Chemical Vapor Deposition (CVD) and Physical Vapor Deposition (PVD) are two prominent thin-film deposition techniques used across various industries, including semiconductors, optics, and coatings. While both methods aim to deposit thin films onto substrates, they differ fundamentally in their mechanisms, operating conditions, and outcomes. CVD relies on chemical reactions between gaseous precursors and the substrate to form a solid coating, offering multidirectional deposition and the ability to coat complex geometries. In contrast, PVD involves the physical vaporization of solid materials, which then condense onto the substrate in a line-of-sight manner, making it suitable for applications requiring precise, thin, and durable coatings. The choice between CVD and PVD depends on factors such as substrate material, desired coating properties, and operational constraints.
Key Points Explained:
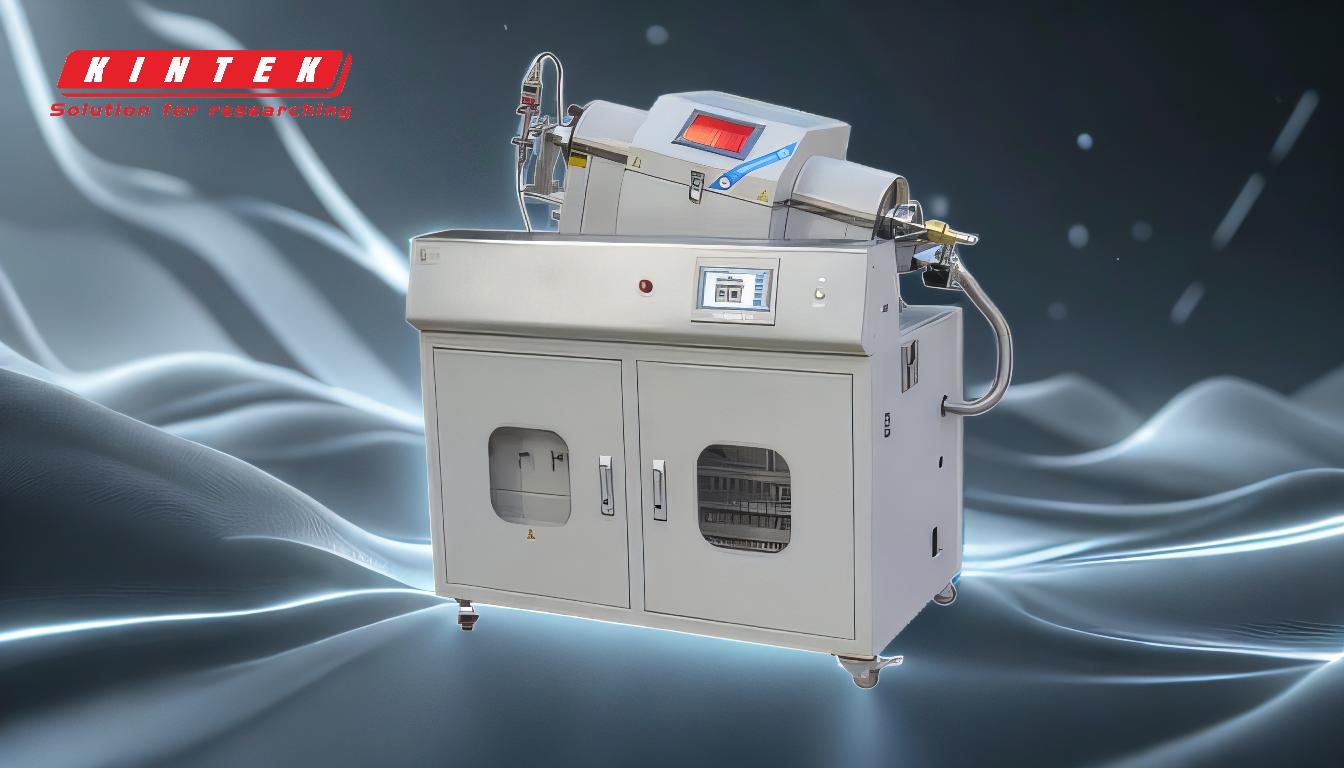
-
Deposition Mechanism:
- CVD: Involves chemical reactions between gaseous precursors and the substrate surface. The process is multidirectional, allowing uniform coating of complex shapes, deep recesses, and holes.
- PVD: Relies on physical processes such as sputtering or evaporation to vaporize solid materials, which then condense onto the substrate. This is a line-of-sight process, limiting its ability to coat non-line-of-sight areas.
-
Operating Temperatures:
- CVD: Typically operates at high temperatures (450°C to 1050°C), which can limit its use with temperature-sensitive substrates. The high temperatures also facilitate chemical reactions but may introduce impurities.
- PVD: Operates at lower temperatures (250°C to 450°C), making it suitable for temperature-sensitive materials. This also reduces the risk of thermal damage to the substrate.
-
Coating Materials:
- CVD: Primarily used for depositing ceramics and polymers. The chemical nature of the process allows for a wide range of material compositions.
- PVD: Can deposit a broader range of materials, including metals, alloys, and ceramics. This versatility makes PVD suitable for diverse applications.
-
Coating Properties:
- CVD: Produces dense, uniform, and high-quality coatings with excellent adhesion. However, the process can be slower and may result in rougher surfaces.
- PVD: Yields thin, smooth, and durable coatings with high precision. While the coatings may be less dense and uniform compared to CVD, they are often faster to apply.
-
Applications:
- CVD: Ideal for applications requiring thick coatings and the ability to coat complex geometries, such as semiconductor manufacturing and tool coatings.
- PVD: Best suited for applications needing precise, thin, and durable coatings, such as optical coatings, decorative finishes, and wear-resistant layers.
-
Advantages and Limitations:
- CVD Advantages: High throwing power, ability to coat complex shapes, and economical for thick coatings. No need for ultra-high vacuum.
- CVD Limitations: High operating temperatures, potential for corrosive byproducts, and slower deposition rates in some cases.
- PVD Advantages: Lower operating temperatures, no corrosive byproducts, and high material utilization efficiency.
- PVD Limitations: Line-of-sight deposition limits coating uniformity on complex geometries, and deposition rates are generally lower than CVD.
In summary, the choice between CVD and PVD depends on the specific requirements of the application, including substrate material, desired coating properties, and operational constraints. CVD excels in coating complex geometries and producing thick, uniform films, while PVD is preferred for precise, thin, and durable coatings on temperature-sensitive materials.
Summary Table:
Aspect | CVD | PVD |
---|---|---|
Deposition Mechanism | Chemical reactions between gaseous precursors and substrate | Physical vaporization of solid materials, condensing onto substrate |
Operating Temperatures | High (450°C to 1050°C) | Low to moderate (250°C to 450°C) |
Coating Materials | Ceramics, polymers | Metals, alloys, ceramics |
Coating Properties | Dense, uniform, high-quality | Thin, smooth, durable |
Applications | Semiconductor manufacturing, tool coatings | Optical coatings, decorative finishes, wear-resistant layers |
Advantages | Coats complex shapes, economical for thick coatings | Lower temperatures, no corrosive byproducts |
Limitations | High temperatures, slower deposition, potential impurities | Line-of-sight deposition, lower uniformity on complex geometries |
Still unsure which deposition process is right for your application? Contact our experts today for personalized guidance!