Injection molding and insert molding are two distinct manufacturing processes used to create plastic parts, each with its own unique applications and advantages. Injection molding involves injecting molten plastic into a mold cavity to form a part, while insert molding involves placing a pre-formed insert (often metal) into the mold before injecting plastic around it. The key difference lies in the presence of an insert in insert molding, which is not used in standard injection molding. Overmolding, a related process, involves injecting two shots of material to create a substrate and an overmold, but it differs from insert molding in that it uses multiple materials in a single process.
Key Points Explained:
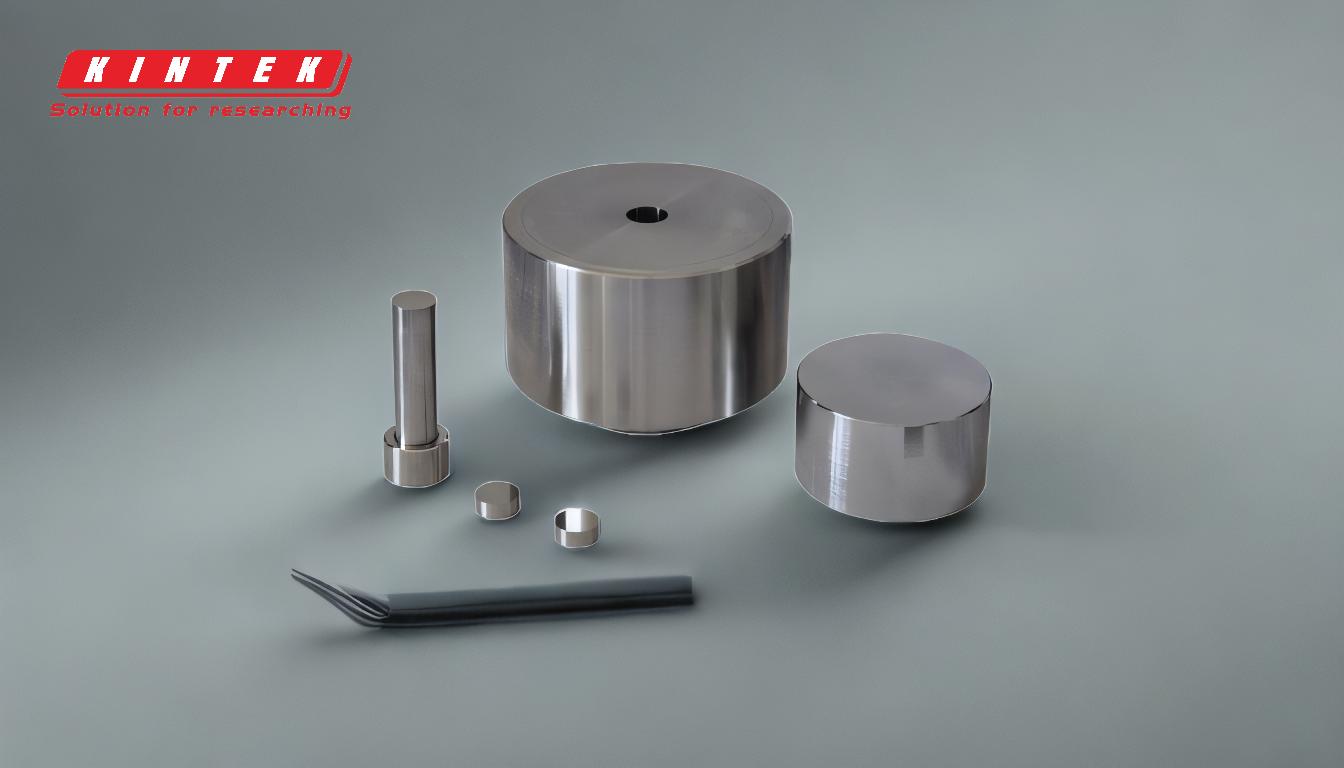
-
Definition and Process:
- Injection Molding: This is a manufacturing process where molten plastic is injected into a mold cavity under high pressure. Once the plastic cools and solidifies, the mold is opened, and the part is ejected. It is a single-material process and is widely used for producing a variety of plastic parts.
