The difference between firing and sintering in ceramics lies in their processes, mechanisms, and outcomes. Firing typically refers to heating ceramic materials to high temperatures to achieve densification and strength, often involving the melting of certain components. Sintering, on the other hand, is a process where powdered materials are heated below their melting point, causing particles to bond and densify through diffusion mechanisms. Sintering is often used in advanced ceramics to achieve precise material properties without complete melting. Below, we explore the key differences in detail.
Key Points Explained:
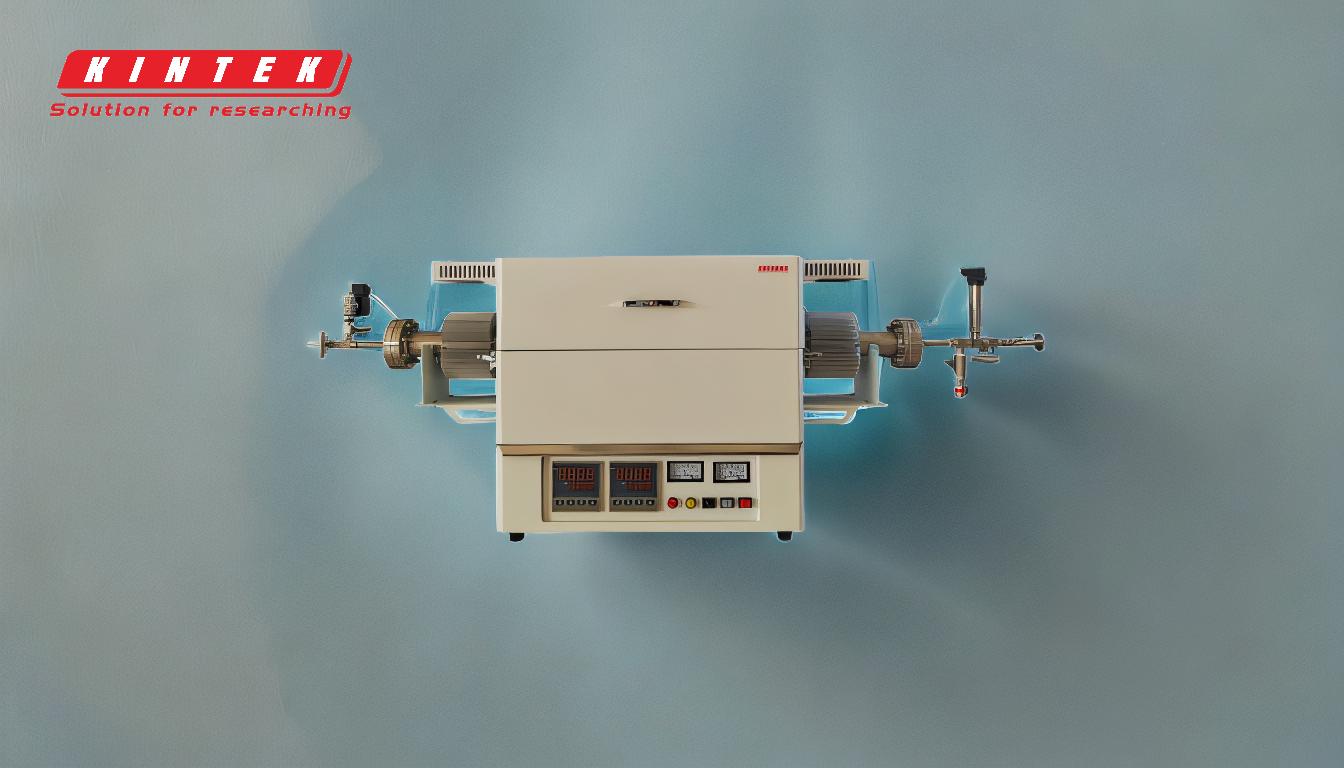
-
Definition and Purpose:
- Firing: Firing is a traditional ceramic process where materials are heated to high temperatures, often causing partial melting or vitrification. This process is used to create strong, dense ceramic products like pottery, tiles, and bricks.
- Sintering: Sintering involves heating powdered materials below their melting point, allowing particles to bond through solid-state diffusion. This method is common in advanced ceramics and materials science to achieve precise microstructures and properties.
-
Temperature Range:
- Firing: Typically occurs at higher temperatures, often close to or above the melting point of some components in the ceramic mixture.
- Sintering: Takes place at lower temperatures, below the melting point of the material, relying on diffusion and grain boundary movement for densification.
-
Mechanisms Involved:
- Firing: Involves melting, vitrification, and chemical reactions that lead to the formation of a dense, glassy phase.
- Sintering: Relies on solid-state diffusion, where atoms migrate across particle boundaries, reducing porosity and increasing density without melting.
-
Pressure Application:
- Firing: Generally does not involve external pressure; densification is achieved through heat alone.
- Sintering: Can include pressure-assisted methods like hot pressing, where pressure is applied to enhance densification. For example, in a sintering furnace, pressure can break oxide films and activate defect-driven densification.
-
Microstructure and Properties:
- Firing: Results in a more glassy and less controlled microstructure, often with larger grains and residual porosity.
- Sintering: Produces a finer, more controlled microstructure with minimal porosity, leading to improved mechanical, thermal, and electrical properties.
-
Applications:
- Firing: Used for traditional ceramics like pottery, bricks, and tiles, where high strength and durability are required.
- Sintering: Preferred for advanced ceramics, such as technical ceramics, electronic components, and biomedical implants, where precise material properties are critical.
-
Shrinkage and Densification:
- Firing: Shrinkage is often significant due to melting and vitrification, leading to denser but less controlled products.
- Sintering: Shrinkage is more controlled and predictable, with densification driven by particle rearrangement and diffusion.
-
Role of Defects:
- Firing: Defects like cracks or impurities can negatively affect the final product.
- Sintering: Crystal defects can enhance the process by activating diffusion pathways, leading to higher density and better material properties.
By understanding these differences, purchasers of equipment and consumables can make informed decisions about which process best suits their needs, whether for traditional ceramics or advanced material applications.
Summary Table:
Aspect | Firing | Sintering |
---|---|---|
Definition | Heating to high temperatures, often causing partial melting or vitrification. | Heating powdered materials below melting point, relying on solid-state diffusion. |
Temperature Range | Higher temperatures, close to or above melting point. | Lower temperatures, below melting point. |
Mechanisms | Melting, vitrification, and chemical reactions. | Solid-state diffusion and grain boundary movement. |
Pressure Application | No external pressure applied. | Can include pressure-assisted methods like hot pressing. |
Microstructure | Glassy, less controlled, larger grains, residual porosity. | Finer, controlled, minimal porosity. |
Applications | Traditional ceramics (pottery, bricks, tiles). | Advanced ceramics (technical ceramics, electronic components, implants). |
Shrinkage | Significant due to melting and vitrification. | Controlled and predictable, driven by particle rearrangement. |
Role of Defects | Defects can negatively affect the final product. | Crystal defects enhance diffusion, improving density and properties. |
Need help choosing the right process for your ceramic applications? Contact our experts today!