Short-path distillation and thin-film (or wiped-film) distillation are both advanced separation techniques used in various industries, but they differ significantly in their working principles, structural designs, efficiency, and applications. Short-path distillation relies on the differences in molecular free paths under high vacuum conditions, allowing for separation without heating to the boiling point, while thin-film distillation depends on differences in boiling points and requires higher temperatures. Structurally, short-path distillation features an internal condenser with a minimal distance between the heating and condensing surfaces, enabling high-purity separation but at a higher cost. In contrast, thin-film distillation uses mechanical wipers to create a thin film of material on a heated surface, reducing heat exposure and increasing productivity, making it more suitable for large-scale operations. Both methods have unique advantages and limitations, making them suitable for different industrial needs.
Key Points Explained:
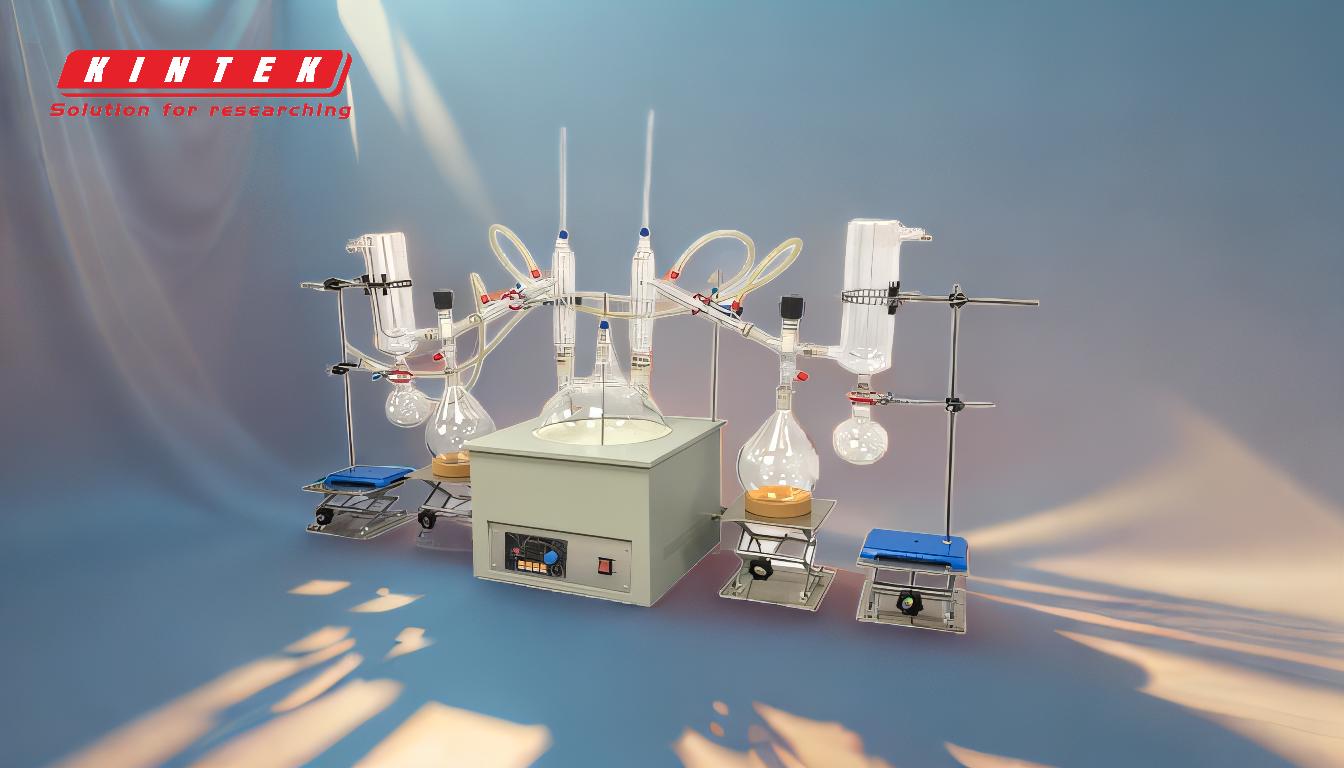
-
Working Principles:
-
Short-Path Distillation:
- Operates under high vacuum conditions.
- Separates components based on differences in molecular free paths, avoiding the need to heat materials to their boiling points.
- Ideal for heat-sensitive materials due to minimal thermal degradation.
-
Thin-Film Distillation:
- Relies on differences in boiling points for separation.
- Requires higher temperatures, which may not be suitable for heat-sensitive compounds.
- Uses mechanical wipers to spread the material into a thin film, enhancing heat transfer and evaporation efficiency.
-
Short-Path Distillation:
-
Structural Differences:
-
Short-Path Distillation:
- Equipped with an internal condenser, reducing the distance between the heating and condensing surfaces.
- Minimizes pressure drop during condensation, improving efficiency.
- Collects distillate from the bottom, ensuring high purity.
-
Thin-Film Distillation:
- Features an external condenser, which may result in a longer path for vapor travel.
- Recycles materials from the top, which can reduce purity but increases throughput.
- Designed for scalability, making it more suitable for large-scale production.
-
Short-Path Distillation:
-
Efficiency and Productivity:
-
Short-Path Distillation:
- Yields high-purity products due to the short vapor path and minimal pressure drop.
- Limited in scale and production capacity, making it more suitable for small-scale, high-value applications.
- Higher operational costs due to the complexity of the system and the need for high vacuum conditions.
-
Thin-Film Distillation:
- Reduces the exposure time of materials to heat, minimizing thermal degradation.
- Higher productivity and better suited for large-scale operations.
- Lower operational costs compared to short-path distillation, but may sacrifice some purity.
-
Short-Path Distillation:
-
Applications:
-
Short-Path Distillation:
- Ideal for applications requiring high-purity separation, such as pharmaceutical, chemical, and essential oil industries.
- Suitable for heat-sensitive materials that cannot withstand high temperatures.
-
Thin-Film Distillation:
- Commonly used in industries requiring large-scale production, such as petrochemical, food, and biodiesel production.
- Effective for processing viscous materials with high boiling points.
-
Short-Path Distillation:
-
Cost and Scalability:
-
Short-Path Distillation:
- Higher initial and operational costs due to the need for high vacuum and precise temperature control.
- Limited scalability, making it less cost-effective for large-scale production.
-
Thin-Film Distillation:
- More cost-effective for large-scale operations due to higher throughput and lower energy requirements.
- Easier to scale up, making it a preferred choice for industrial applications.
-
Short-Path Distillation:
In summary, the choice between short-path and thin-film distillation depends on the specific requirements of the application, including the desired purity, scale of production, and sensitivity of the materials being processed. Short-path distillation excels in high-purity, small-scale applications, while thin-film distillation is better suited for large-scale, high-throughput operations.
Summary Table:
Aspect | Short-Path Distillation | Thin-Film Distillation |
---|---|---|
Working Principle | Uses molecular free paths under high vacuum | Relies on boiling point differences |
Temperature | Minimal heating, ideal for heat-sensitive materials | Requires higher temperatures |
Structure | Internal condenser, short vapor path | External condenser, mechanical wipers |
Efficiency | High purity, limited scale | High throughput, scalable |
Applications | Pharmaceuticals, essential oils, chemicals | Petrochemicals, food, biodiesel production |
Cost | Higher initial and operational costs | More cost-effective for large-scale operations |
Still unsure which distillation method is best for your needs? Contact our experts today for personalized guidance!