- Insert Molding: In this process, a pre-formed insert (often made of metal) is placed into the mold before the plastic is injected. The molten plastic then flows around the insert, bonding with it as it cools. This process is used to create parts that combine the properties of plastic and metal, such as threaded inserts or electrical connectors.
-
Materials Used:
- Injection Molding: Typically uses a single type of plastic material. The material is chosen based on the desired properties of the final part, such as strength, flexibility, or heat resistance.
- Insert Molding: Involves both plastic and a pre-formed insert, which can be made of metal, ceramic, or another material. The plastic is chosen to bond well with the insert, ensuring a strong and durable final product.
-
Applications:
- Injection Molding: Commonly used for producing a wide range of plastic parts, including consumer goods, automotive components, and medical devices. It is ideal for high-volume production due to its efficiency and repeatability.
- Insert Molding: Used in applications where a combination of materials is required, such as in the production of electronic components, medical devices, and automotive parts. It is particularly useful for creating parts that require metal reinforcement or specific mechanical properties.
-
Advantages:
-
Injection Molding:
- High production efficiency and repeatability.
- Ability to produce complex shapes with high precision.
- Cost-effective for large production runs.
-
Insert Molding:
- Combines the benefits of plastic and metal, resulting in parts with enhanced strength and durability.
- Reduces the need for secondary assembly operations, as the insert is molded directly into the part.
- Can improve the overall performance of the part by integrating different materials.
-
Injection Molding:
-
Challenges:
-
Injection Molding:
- Limited to single-material parts, which may not meet the requirements for certain applications.
- High initial tooling costs, which can be a barrier for small production runs.
-
Insert Molding:
- Requires precise placement of the insert, which can complicate the molding process.
- The insert must be compatible with the plastic material to ensure proper bonding.
- May involve additional costs for the inserts and more complex mold design.
-
Injection Molding:
-
Comparison with Overmolding:
- Overmolding: This process involves injecting two shots of material to create a substrate and an overmold. It is similar to insert molding in that it combines different materials, but it does so by molding one material over another in a single process. Overmolding is often used to create parts with soft grips, multi-colored components, or parts with varying material properties.
- Insert Molding: Unlike overmolding, insert molding involves a single shot of plastic material and a pre-formed insert. The insert is not molded but is placed into the mold before the plastic is injected. This process is more focused on combining plastic with other materials, such as metal, rather than layering different plastics.
-
Design Considerations:
- Injection Molding: Designers must consider factors such as wall thickness, gate location, and draft angles to ensure proper mold filling and part ejection.
- Insert Molding: Additional considerations include the placement and design of the insert, as well as the bonding between the insert and the plastic material. The insert must be designed to withstand the molding process and provide the desired mechanical properties.
In summary, while both injection molding and insert molding are used to create plastic parts, they serve different purposes and are suited to different applications. Injection molding is ideal for single-material parts produced in high volumes, while insert molding is used to create parts that combine plastic with other materials, such as metal, for enhanced performance. Understanding the differences between these processes is crucial for selecting the right manufacturing method for a given application.
Summary Table:
Aspect | Injection Molding | Insert Molding |
---|---|---|
Process | Molten plastic is injected into a mold cavity. | A pre-formed insert is placed in the mold before injecting plastic around it. |
Materials | Single plastic material. | Plastic combined with a pre-formed insert (e.g., metal). |
Applications | Consumer goods, automotive parts, medical devices. | Electronic components, medical devices, automotive parts with metal reinforcement. |
Advantages | High efficiency, precision, cost-effective for large runs. | Combines plastic and metal, reduces assembly, enhances part performance. |
Challenges | Limited to single-material parts, high tooling costs. | Precise insert placement, compatibility, and additional costs. |
Need help choosing the right molding process for your project? Contact our experts today!