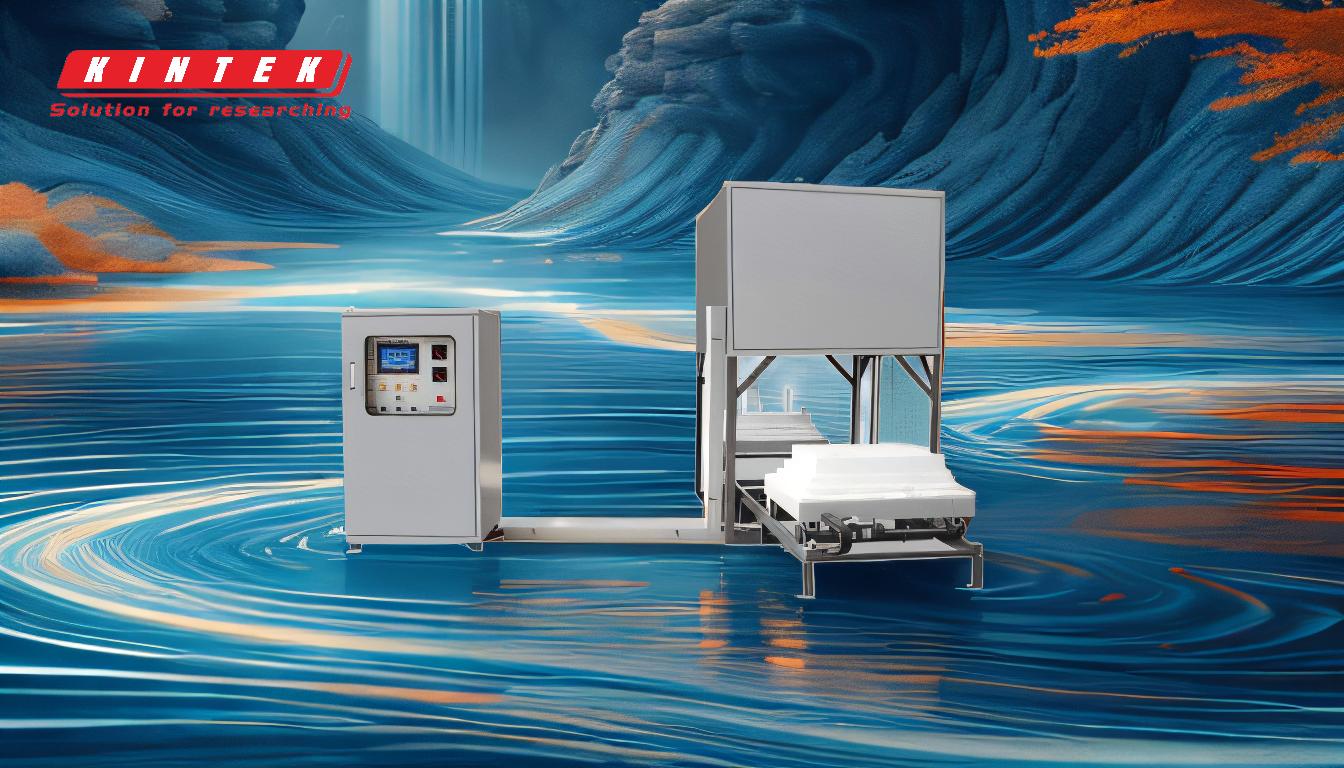
-
Operation and Design:
- Batch Furnaces: These are closed systems where materials are processed in batches. They are designed to handle multiple rolls or groups of materials at once, often requiring fixtures like baskets or racks for loading. This design is ideal for applications requiring cleanroom standards or inert atmospheres.
- Continuous Furnaces: These operate by moving materials through the furnace at a constant speed. The furnace maintains a steady temperature, and materials are processed in a single layer, eliminating the need for racks or baskets. This design is more efficient for high-volume production.
-
Complexity and Maintenance:
- Batch Furnaces: They are less complex, making them easier to maintain and repair. Their simpler design also contributes to lower initial and operational costs.
- Continuous Furnaces: These are more complex due to their continuous operation and constant temperature maintenance. This complexity leads to higher maintenance requirements and costs.
-
Cost Considerations:
- Batch Furnaces: Generally, batch furnaces have lower initial costs and are less expensive to operate over time. However, they require more work in process to prepare materials for loading.
- Continuous Furnaces: These have higher initial and operational costs due to their complexity and the need for frequent maintenance. However, they can be more cost-effective for high-volume production due to reduced energy consumption and faster processing times.
-
Energy Efficiency:
- Batch Furnaces: While they are less energy-efficient compared to continuous furnaces, their simplicity and lower operational costs can offset this disadvantage in certain applications.
- Continuous Furnaces: These are more energy-efficient due to their constant operation and the elimination of the need for racks or baskets, which reduces heat loss and energy consumption.
-
Application Suitability:
- Batch Furnaces: Ideal for applications requiring precise control over the processing environment, such as cleanroom standards or inert atmospheres. They are also suitable for smaller production runs or when processing materials that require specific handling.
- Continuous Furnaces: Best suited for high-volume production where materials need to be processed quickly and efficiently. They are commonly used in industries where continuous processing is essential, such as in the production of wire mesh or other continuous materials.
-
Material Handling:
- Batch Furnaces: Require more preparation for loading, often needing fixtures like baskets or racks. This can add to the overall processing time and labor costs.
- Continuous Furnaces: Eliminate the need for racks or baskets, as materials are processed in a single layer at a constant speed. This reduces handling time and labor costs, making them more efficient for large-scale production.
In summary, the choice between batch and continuous furnaces depends on the specific needs of the production process, including the volume of materials, the type of materials being processed, and the required processing environment. Batch furnaces offer simplicity and lower costs but require more preparation and handling, while continuous furnaces provide efficiency and energy savings at the expense of higher complexity and maintenance costs.
Summary Table:
Aspect | Batch Furnaces | Continuous Furnaces |
---|---|---|
Operation | Processes materials in batches; requires racks or baskets for loading. | Processes materials continuously at a steady speed; no racks or baskets needed. |
Complexity | Simpler design; easier to maintain and repair. | More complex; requires frequent maintenance. |
Cost | Lower initial and operational costs. | Higher initial and operational costs. |
Energy Efficiency | Less energy-efficient but offset by lower operational costs. | More energy-efficient due to constant operation. |
Applications | Ideal for cleanroom environments, inert atmospheres, and smaller production runs. | Best for high-volume production and continuous processing. |
Material Handling | Requires more preparation and fixtures for loading. | Eliminates the need for racks or baskets; reduces handling time and labor costs. |
Need help choosing the right furnace for your production needs? Contact our experts today for personalized advice!