Sintering is a critical process in materials science, where powdered materials are heated to form a solid mass without melting. The density of the final product is a key outcome of sintering, influenced by various factors such as temperature, pressure, particle size, and sintering atmosphere. Higher density generally leads to improved mechanical properties like tensile strength and fatigue resistance. However, achieving optimal density requires careful control of sintering parameters. For instance, higher temperatures and finer particle sizes can enhance densification, but excessive temperatures or improper pressure can lead to defects. The sintering process is also affected by the initial porosity of the material and the sintering environment, such as vacuum or controlled atmospheres. Understanding these factors is essential for producing high-quality sintered materials with desired properties.
Key Points Explained:
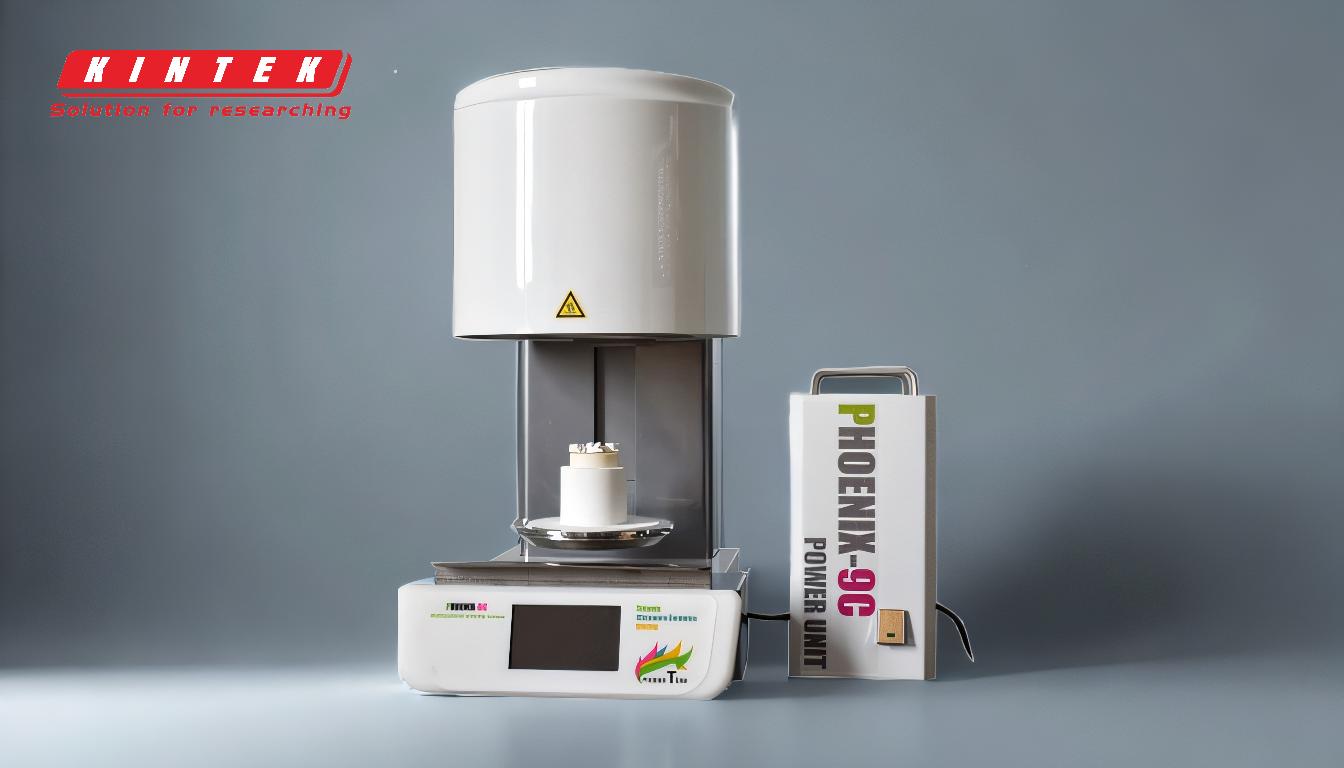
-
Density and Mechanical Properties:
- Higher density in sintered materials typically results in improved mechanical properties, such as tensile strength, bending fatigue strength, and impact energy.
- Density is influenced by the sintering temperature, with higher temperatures generally promoting better densification.
- However, excessive temperatures can lead to undesirable grain growth or defects, which may compromise mechanical properties.
-
Temperature and Sintering Kinetics:
- Temperature is a critical factor in sintering, as it determines the kinetics of particle diffusion and bonding.
- Higher temperatures accelerate particle diffusion, leading to increased densification and reduced porosity.
- The optimal sintering temperature depends on the material being used and the desired final density.
-
Particle Size and Initial Porosity:
- Smaller particle sizes promote better densification due to increased surface area and enhanced particle contact.
- The initial porosity of the green compact (pre-sintered material) also plays a significant role in determining the final density.
- Materials with lower initial porosity tend to achieve higher final densities after sintering.
-
Pressure and Particle Rearrangement:
- Applying pressure during sintering can enhance particle rearrangement and eliminate porosity, leading to higher density.
- Pressure-assisted sintering techniques, such as hot pressing or spark plasma sintering, are often used to achieve near-theoretical densities.
-
Sintering Atmosphere:
- The sintering atmosphere (e.g., air, vacuum, or inert gases like argon/nitrogen) can significantly affect the final density.
- A controlled atmosphere prevents oxidation or contamination, which can interfere with particle bonding and densification.
- Vacuum sintering is particularly effective for materials that are sensitive to oxidation.
-
Sintering Time and Cooling Rate:
- The duration of the sintering process and the cooling rate also influence the final density.
- Longer sintering times allow for more complete particle diffusion and bonding, but excessively long times can lead to grain growth.
- Controlled cooling rates help in maintaining the desired microstructure and density.
-
Material Composition:
- The composition of the material being sintered affects its sintering behavior.
- Homogeneous compositions and the presence of a liquid phase (in liquid-phase sintering) can promote better densification.
- However, the amount of liquid phase must be carefully controlled to avoid defects.
-
Sintering Techniques:
- Different sintering techniques, such as conventional sintering, hot pressing, or spark plasma sintering, offer varying levels of control over density.
- The choice of technique depends on the material properties and the desired final product characteristics.
-
Practical Considerations:
- In industrial sintering, factors such as layer thickness, machine speed, and sintering endpoint are carefully controlled to achieve consistent density.
- For example, in sintering ores, the air volume, vacuum, and layer thickness are optimized to ensure uniform sintering and desired density.
By understanding and controlling these factors, manufacturers can tailor the sintering process to achieve the desired density and properties in the final product. This knowledge is crucial for producing high-performance materials for various applications, from automotive components to electronic devices.
Summary Table:
Factor | Influence on Density |
---|---|
Temperature | Higher temps enhance densification; excessive temps cause defects. |
Particle Size | Smaller particles increase surface area, improving densification. |
Pressure | Pressure aids particle rearrangement, reducing porosity. |
Sintering Atmosphere | Controlled atmospheres (e.g., vacuum) prevent oxidation, improving density. |
Sintering Time | Longer times allow complete diffusion; excessive times risk grain growth. |
Material Composition | Homogeneous materials and controlled liquid phases enhance densification. |
Sintering Techniques | Techniques like hot pressing or spark plasma sintering achieve higher densities. |
Optimize your sintering process for superior material density—contact our experts today!