Pelleting and pelletizing are two processes often used in material processing, but they differ significantly in their methods, applications, and outcomes. Pelleting typically refers to the process of compressing powdered or granular materials into small, dense pellets, often used in industries like agriculture, pharmaceuticals, and food processing. Pelletizing, on the other hand, involves forming materials into spherical or near-spherical shapes, commonly used in metallurgy, chemical industries, and recycling. Both processes aim to improve material handling, storage, and efficiency, but they employ different techniques and equipment, such as the xrf pellet press for pelleting in X-ray fluorescence analysis.
Key Points Explained:
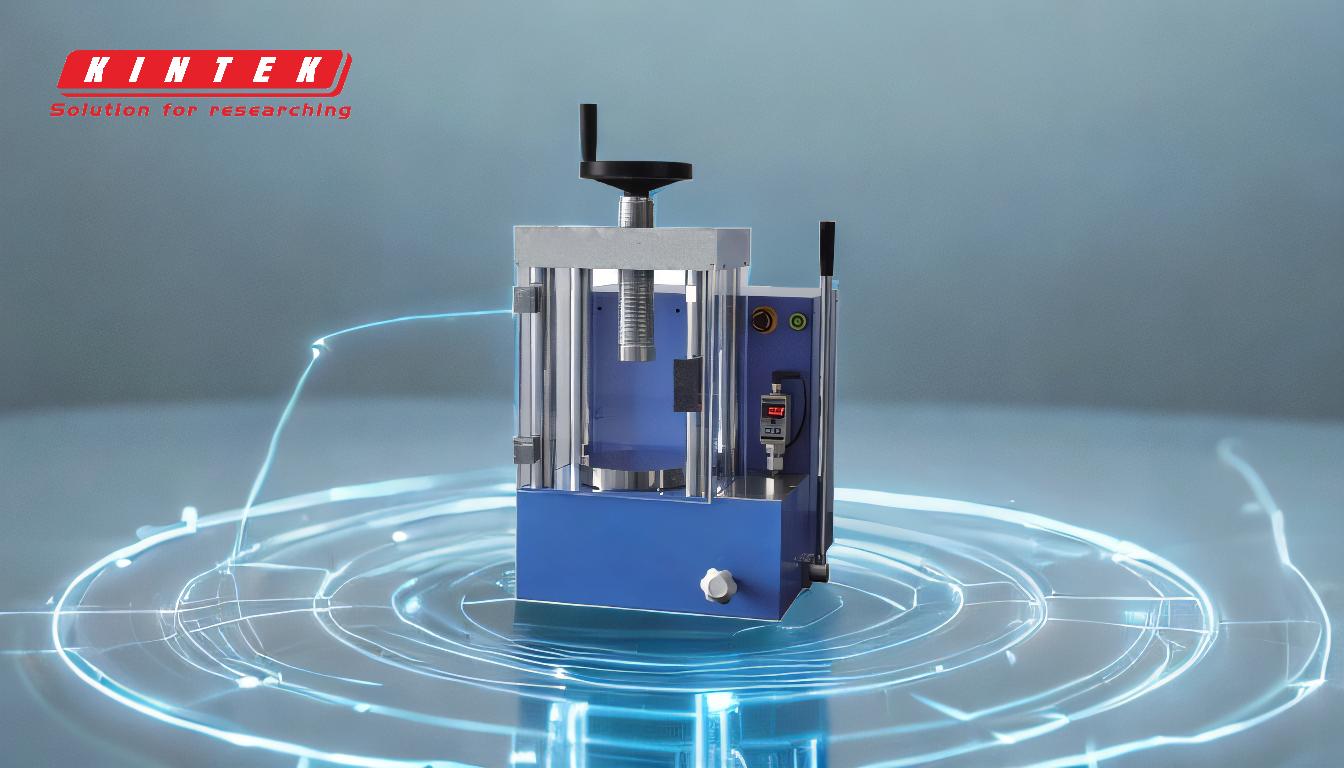
-
Definition and Purpose:
- Pelleting: This process involves compressing materials into uniform, dense pellets. It is commonly used to create feed pellets for animals, pharmaceutical tablets, or biomass fuel pellets. The goal is to improve material density, reduce dust, and enhance handling and storage efficiency.
