Tempering and sintering are two distinct heat treatment processes used in materials science, each serving different purposes and involving unique mechanisms. Tempering is primarily used to reduce brittleness in hardened steel by reheating it to a temperature below its critical point, followed by controlled cooling. This process enhances toughness while maintaining hardness. Sintering, on the other hand, is a process of compacting and forming a solid mass of material by heat or pressure without melting it to the point of liquefaction. It is commonly used in powder metallurgy to create solid objects from powdered materials, improving strength and density. While both processes involve heating, their goals, mechanisms, and applications differ significantly.
Key Points Explained:
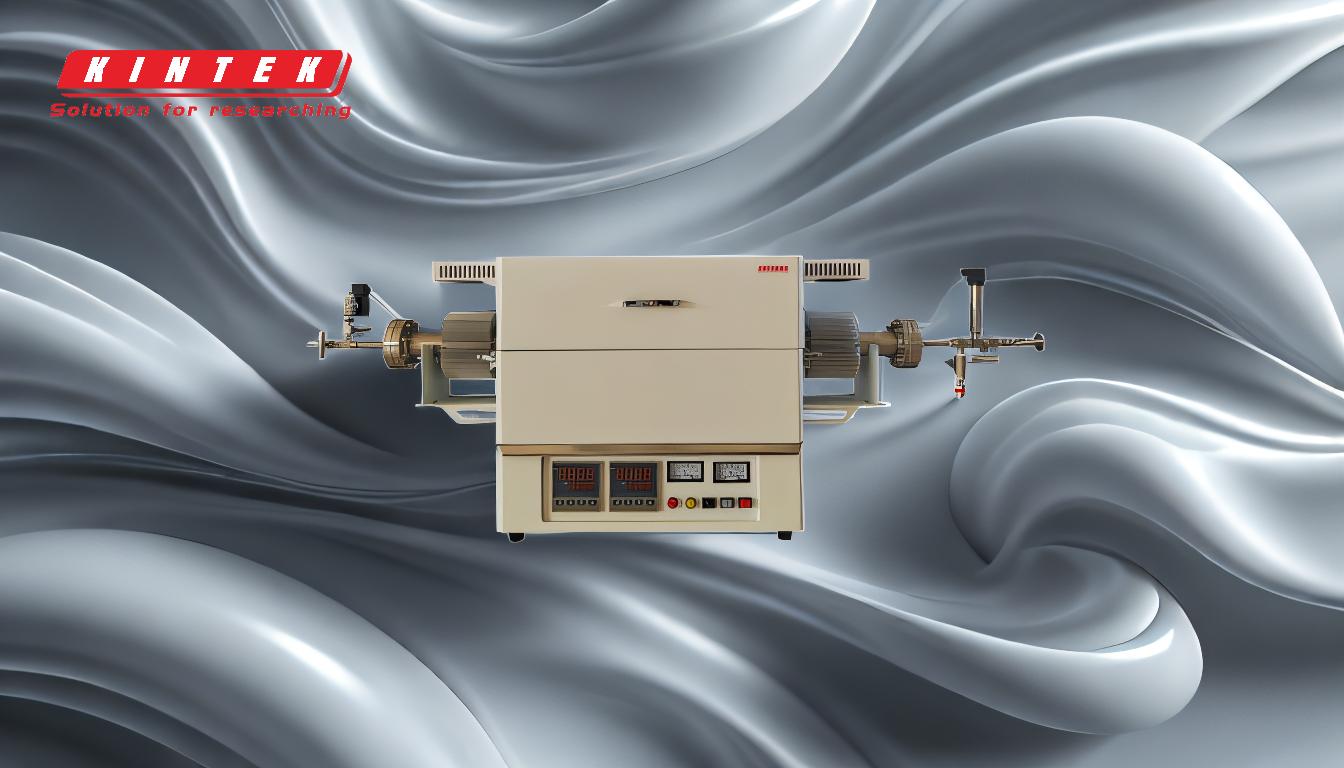
-
Definition and Purpose:
- Tempering: A heat treatment process applied to hardened steels to reduce brittleness and improve toughness. It involves reheating the material to a temperature below its critical point and then cooling it in a controlled manner.
