Roll bending and roll forming are two distinct metalworking processes used to shape metal sheets or plates, but they differ significantly in their methods, applications, and outcomes. Roll bending involves curving metal sheets or plates into cylindrical or curved shapes using a set of rollers, while roll forming is a continuous process that shapes metal strips into complex cross-sectional profiles by passing them through a series of rollers. Roll bending is typically used for creating large-radius curves or cylinders, such as tanks or pipes, whereas roll forming is ideal for producing long, uniform profiles like metal roofing, gutters, or automotive components. The choice between the two depends on the desired shape, material thickness, and production requirements.
Key Points Explained:
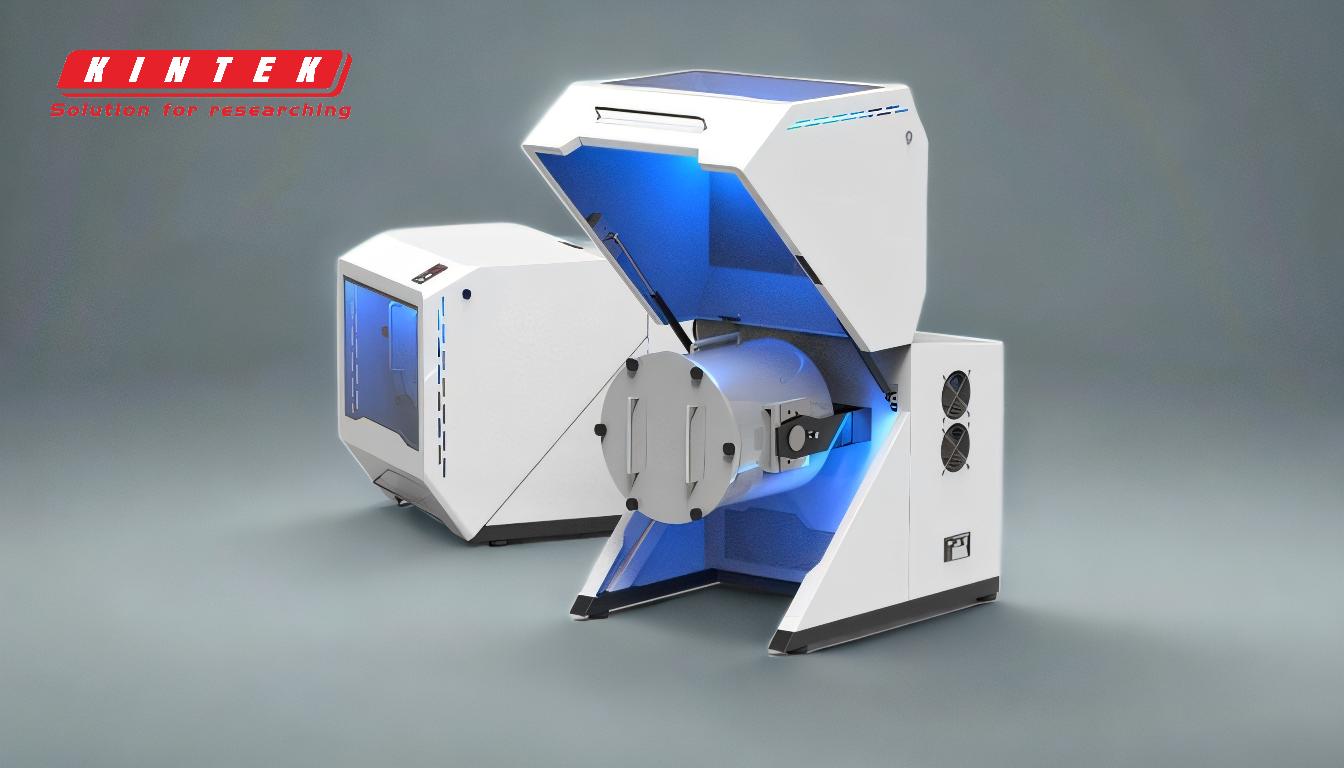
-
Definition and Process:
- Roll Bending: This process involves passing a metal sheet or plate through a set of rollers to create a curved or cylindrical shape. The rollers apply pressure to bend the material gradually, and the curvature can be adjusted by controlling the roller positions.
- Roll Forming: In this process, a continuous metal strip is fed through a series of rollers, each performing a small incremental bend. The cumulative effect of these bends creates a complex cross-sectional profile. Roll forming is a continuous process, making it suitable for high-volume production.
-
Applications:
- Roll Bending: Commonly used for creating large-radius curves, cylinders, or conical shapes. Typical applications include manufacturing tanks, pipes, and structural components like arches or hoops.
- Roll Forming: Ideal for producing long, uniform profiles with consistent cross-sections. Applications include metal roofing, gutters, automotive parts, and construction materials like steel studs or tracks.
-
Material Thickness and Shape Complexity:
- Roll Bending: Best suited for thicker materials and simpler shapes, such as large-radius bends or cylinders. It is less effective for creating intricate profiles.
- Roll Forming: Capable of handling thinner materials and producing complex cross-sectional shapes with high precision. The process is highly versatile for creating detailed profiles.
-
Production Speed and Volume:
- Roll Bending: Generally slower and more suited for custom or low-volume production due to the manual adjustments required for each bend.
- Roll Forming: A high-speed, continuous process designed for mass production. It is efficient for producing large quantities of uniform parts.
-
Equipment and Tooling:
- Roll Bending: Requires specialized machinery with adjustable rollers to accommodate different material thicknesses and bend radii.
- Roll Forming: Involves custom tooling with multiple roller sets, each designed to perform a specific bend or shape. The tooling is tailored to the desired profile.
-
Advantages and Limitations:
- Roll Bending: Offers flexibility for creating large-radius curves and is suitable for thicker materials. However, it is less efficient for high-volume production and complex shapes.
- Roll Forming: Provides high precision and consistency for complex profiles and is ideal for mass production. However, the initial setup and tooling costs can be higher, and it is less adaptable to custom or one-off designs.
-
Material Considerations:
- Both processes can work with a variety of metals, including steel, aluminum, and stainless steel. However, the choice of material may influence the selection of the process based on its thickness, ductility, and intended application.
In summary, roll bending and roll forming serve different purposes in metalworking. Roll bending is ideal for creating large-radius curves and cylindrical shapes, while roll forming excels at producing complex, uniform profiles for high-volume applications. The choice between the two depends on the specific requirements of the project, including the desired shape, material properties, and production volume.
Summary Table:
Aspect | Roll Bending | Roll Forming |
---|---|---|
Process | Curves metal sheets into cylindrical or curved shapes using rollers. | Shapes metal strips into complex profiles through a series of incremental bends. |
Applications | Tanks, pipes, arches, hoops. | Metal roofing, gutters, automotive parts, steel studs. |
Material Thickness | Best for thicker materials. | Handles thinner materials. |
Shape Complexity | Simpler shapes (e.g., large-radius curves). | Complex cross-sectional profiles. |
Production Speed | Slower, suited for custom/low-volume production. | High-speed, ideal for mass production. |
Equipment | Adjustable rollers for varying thicknesses and bend radii. | Custom tooling with multiple roller sets for specific profiles. |
Advantages | Flexible for large-radius curves, suitable for thicker materials. | High precision, consistent profiles, ideal for high-volume production. |
Limitations | Less efficient for complex shapes and high-volume production. | Higher setup costs, less adaptable for custom designs. |
Need help choosing the right metalworking process? Contact our experts today for tailored solutions!