- Pelletizing: This process involves shaping materials into spherical or near-spherical forms, often through agglomeration or extrusion. It is widely used in industries like metallurgy (e.g., iron ore pelletizing) and chemical processing. The primary purpose is to improve material flow, reduce waste, and enhance reactivity.
-
Process and Techniques:
- Pelleting: Typically involves mechanical compression using equipment like pellet mills or xrf pellet presses. The material is forced through a die under high pressure to form uniform pellets. Binders or lubricants may be added to improve pellet integrity.
- Pelletizing: Often involves agglomeration techniques such as tumbling, extrusion, or spray drying. The material is shaped into spheres through rolling or coating processes, sometimes with the addition of binders or heat to achieve the desired form.
-
Applications:
- Pelleting: Commonly used in agriculture (animal feed), pharmaceuticals (tablets), and energy (biomass pellets). It is also essential in analytical chemistry, where xrf pellet presses are used to prepare samples for X-ray fluorescence analysis.
- Pelletizing: Primarily used in metallurgy (iron ore pellets), chemical industries (catalyst pellets), and recycling (plastic pelletizing). It is also employed in food processing (e.g., snack pellets) and environmental applications (e.g., waste pelletizing).
-
Equipment Used:
- Pelleting: Requires specialized equipment like pellet mills, extruders, or xrf pellet presses. These machines apply high pressure to compress materials into pellets.
- Pelletizing: Utilizes equipment like disc pelletizers, drum pelletizers, or extruders. These machines shape materials into spherical forms through rolling, tumbling, or extrusion.
-
Material Characteristics:
- Pelleting: Produces dense, uniform pellets with consistent size and shape. The process enhances material durability and reduces dust generation.
- Pelletizing: Produces spherical or near-spherical pellets with improved flow properties and surface area. The process enhances material reactivity and handling efficiency.
-
Advantages:
- Pelleting: Improves material density, reduces dust, and enhances storage and transportation efficiency. It also ensures uniformity in size and shape, which is critical for applications like XRF analysis.
- Pelletizing: Enhances material flow, reduces waste, and improves reactivity. It is particularly beneficial for materials that require uniform size and shape for further processing.
-
Challenges:
- Pelleting: Requires precise control of pressure and binder content to achieve uniform pellets. The process can be energy-intensive and may require specialized equipment.
- Pelletizing: Requires careful control of agglomeration techniques and binder content to achieve the desired spherical shape. The process may also involve additional steps like drying or curing.
In summary, while both pelleting and pelletizing aim to improve material handling and efficiency, they differ in their methods, applications, and outcomes. Pelleting focuses on compression to create dense, uniform pellets, while pelletizing involves shaping materials into spherical forms. Understanding these differences is crucial for selecting the appropriate process and equipment, such as the xrf pellet press, for specific applications.
Summary Table:
Aspect | Pelleting | Pelletizing |
---|---|---|
Definition | Compressing materials into dense, uniform pellets. | Shaping materials into spherical or near-spherical forms. |
Purpose | Improves density, reduces dust, and enhances storage efficiency. | Enhances material flow, reduces waste, and improves reactivity. |
Process | Mechanical compression using pellet mills or XRF pellet presses. | Agglomeration techniques like tumbling, extrusion, or spray drying. |
Applications | Agriculture (animal feed), pharmaceuticals, biomass fuel, XRF analysis. | Metallurgy (iron ore), chemical industries, recycling, food processing. |
Equipment | Pellet mills, extruders, XRF pellet presses. | Disc pelletizers, drum pelletizers, extruders. |
Material Outcome | Dense, uniform pellets with consistent size and shape. | Spherical or near-spherical pellets with improved flow properties. |
Advantages | Enhances durability, reduces dust, and ensures uniformity. | Improves material flow, reduces waste, and enhances reactivity. |
Challenges | Requires precise pressure control and can be energy-intensive. | Needs careful control of agglomeration techniques and binder content. |
Need help choosing the right process for your material? Contact our experts today for personalized advice!