The heat generated in a hydraulic system can have significant effects on its performance, efficiency, and longevity. Excessive heat can lead to fluid degradation, reduced viscosity, and increased wear on components, ultimately compromising the system's reliability. Proper thermal management is crucial to maintain optimal operating conditions and prevent overheating. Understanding the sources of heat, its impact on hydraulic fluid and components, and strategies to mitigate it are essential for ensuring the system's efficiency and durability.
Key Points Explained:
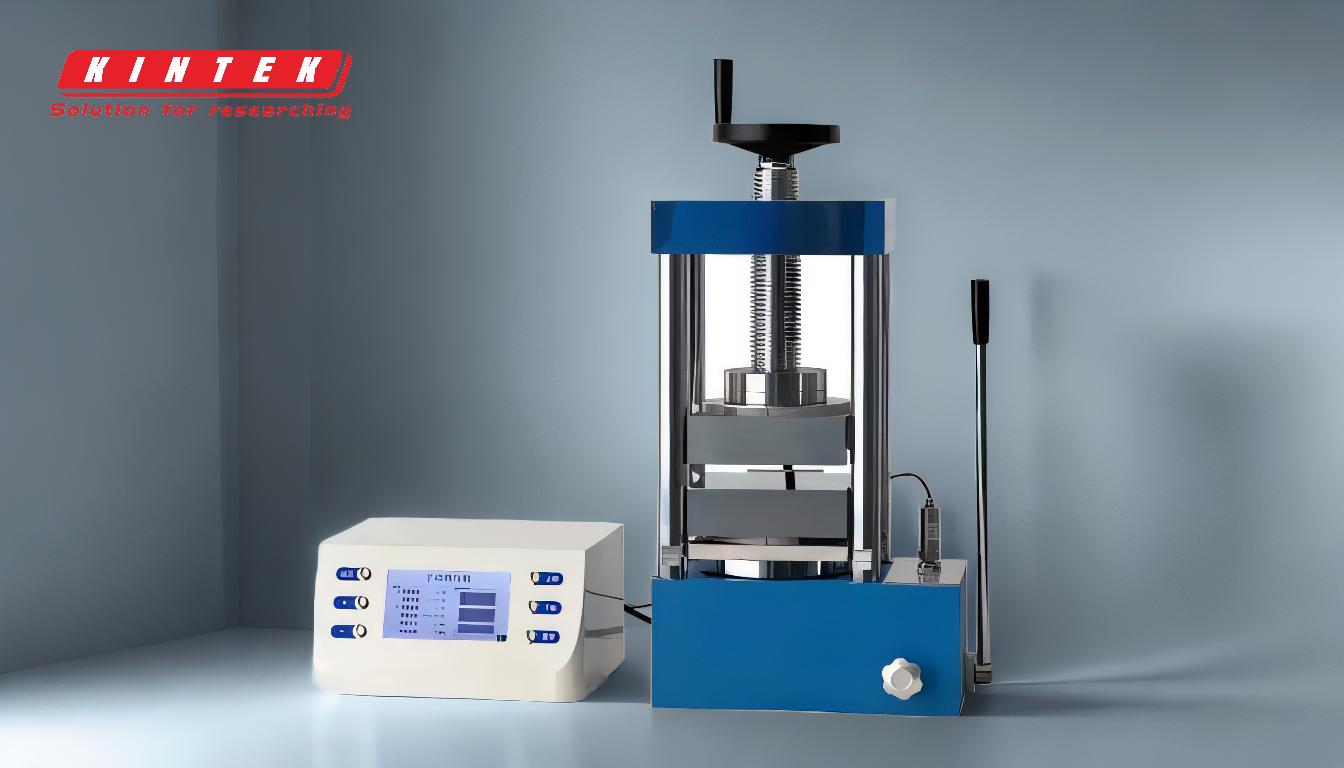
-
Sources of Heat in Hydraulic Systems:
- Heat in hydraulic systems is primarily generated through energy losses during operation. These losses occur due to:
- Friction: Internal friction within the hydraulic fluid and between moving parts, such as pumps, valves, and cylinders, generates heat.