- Sintering: A process used to create solid objects from powdered materials by applying heat and/or pressure. It is commonly used in powder metallurgy to improve the strength, density, and structural integrity of the material.
-
Temperature and Mechanism:
- Tempering: Typically occurs at temperatures between 150°C to 650°C (302°F to 1202°F), depending on the desired properties. The process involves the transformation of martensite (a hard, brittle phase) into tempered martensite, which is tougher and less brittle.
- Sintering: Involves heating the material to a temperature below its melting point, usually between 70% to 90% of the melting temperature. The particles bond together through diffusion, reducing porosity and increasing density without liquefying the material.
-
Material State:
- Tempering: Applied to already hardened materials, typically steels that have undergone quenching. The goal is to modify the microstructure to achieve a balance between hardness and toughness.
- Sintering: Applied to powdered materials, often metals, ceramics, or composites. The goal is to consolidate the powder into a solid mass with improved mechanical properties.
-
Microstructural Changes:
- Tempering: Results in the decomposition of martensite into ferrite and cementite, which reduces internal stresses and improves ductility and toughness.
- Sintering: Leads to the bonding of particles at their contact points, reducing porosity and increasing the density and strength of the material. The microstructure becomes more homogeneous and cohesive.
-
Applications:
- Tempering: Commonly used in the manufacturing of tools, gears, springs, and other components that require a balance of hardness and toughness. It is essential in applications where the material must withstand impact and wear.
- Sintering: Widely used in the production of metal components, ceramics, and composite materials. It is particularly important in industries such as automotive, aerospace, and electronics, where complex shapes and high-performance materials are required.
-
Advantages and Limitations:
-
Tempering:
- Advantages: Improves toughness and reduces brittleness without significantly sacrificing hardness. Enhances the overall durability of the material.
- Limitations: May reduce the hardness of the material if not carefully controlled. The process is limited to materials that have been previously hardened.
-
Sintering:
- Advantages: Allows for the production of complex shapes and near-net-shape components with minimal material waste. Can be used with a wide range of materials, including metals, ceramics, and composites.
- Limitations: The process can be time-consuming and may require additional finishing steps to achieve the desired surface quality. The initial cost of powder materials can be high.
-
Tempering:
-
Process Control:
- Tempering: Requires precise control of temperature and cooling rates to achieve the desired mechanical properties. Over-tempering can lead to excessive softening, while under-tempering may not sufficiently reduce brittleness.
- Sintering: Involves careful control of temperature, pressure, and atmosphere to ensure proper bonding of particles. The sintering atmosphere (e.g., vacuum, inert gas) is critical to prevent oxidation and contamination.
In summary, tempering and sintering are both critical heat treatment processes in materials science, but they serve different purposes and involve distinct mechanisms. Tempering is focused on improving the toughness of hardened materials, while sintering is aimed at consolidating powdered materials into solid objects with enhanced properties. Understanding the differences between these processes is essential for selecting the appropriate treatment for specific applications and materials.
Summary Table:
Aspect | Tempering | Sintering |
---|---|---|
Purpose | Reduces brittleness in hardened steel, improves toughness. | Consolidates powdered materials into solid objects, improves strength and density. |
Temperature Range | 150°C to 650°C (302°F to 1202°F). | 70% to 90% of the material's melting point. |
Material State | Applied to hardened materials (e.g., steel). | Applied to powdered materials (e.g., metals, ceramics). |
Microstructural Change | Decomposes martensite into ferrite and cementite. | Bonds particles, reduces porosity, and increases density. |
Applications | Tools, gears, springs, and components requiring hardness and toughness. | Automotive, aerospace, and electronics industries for complex shapes. |
Advantages | Improves toughness without sacrificing hardness. | Produces complex shapes with minimal material waste. |
Limitations | May reduce hardness if not controlled; limited to hardened materials. | Time-consuming; may require additional finishing steps. |
Need help choosing the right heat treatment process for your materials? Contact our experts today!