- Pressure Drops: When hydraulic fluid flows through narrow passages or restrictions, pressure drops occur, converting energy into heat.
- Inefficiencies in Components: Components like pumps and motors are not 100% efficient; some energy is lost as heat during operation.
- Heat in hydraulic systems is primarily generated through energy losses during operation. These losses occur due to:
-
Effects of Heat on Hydraulic Fluid:
- Excessive heat can significantly alter the properties of hydraulic fluid, leading to:
- Reduced Viscosity: High temperatures cause the fluid to thin out, reducing its ability to lubricate components effectively. This can lead to increased wear and tear.
- Oxidation and Degradation: Heat accelerates the oxidation process, causing the fluid to break down and form sludge, varnish, and acids. These byproducts can clog filters and damage system components.
- Reduced Lubrication: As the fluid degrades, its lubricating properties diminish, increasing friction and wear on moving parts.
- Excessive heat can significantly alter the properties of hydraulic fluid, leading to:
-
Impact on System Components:
- Heat can adversely affect the performance and lifespan of hydraulic system components, including:
- Seals and Hoses: High temperatures can cause seals and hoses to harden, crack, or fail, leading to leaks and reduced system efficiency.
- Pumps and Valves: Excessive heat can cause thermal expansion, leading to misalignment and increased wear in pumps and valves.
- Bearings and Gears: Heat can reduce the effectiveness of lubrication, leading to increased friction and wear in bearings and gears.
- Heat can adversely affect the performance and lifespan of hydraulic system components, including:
-
Consequences of Overheating:
- If heat is not managed properly, it can lead to several operational issues, such as:
- Reduced Efficiency: Overheating can cause the system to operate less efficiently, requiring more energy to perform the same tasks.
- Increased Maintenance Costs: Frequent overheating can lead to more frequent maintenance and replacement of components, increasing operational costs.
- System Failure: In extreme cases, excessive heat can cause catastrophic failure of the hydraulic system, resulting in downtime and costly repairs.
- If heat is not managed properly, it can lead to several operational issues, such as:
-
Strategies to Mitigate Heat Generation:
- To prevent overheating and maintain optimal system performance, several strategies can be employed:
- Proper Sizing of Components: Ensuring that pumps, valves, and other components are correctly sized for the system can reduce energy losses and heat generation.
- Use of Heat Exchangers: Installing heat exchangers or coolers can help dissipate excess heat from the hydraulic fluid, maintaining it at an optimal temperature.
- Regular Maintenance: Regularly checking and replacing hydraulic fluid, filters, and worn components can help prevent overheating and extend the system's lifespan.
- System Design Optimization: Designing the hydraulic system with minimal pressure drops and efficient flow paths can reduce heat generation.
- To prevent overheating and maintain optimal system performance, several strategies can be employed:
-
Monitoring and Control:
- Implementing monitoring and control systems can help manage heat levels in hydraulic systems:
- Temperature Sensors: Installing temperature sensors allows for real-time monitoring of hydraulic fluid temperature, enabling timely intervention if overheating occurs.
- Thermostatic Controls: Using thermostatic controls can help regulate the temperature of the hydraulic fluid by activating cooling systems when necessary.
- Implementing monitoring and control systems can help manage heat levels in hydraulic systems:
In conclusion, heat generation in hydraulic systems is an inevitable byproduct of their operation, but its effects can be managed through proper design, maintenance, and monitoring. By understanding the sources of heat, its impact on the system, and implementing strategies to mitigate it, operators can ensure the longevity and efficiency of their hydraulic systems.
Summary Table:
Aspect | Impact of Heat |
---|---|
Hydraulic Fluid | Reduced viscosity, oxidation, degradation, and loss of lubrication. |
System Components | Seals and hoses harden, pumps and valves misalign, bearings and gears wear faster. |
Operational Consequences | Reduced efficiency, increased maintenance costs, and potential system failure. |
Mitigation Strategies | Proper component sizing, heat exchangers, regular maintenance, and system design. |
Ensure your hydraulic system runs efficiently and lasts longer—contact our experts today for tailored solutions!